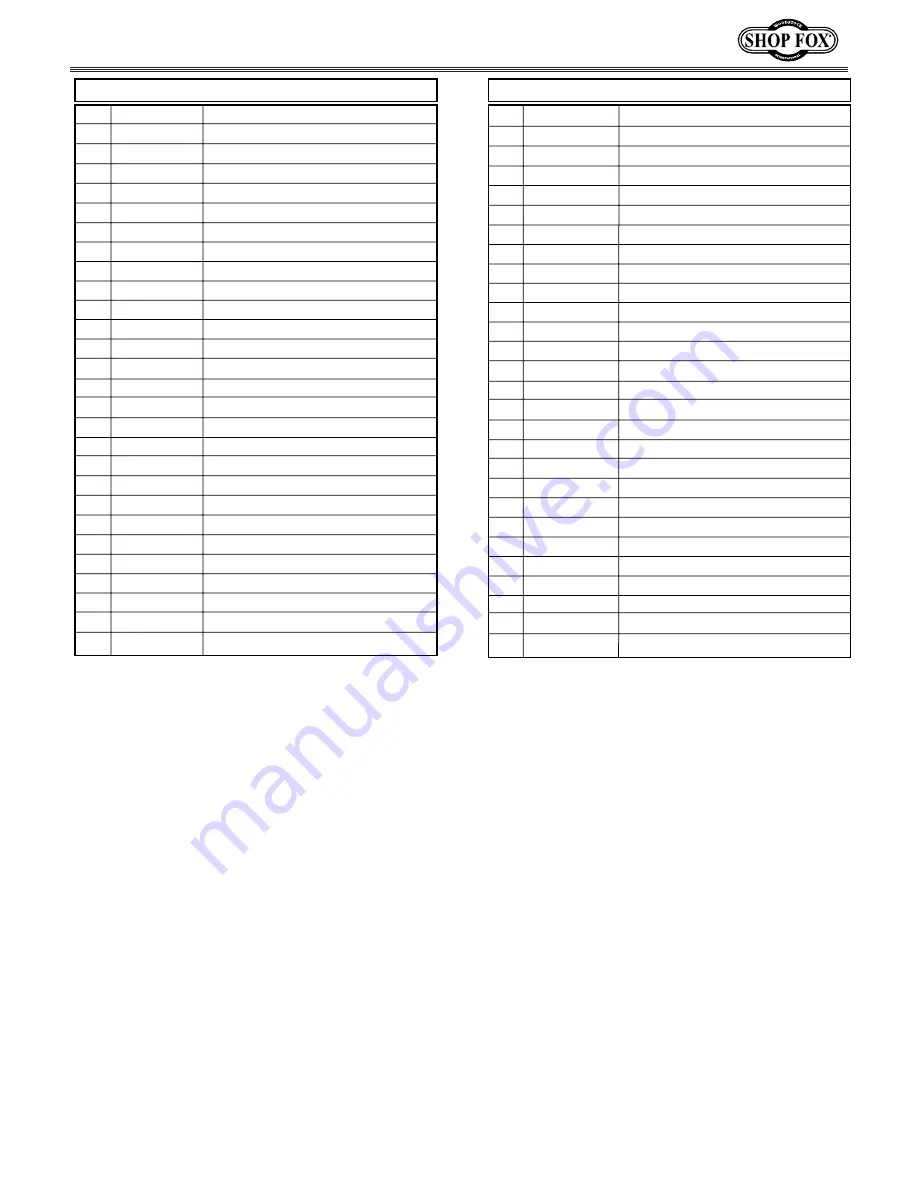
41
101 XPB03
HEX BOLT
5
⁄
16
"-18 X1"
102 XPW07
FLAT WASHER
5
⁄
16
"
103 X167103
SPRING
104 X16732104
BRACKET
105 X1673105
BAR SETTING PLATE
107 X1673107
SPECIAL WASHER
108 X1673108
BODY
109 X1673109
SPECIAL NUT
110 X167310
SPRING
111 X1673111
QUICK-HANDLE LEVER
112 XPRP49M
ROLL PIN 5 X 25
113 X1673113
TENSION BOLT
114 X1673114
GUIDE ROD
115 XPR39M
EXT RETAINING RING 8MM
116 X1673116
UPPER WHEEL BASE
117 X1673117
UPPER WHEEL SHAFT
118 X1673118
UPPER WHEEL
119 XPR21M
INT RETAINER RING 35MM
120 XP6202
BEARING 6202ZZ
122 X1673122 RUBBER TIRE
123 X1673123
SHOPFOX PLAQUE
125 X1673125
UPPER WHEEL GUARD
126 X1673126 HINGE
127 X1673127A
SWITCH
127A
X1673127B
SWITCH PLATE
127B
X1673127C
SWITCH KEY
128 XPS01
PHLPHD SCREW 10-24 X
1
⁄
2
"
129 X1673129
TRACKING KNOB
REF
PART #
DESCRIPTION
130 XPN02
HEX NUT
5
⁄
16
"-18
131 XPN06
HEX NUT
1
⁄
2
"-12
132 XPLW07
LOCK WASHER
1
⁄
2
"
133 XPLW02
LOCK WASHER
1
⁄
4
"
134 XPSB17
CAP SCREW
1
⁄
4
"-20 X
3
⁄
8
"
135 XP6204
BEARING 6204ZZ
136 XPK12M
KEY 5 X 5 X 30MM
137 X1673137
SHAFT
138 X1673138
DRIVE WHEEL
139 X1673139
LEFT HANDED NUT
3
⁄
4
"-16
140 X1673140
LOWER WHEEL GUARD
141 XPB35
HEX BOLT
3
⁄
8
"-16 X 2
1
⁄
2
"
142 XPN08
HEX NUT
3
⁄
8
"-16
143 XPB09
HEX BOLT
5
⁄
16
"-18" X
1
⁄
2
"
144 XPLW01
LOCK WASHER
5
⁄
16
"
145 X1673145
PIN 6 X 16
146 X1673146
GUARD LOCKING KNOB
147 X1673147
SPECIAL SCREW
148 X1673148
STRAIN RELIEF
149 X1673149
KNOB
150
XPWRCRD110V
110V LONG POWER CORD
151
XPWRCRDRECP
POWER CORD W/RECP
152
XPWRCRDPLUG
POWER CORD W/PLUG
153 XPLW03
FLAT WASHER
3
⁄
16
"
155 XPB11
HEX BOLT
5
⁄
16
"-18 X 1
1
⁄
2
"
156 X1673156
ADJUSTING SCREW
157 XPN04
HEX NUT
5
⁄
8
"-11
158 X1673158
BEARING HOUSING
REF
PART #
DESCRIPTION