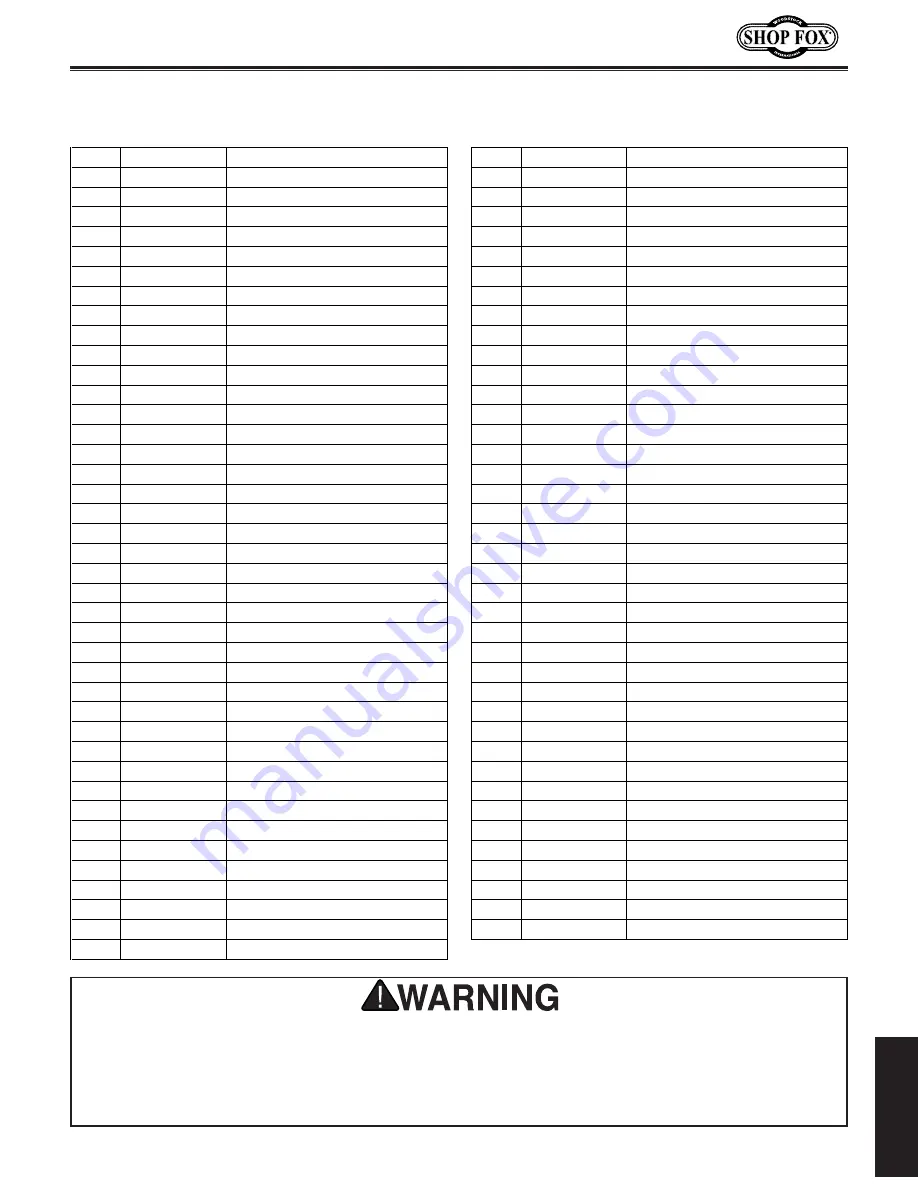
-19-
M1044 52" Foot Shear
PA
RT
S
Parts List
REF
PART
�
#
DESCRIPTION
REF
PART
�
#
DESCRIPTION
1
XM104401
BACK
�
GAUGE
�
ASSY
46
XM1044046
STRAIGHTENER
�
ROD
4
XM104404
FOOT
�
PEDAL
47
XPN02M
HEX
�
NUT
�
M10-1.5
5
XPSS10M
SET
�
SCREW
�
M10-1.5
�
X
�
20
48
XPSB72M
CAP
�
SCREW
�
M10-1.5
�
X
�
30
6
XM104406
BEVEL
�
GAUGE
49
XM1044049
GIB
7
XM104407
WING
�
NUT
50
XPSS15M
SET
�
SCREW
�
M12-1.75
�
X
�
12
8
XPW02
FLAT
�
WASHER
�
3/8"
51
XPW04M
FLAT
�
WASHER
�
10MM
9
XM104409
T-NUT
�
STUD
52
XPW04M
FLAT
�
WASHER
�
10MM
10
XM1044010
FRONT
�
STOP
53
XPSB90M
CAP
�
SCREW
�
M10-1.5
�
X
�
55
11
XPN02M
HEX
�
NUT
�
M10-1.5
54
XPB31M
HEX
�
BOLT
�
M10-1.5
�
x
�
40
12
XPB32M
HEX
�
BOLT
�
M10-1.5
�
X
�
25
55
XM1044055
FIXED
�
KNIFE
�
(LOWER)
13
XM1044013
EXT
�
BAR
�
SCREW
56
XM1044056
MOVING
�
KNIFE
�
(UPPER)
14
XM1044014
ROD
�
BRACKET
57
XPN05M
HEX
�
NUT
�
M16-1.5
15
XM1044015
STUD
58
XPW08M
FLAT
�
WASHER
�
16MM
16
XM1044016
LOCK
�
KNOB
59
XPB113M
HEX
�
BOLT
�
M16-2
�
X
�
120
17
XPN02M
HEX
�
NUT
�
M10-1.5
61
XPSB47M
CAP
�
SCREW
�
M10-1.5
�
X
�
40
18
XM1044018
ADJUSTABLE
�
SCREW
62
XPSS39M
SET
�
SCREW
�
M10-1.5
�
X
�
50
19
XM1044019
ADJUSTABLE
�
DIAL
63
XM1044063
TABLE
�
SCALE
�
WASHER
20
XM1044020
ADJUSTABLE
�
BLOCK
64
XM1044064
TABLE
�
SCALE
�
SCREW
21
XM1044021
RIGHT
�
BACK
�
GAUGE
�
EXT
�
BAR
65
XM1044065
RIGHT
�
TABLE
�
SCALE
22
XM1044022
LEFT
�
BACK
�
GAUGE
�
EXT
�
BAR
66
XM1044066
LEFT
�
TABLE
�
SCALE
23
XM1044023
BACK
�
GAUGE
�
STOP
67
XPSB58M
CAP
�
SCREW
�
M8-1.25
�
X
�
12
24
XM1044024
BACK
�
GAUGE
�
ROD
68
XM1044068
FINGER
�
GUARD
26
XM1044026
HINGE
�
PIN
69
XPW06M
FLAT
�
