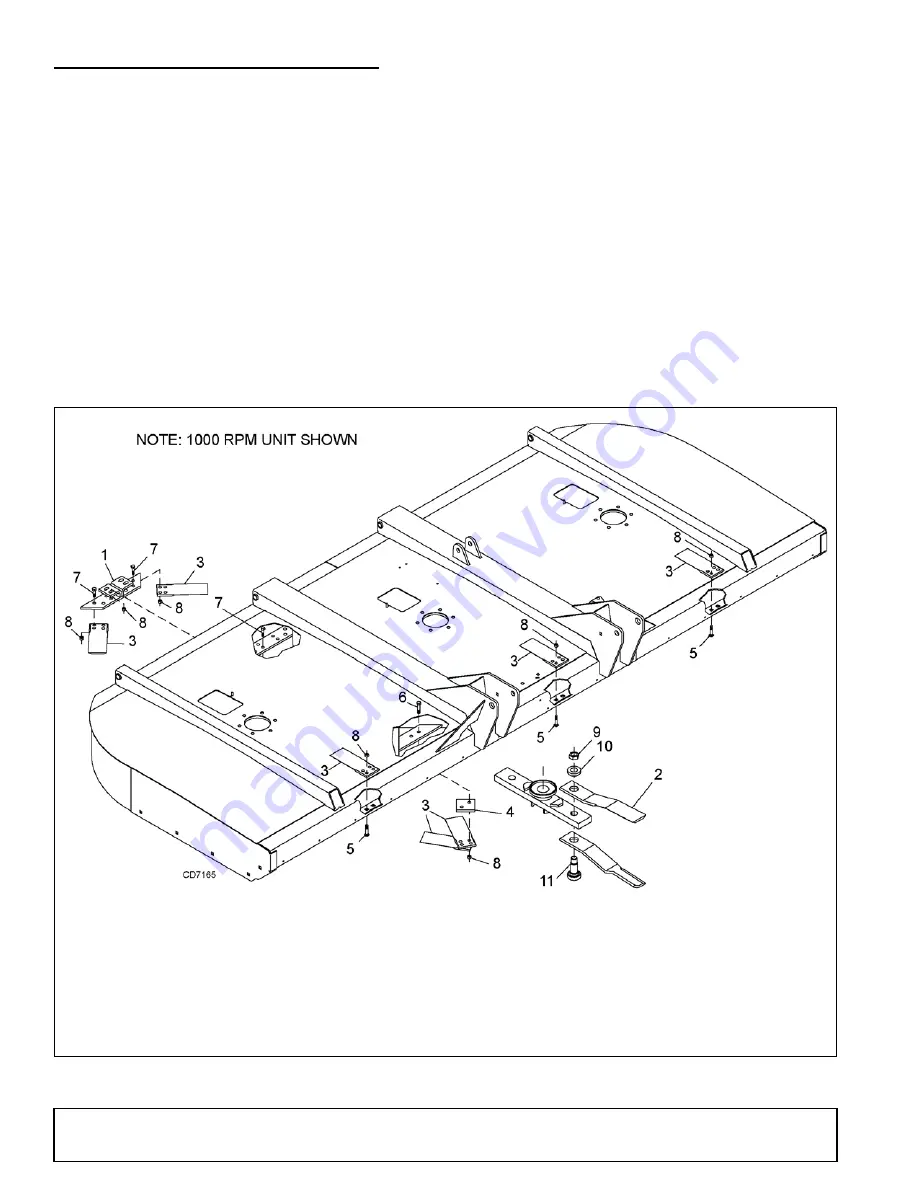
46
Assembly
MAN0577 (6/29/2007)
INSTALL SHREDDER KIT (OPTIONAL)
1.
Remove nut (9) and spacer (10) from blade pin
(11). While keeping the lower formed blade
installed, install double-edge blade (2) with offset
upwards towards deck.
2.
Reinstall spacer (10). Install new nut (9) and torque
to 664 lbs-ft. Make sure blades are free to pivot.
3.
Install blade holder (1) to link between rear V-baffle
of machine using four cap screws (7) and four lock
nuts (8).
NOTE:
Blade holder installs on right side of cutter
for 1000 rpm cutters (shown) and on the left side
for 540 rpm cutters. See Figure 35.
4.
Attach two stationary blades (3) to blade holder
using cap screws (7) and lock nuts (8).
5.
Attach plate (4) and two stationary blades (3) to link
between front V-baffle of machine using cap
screws (6) and lock nuts (8).
NOTE:
Blades located on right side of cutter for
1000 rpm cutters (shown) and on the left side for
540 rpm cutters.
6.
Attach three stationary blades (3) to front frame of
cutter using carriage bolts (5) and lock nuts (8).
NOTE:
Center blade is located left of cutter center
for 1000 rpm cutters (shown) and right of center for
540 rpm cutters.
Figure 34
. Shredder Kit Installation
1. Blade holder
2. Double edge blade, .5 x 4 x 22.5
3. Double edge blade, .38 x 1 x 11.13
4. Plate
5. 5/8 NC x 1-1/2 Carriage bolt
6. 5/8 NC x 3 HHCS GR5
7. 5/8 NC x 1-3/4 HHCS GR5
8. 5/8 NC Lock nut
9. 1-1/4 Locking jam nut
10. Flange bushing
11. Blade pin
Summary of Contents for TS1680
Page 1: ...OPERATOR S MANUAL ROTARY CUTTER MAN0577 Rev 9 30 2015 TS1680 TS1680Q...
Page 28: ...28 Troubleshooting MAN0577 6 29 2007 NOTES...
Page 41: ...Assembly 41 MAN0577 6 26 2007 Figure 29 TS1680 Pull Type Cutter Assembly Front Half...
Page 52: ...52 Parts MAN0577 6 29 2007 PULL TYPE ASSEMBLY FRONT HALF...
Page 56: ...56 Parts MAN0577 6 29 2007 MOUNTED CUTTER ASSEMBLY Rev 1 25 2008...
Page 58: ...58 Parts MAN0577 6 29 2007 CENTER GEARBOX ASSEMBLY...
Page 60: ...60 Parts MAN0577 6 29 2007 SIDE GEARBOX ASSEMBLY...
Page 70: ...70 Parts MAN0577 6 29 2007 CASTER ARM ASSEMBLY MOUNTED...