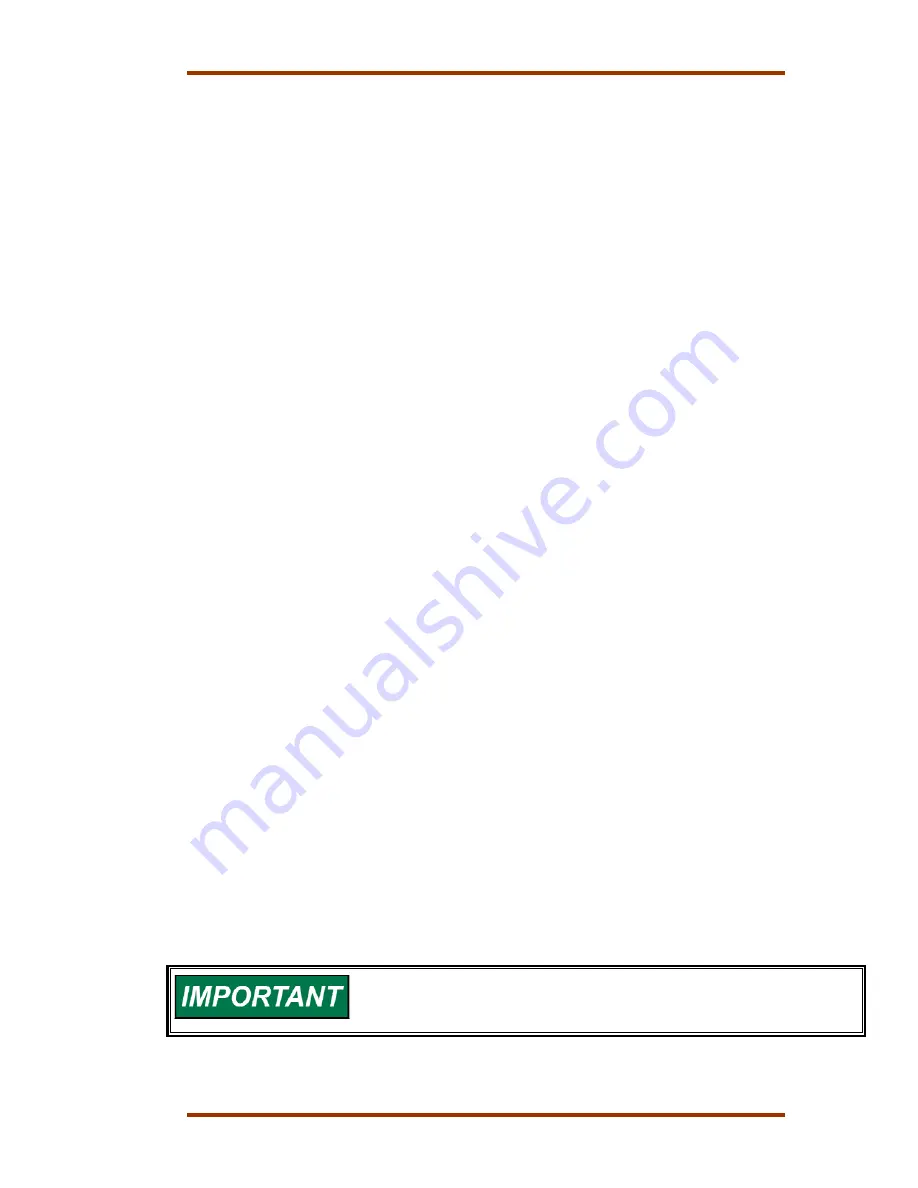
Manual 03040
UG Dial Governor
Woodward
13
As the ballhead (23) rotates, the flyweights (24) pivot outward due to the
centrifugal force. At the same time the speeder spring (25) forces the thrust
bearing (30) downward on the flyweight toes. This downward force opposes the
centrifugal force of the flyweights. Increasing the drive speed increases the
centrifugal force. Compressing the speeder spring (25) with the speeder plug
(29) increases the downward force applied to the flyweight toes, and in turn,
increases the governor speed setting. The prime mover must run faster to
generate a centrifugal force greater than the speeder spring force to balance the
system again.
Speeder spring force or speed setting (25) is controlled manually through the
synchronizer (speed setting) adjusting knob (5). It can also be controlled from a
remote area if the governor is equipped with a speed setting motor (1).
Compensation System
The purpose of the compensation system is to give stability to the governor and
obtain steady state speed control. Also, when correctly adjusted, the
compensation system effectively regulates the amount of fuel necessary to bring
the engine to the required output to adjust to a decrease or increase in load.
The compensation system creates a small temporary change of speed setting
with governor output shaft movement to produce a stabilizing speed droop
characteristic in the governor. The change of speed setting is followed by a slow
return of speed setting to its original value. Compensation is simply another word
for temporary speed droop characteristic.
The compensation system includes a large dashpot compensation piston (34), a
small dashpot compensation piston (35), a floating lever (31), a compensation
adjusting lever (22) with a pivotable fulcrum (18), and a needle valve (33). See
Figure 3-1.
The large dashpot compensation piston (34) is connected to the governor output
shaft (6) by a compensation adjusting lever (22). A pivotable fulcrum (18) rides
on the compensation adjusting lever (22). Changing the fulcrum’s (18) position
allows the compensation lever (22) to control the amount of stroke available for
the large dashpot compensation piston (34).
The small dashpot compensation piston (35) is connected through a floating
lever (31) to the pilot valve plunger (39) and the speeder rod (21).
Moving the large dashpot compensation piston (34) down forces oil under the
small dashpot compensation piston (35). As the small dashpot compensation
piston (35) is forced upward, it lifts the pilot valve plunger (39) to close off the
control port which stops the flow of oil to the bottom of the power piston (9).
The needle valve (33) is a variable orifice which controls the flow of oil between
both the large (34) and the small dashpot compensation (35) pistons, and the oil
sump.
Compensation must be properly adjusted to the particular engine
and load to provide stable operation (see Chapter 4, Compensation
Adjustments).
Summary of Contents for UG-10 Dial
Page 5: ...Manual 03040 UG Dial Governor Woodward iii...
Page 6: ...UG Dial Governor Manual 03040 iv Woodward Figure 1 1 UG 8 Dial Governor...
Page 9: ...Manual 03040 UG Dial Governor Woodward 3 Figure 1 3 UG Dial Governor Outline Drawing...
Page 14: ...UG Dial Governor Manual 03040 8 Woodward Table 2 1 Oil Chart Table 2 2 Viscosity Comparisons...
Page 18: ...UG Dial Governor Manual 03040 12 Woodward Figure 3 1 UG Dial Governor Schematic Diagram...