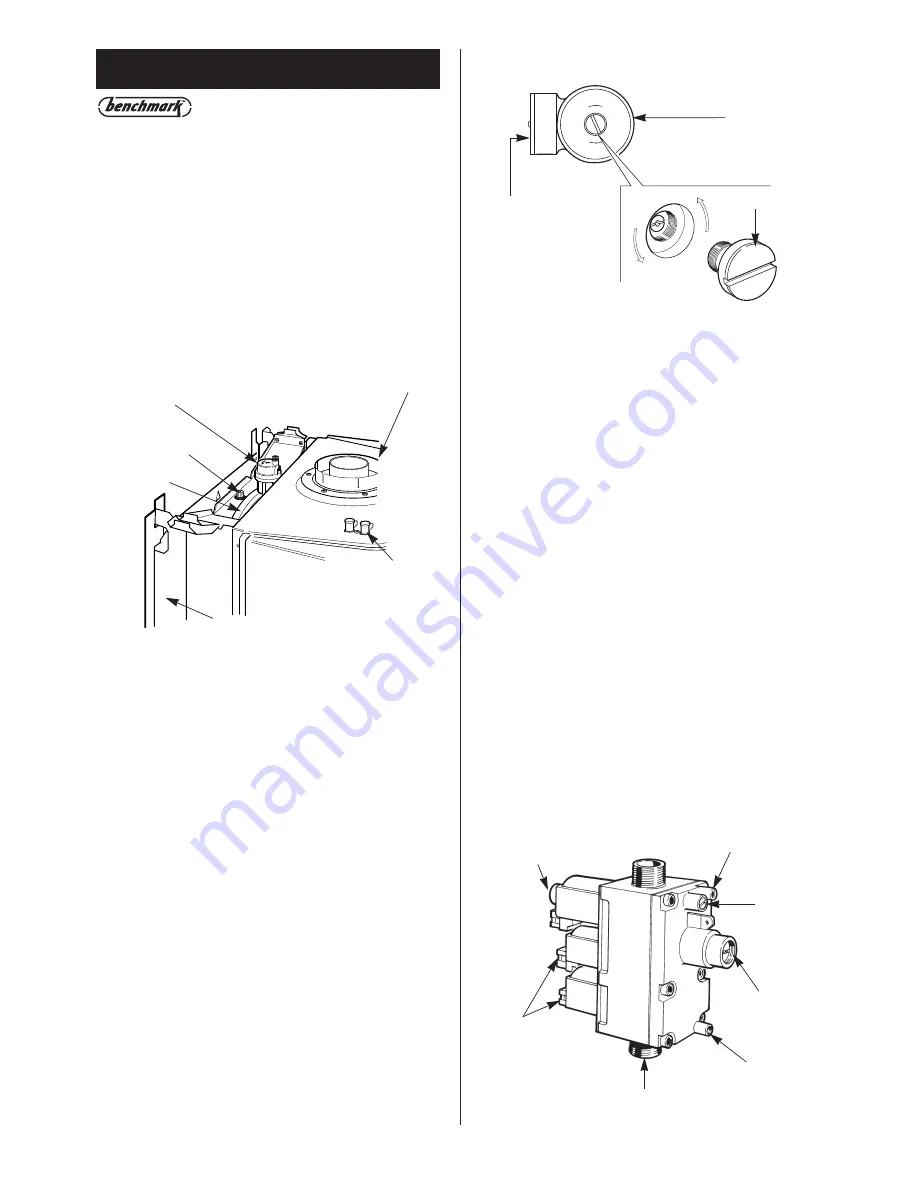
Benchmark Water Treatment: For optimum performance after
installation, this boiler and its associated central heating
system should be flushed in accordance with the guidelines
given in BS7593:1992 - Treatment of water in domestic hot
water systems. Full instructions are supplied with proprietary
cleansers sold for this purpose. If an inhibitor is to be used
after flushing, it should be used in accordance with the
inhibitor manufacturers instructions.
Suitable flushing agents and inhibitors are available from Betz
Dearborn Tel: 0151 4209563 and Fernox Tel: 01799 550811.
Instructions for use are supplied with these products.
12.1
Remove the appliance cabinet by removing the screw at
the top centre of the cabinet.
Check that the electrical supply and the gas supply to the
appliance are turned off and that all the water connections
throughout the system are tight.
Open the system valves at the appliance. Refer to Fig.6.
Open all the radiator valves. Remove the automatic air vent cap.
Refer to Fig. 34.
Fill the system through the external filling loop. Refer to Section
7, Sealed System.
Vent each radiator in turn. The automatic air vent will vent the
appliance. Refer to Fig 34.
Remove the cap from the pump and turn the shaft about half a
turn. Replace the cap. Refer to Fig 35.
Check that the pressure relief valve operates by turning the knob
anti-clockwise until it releases. Lower the facia to gain access to
the relief valve. Refer to Fig 17. Water should be expelled from
the discharge pipe.
12.2
Set the Expansion Vessel Pressure
The charge pressure of the expansion vessel as dispatched is
0.5bar, which is equivalent to a static head of 5m [17ft]. The
charge pressure must not be less than the static head at the
point of connection. A Schraeder type valve is fitted to the
expansion vessel to allow the charge pressure to be increased if
necessary. Refer to Fig 34. The expansion vessel must be charged
to 0.35bar less than the initial system design pressure.
Note: 1bar = 10.2m = 33.5ft of water.
12.3
Set the System Pressure
Fill the system until the pressure gauge is at 2.5bar and check for
leaks.
Release water from the system using the relief valve test knob
until the required system pressure is obtained, upto a maximum
of 1.5bar.
Set the pointer on the pressure gauge to record the set system
pressure.
If the pressure indicated on the gauge is greater than 2.65bar
when operating at the maximum central heating temperature,
an extra expansion vessel must be fitted to the system as close
as possible to the appliance central heating return connection.
The appliance [as despatched] can accommodate a system
volume of 100 litres with a system pressure of 0.5bar. Refer to
BS7074 Part 1, BS5449 and Table 8. If the system volume is
greater then an extra vessel must be fitted as close as possible to
the appliance central heating return connection and pressurised
to the same figure as the integral vessel.
12.4
Clock/Programmer: The controls fitted to the appliance
should be set up at this stage.
12.5
Check that the gas and electricity supplies are turned off.
Connect a pressure gauge to the gas valve burner pressure test
point. Refer to Fig 36.
12. Commissioning The Appliance
18
Fig.34. Automatic air vent and combustion
test point
Fig. 35. Pump venting.
Pump
Pump
cap
Electrical
connections
cover
Fig. 36. Gas valve.
Modulating
solenoid
valve
Burner pres-
sure test
point
Burner con-
nection
Safety sole-
noid valves
Gas
Inlet pressure
test point
Minimum
pressure
adjustment
screw
Maximum
pressure
adjustment
screw
Automatic air vent
Flue connections
Expansion vessel charg-
ing point
Expansion vessel
Wall mounting frame
Combustion products
test point (front cap)