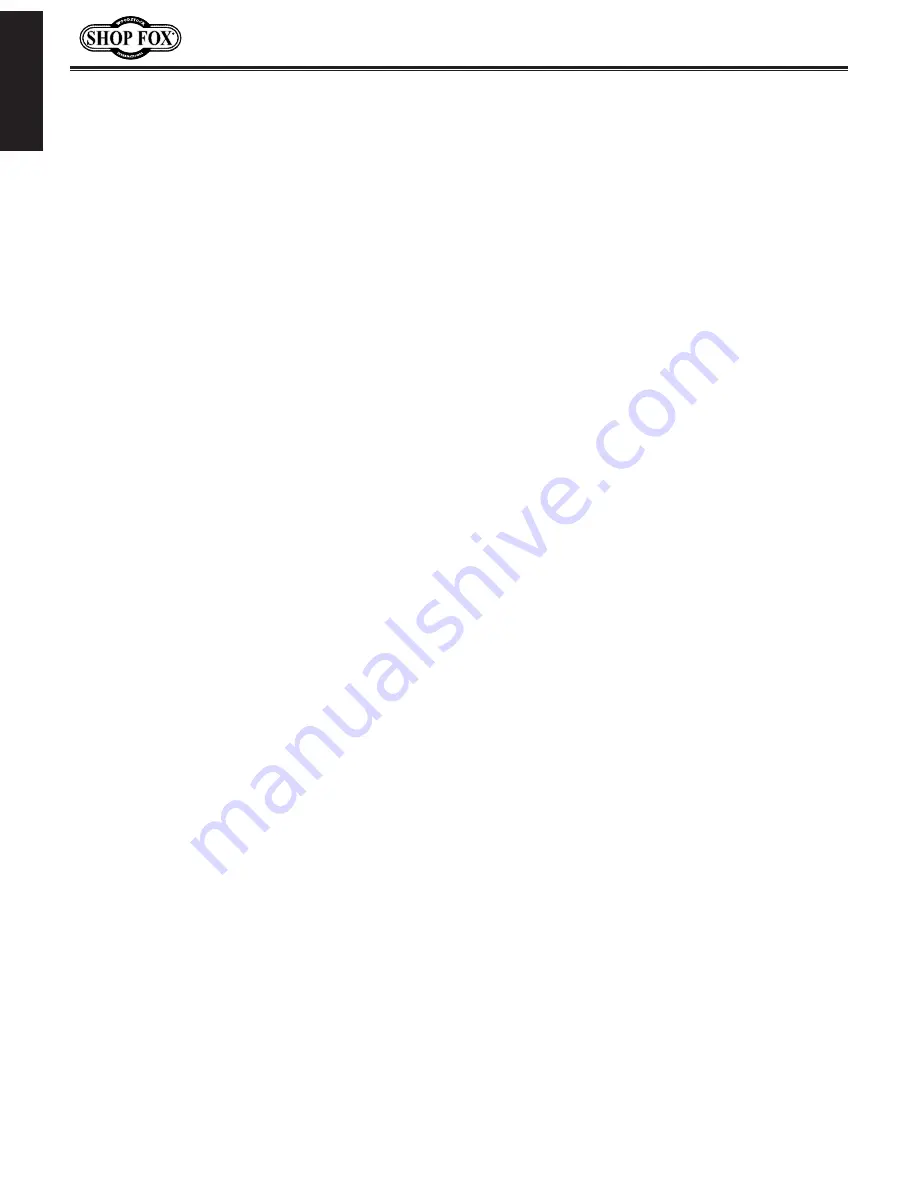
-4-
Model W1687 (For Machines Mfg. Since 9/11)
IN
TR
O
DU
CT
IO
N
Model W1687 Machine Specifications, Page 2 of 2
Main Specifications
Operation
Dust Collector Type.............................................................................. Single-Stage
Approved Dust Types.................................................................................... Wood
Filter Type................................................................................................... Bag
Airflow Capacity..................................................................................... 2830 CFM
Max Static Pressure (at 0 CFM)...................................................................... 14.4 in.
Main Inlet Size............................................................................................. 8 in.
Inlet Adapter Included..................................................................................... Yes
Number of Adapter Inlets.................................................................................... 4
Adapter Inlet Size......................................................................................... 4 in.
Machine Collection Capacity At One Time................................................................. 4
Maximum Material Collection Capacity........................................................ 10.8 cu. ft.
Filtration Rating..................................................................................... 30 Micron
Bag Information
No of Upper Bags.............................................................................................. 2
No of Lower Bags.............................................................................................. 2
Upper Bag Diameter..................................................................................... 19 in.
Upper Bag Length........................................................................................ 33 in.
Lower Bag Diameter..................................................................................... 19 in.
Lower Bag Length........................................................................................ 33 in.
Impeller Information
Impeller Type........................................................................................ Radial Fin
Impeller Size.............................................................................................. 13 in.
Impeller Blade Thickness.............................................................................. 1/8 in.
Construction
Upper Bag................................................................................................. Fabric
Lower Bag................................................................................................. Fabric
Base............................................................................. Steel Sheet Metal w/Casters
Caster..................................................................................... High Density Plastic
Impeller.................................................................................................... Steel
Paint............................................................................................ Powder Coated
Blower Housing............................................................................. Steel Sheet Metal
Body......................................................................................... Steel Sheet Metal
Other
Country Of Origin ............................................................................................. Taiwan
Warranty ....................................................................................................... 2 Years
Approximate Assembly & Setup Time ...................................................................... 1 Hour
Serial Number Location .............................................. ID Label Above Magnetic On/Off Switch
ISO 9001 Factory .................................................................................................. Yes
CSA Certified ...................................................................................................... Yes
Features
Fully Mobile
Powder Coated Paint
Includes Steel Base with Casters