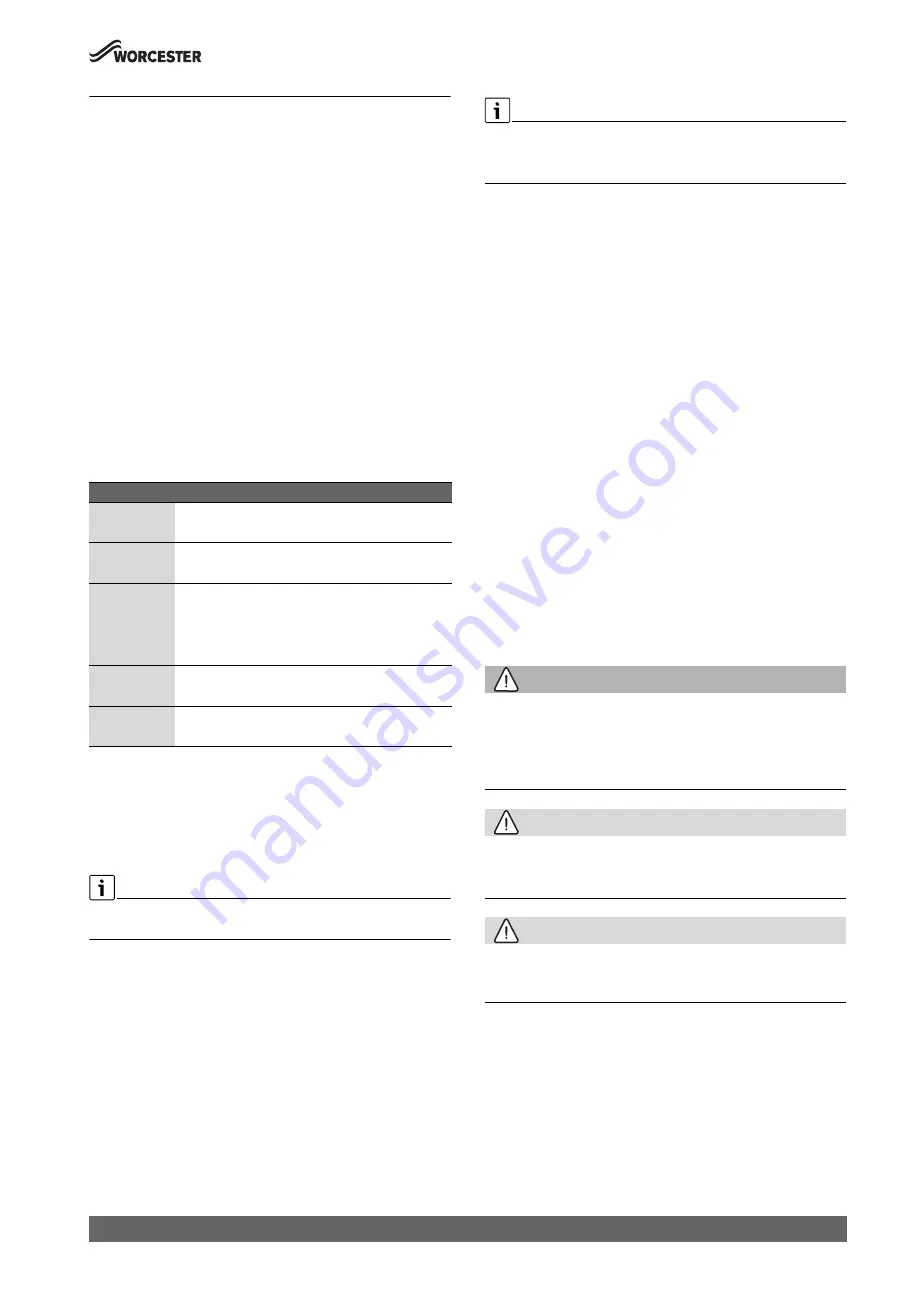
Malfunction or failure
15
Greenstar 4000 – 6 720 891 171 (2020/09)
9
Malfunction or failure
If you believe there is a problem with your central heating or hot water
supply, before you contact your installer/maintenance engineer and
report the error and appliance type carry out the following checks.
