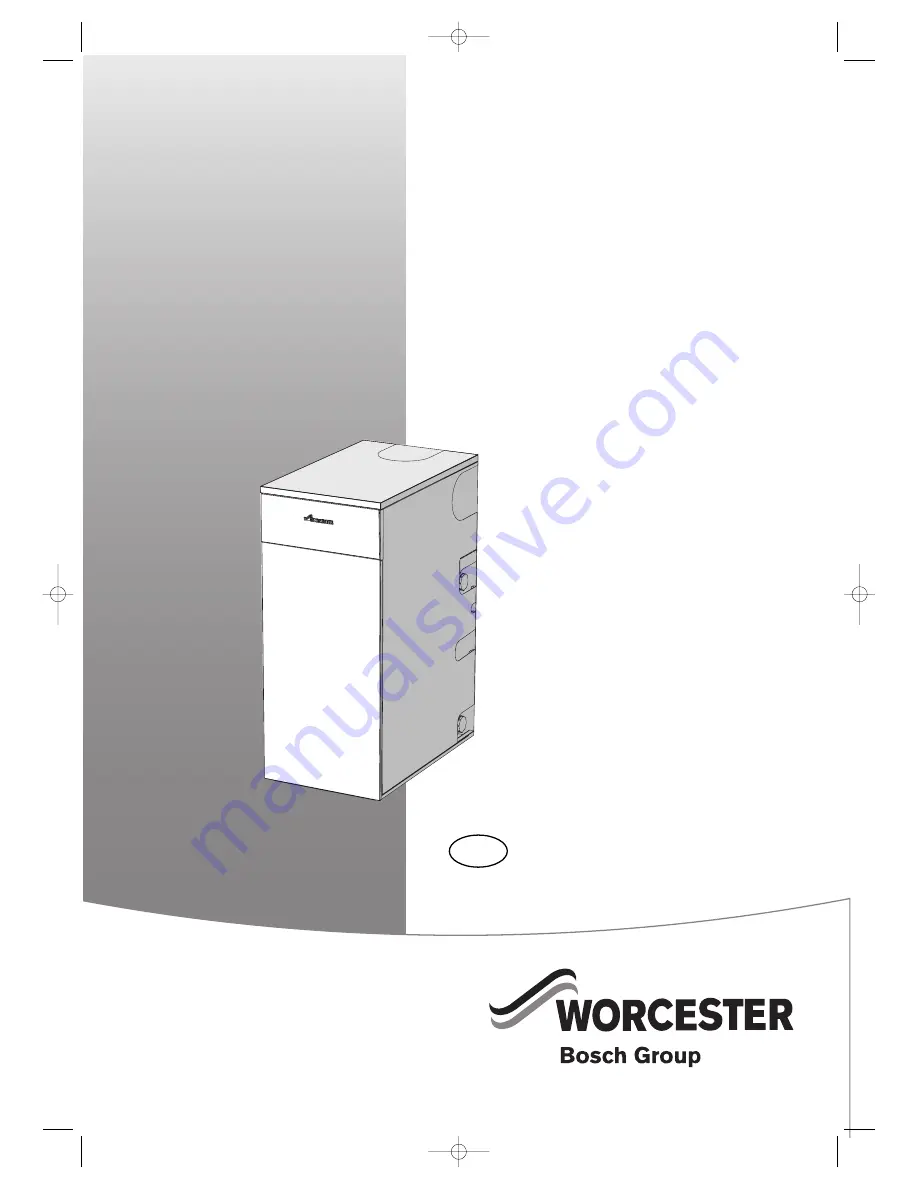
INSTRUCTION MANUAL
INSTALLATION, COMMISSIONING & SERVICING
FLOOR STANDING OIL FIRED CONDENSING BOILER CONVENTIONAL
FLUE & ROOM SEALED FLUE
GREENSTAR UTILITY
18/25
FOR FULLY PUMPED OPEN VENT OR SEALED CENTRAL HEATING SYSTEMS
AND DOMESTIC HOT WATER CYLINDERS
UK
THE APPLIANCE IS FOR USE WITH KEROSENE
(28 SECOND OIL) ONLY
8 716 106 256 C 03.10 30/3/10 14:24 Page 1