WASHER
�
12MM
28
XM1044028
BOTTOM
�
SWIVEL
�
SCREW
70
XPB125M
HEX
�
BOLT
�
M12-1.75
�
X
�
65
29
XM1044029
TOP
�
SWIVEL
�
SCREW
71
XPN09M
HEX
�
NUT
�
M12-1.75
30
XPW04M
FLAT
�
WASHER
�
10MM
72
XM1044072
PRESSURE
�
PLATE
�
SPRING
�
STUD
31
XPSB64M
CAP
�
SCREW
�
M10-1.5
�
X
�
25
73
XM1044073
PRESSURE
�
PLATE
�
SPRING
32
XM1044032
SPRING
�
MOUNTING
�
BRACKET
74
XPB24M
HEX
�
BOLT
�
M12-1.75
�
X
�
45
33
XPN05M
HEX
�
NUT
�
M16-1.5
75
XM1044075
FRONT
�
ARM
�
EXT
34
XPLW10M
LOCK
�
WASHER
�
16MM
76
XM1044076
LEFT
�
SIDE
�
PANEL
35
XM1044035
STUD
77
XM1044077
RIGHT
�
SIDE
�
PANEL
36
XM1044036
SWIVEL
�
BOTTOM
78
XM1044078
PRESSURE
�
PLATE
37
XM1044037
SWIVEL
�
TOP
79
XM1044079
CUTTER
�
BAR
38
XM1044038
CAP
�
SPRING
80
XM1044080
TABLE
39
XM1044039
FOOT
�
PEDAL
�
SPRING
81
XM1044081
MACHINE
�
ID
�
LABEL
40
XPSS10M
SET
�
SCREW
�
M10-1.5
�
X
�
20
82
XM1044082
SAFETY
�
GLASSES
�
LABEL
41
XPW08M
FLAT
�
WASHER
�
16MM
83
XM1044083
READ
�
MANUAL
�
LABEL
42
XPN05M
HEX
�
NUT
�
M16-1.5
84
XM1044084
SHEARED
�
FINGERS
�
LABEL
43
XM1044043
BOW
�
BOLT
85
XM1044085
GUARD
�
LABEL
44
XPN05M
HEX
�
NUT
�
M16-1.5
86
XM1044086
MODEL
�
NUMBER
�
LABEL
45
XPW08M
FLAT
�
WASHER
�
16MM
Safety labels warn about machine hazards and how to prevent machine damage or injury. The
owner of this machine MUST maintain the original location and readability of all labels on this
machine. If any label is removed or becomes unreadable, REPLACE that label before allowing the
machine to enter service again. Contact Woodstock International, Inc. at
(
360
)
734-3482 or www.
shopfoxtools.com to order new labels.
Summary of Contents for SHOP FOX M1044
Page 2: ... ...