Basic checks
Some items to check before placing a call are:
• Is the electrical power switched on to the appliance?
• Is the programmer/timer set to ON or in an ON period?
• Is the room thermostat set too low?
• Is the cylinder thermostat (if fitted) set too low?
• Is the cold water main turned on?
• Sealed heating system:
– Is the static system pressure (when appliance is cold) between
1 and 1.5 bar?
• Do you have gas?
– Are other gas appliances working, gas cooker/hob for example?
– Has your credit run out on your gas pre-payment meter?
Details of your installer should be available in the Commissioning
Checklist or can be recorded in the following section.
Installer/maintenance engineer
Table 9
Worcester, Bosch Group
The appliance is supported in the UK and Eire by Worcester, Bosch
Group.
Specialist service engineers are available to attend an appliance
breakdown.
Invoices for attendance and repair work carried out on this appliance by
any third party will not be accepted.
• No charge will be made for parts and/or labour providing:
– The appliance fault is found and the appliance is within the
guarantee period. Reasonable evidence of this must be supplied
on request. i.e. a completed Commissioning and service record
and has been regularly serviced at least once a year.
• A call-out charge will be made where:
– The appliance is outside the guarantee period or has not been
serviced in accordance with the manufacturers instructions.
– Our Field Service Engineer finds no fault with the appliance.
– The cause of breakdown is misuse or with other parts of your
plumbing/heating system, or with equipment not supplied by
Worcester, Bosch Group.
No appliance fault is found on over 30% of all service calls.
▶ In the case of a suspected fault, refer to the basic checks earlier in this
section.
In the event of an appliance fault or breakdown please contact
Worcester, Bosch Group appointments team on 0330 123 9339. Your
advisor will arrange for an engineer to call with the minimum of delay;
under normal circumstances this will be from 1‒3 working days
(excluding weekends and bank holidays) for priority breakdown
situations (no hot water and/or heating).
9.1
Troubleshooting (fault reset)
If there is fault in the system, there will be a message shown on the
display with an icon on the right up corner. The color of this icon depends
on the severity of the fault in the system. The cause of the fault is coded
(e.g. fault code 232) and displayed as text.
▶ Press the
and
keys until
Reset
is displayed.
The appliance starts up again and the current supply temperature is
displayed.
If a fault persists:
▶ Contact the contractor or the customer service.
▶ Provide them with the displayed fault code and the device data
(
9.2
Extreme cold weather
In certain instances where the condensate pipe work is run externally or
in an unheated area, such as a garage, the condensate pipe work can be
at risk of freezing, even if well insulated.
A frozen/blocked condensate pipe will cause the boiler to shut down.
Worcester, Bosch Group have available helpful videos on thawing frozen
condensate pipe work on our website in the Customer service section.
WARNING
Falling hazard!
Failure to follow this guidance may result in personal injury.
▶ Only attempt to thaw a condensate pipe that is at ground level and
easily accessible.
▶ Never attempt to thaw a condensate pipe that is at height.
CAUTION
Risk of damage to pipe work!
Thermal shock from boiling water can damage plastic pipes.
▶
DO NOT
use boiling water to thaw the condensate pipe!
CAUTION
Slip hazard
▶ Ensure that the subsequent freezing of any water does not result in a
slip hazard.
If the condensate pipe has frozen:
▶ Locate the blockage.
– It is likely that the pipe is frozen at the most exposed point outside
the building or where there is an obstruction to flow. This could be
the open end of the pipe, at a bend or elbow, or where there is a
sag in the pipe in which condensate can collect.
– The location of the blockage should be identified as closely as
possible before taking further action.
Installer/maintenance engineer details
Engineer name:
Company
name:
Company
address:
Telephone:
Email: