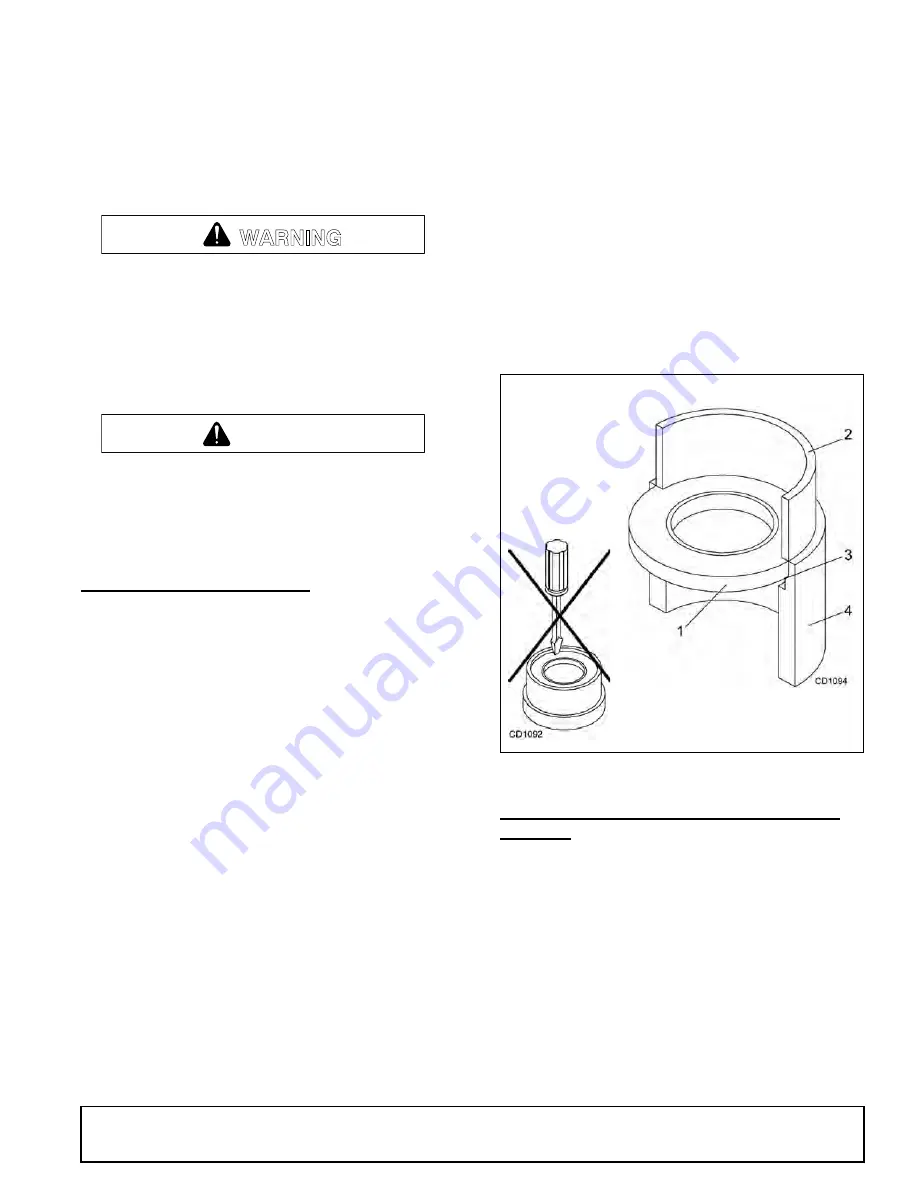
Dealer Service
23
MAN1289 (10/18/2019)
DEALER SERVICE
The information in this section is written for dealer ser-
vice personnel. The repair described here requires
special skills and tools. If your shop is not properly
equipped or your mechanics are not properly trained in
this type of repair, do not attempt this repair.
Before working underneath, disconnect drive-
line, raise cutter, lock in transport position, and
block cutter securely. Hydraulic system leak down
and failure of mechanical or hydraulic system can
cause equipment to drop.
Keep all persons away from operator control
area while performing adjustments, service, or
maintenance.
Always wear relatively tight and belted clothing
to avoid getting caught in moving parts. Wear
sturdy, rough-soled work shoes and protective
equipment for eyes, hair, hands, hearing, and head;
and respirator or filter mask where appropriate.
GEARBOX MAINTENANCE
NOTE:
Read this entire section before starting any
repair. Many steps are dependent on each other.
1.
Fill gearbox with SAE 80W or 90W gear lube until it
runs out the side level plug.
NOTE:
Repair to this gearbox is limited to replac-
ing bearings, seals, and gaskets. Replacing gears,
shafts, and a housing is not cost effective. Pur-
chasing a complete gearbox is more economical.
2.
Inspect gearbox for leakage and bad bearings.
Leakage is a very serious problem and must be
corrected immediately. Bearing failure is indicated
by excessive noise and side-to-side or end-play in
gear shafts.
Seal Replacement
Recommended sealant for gearbox repair is Perma-
tex
®
Aviation 3D Form-A-Gasket or equivalent.
Leakage can occur at the vertical or horizontal gaskets
and shaft seals.
Leakage at the horizontal gasket or seal can be
repaired without removing the gearbox from the cutter.
Seal Installation
NOTE:
Proper seal installation is important. An improp-
erly installed seal will leak.
1.
Clean area in housing where seal outer diameter
(OD) seats. Apply a thin coat of Permatex.
2.
Inspect area of shaft where seal seats. Remove
any burrs or nicks with an emery cloth.
3.
Lubricate gear shaft and seal lips.
4.
Place seal squarely on housing, spring-loaded lip
toward housing. Select a piece of pipe or tubing
with an OD that will sit on the outside edge of the
seal but will clear the housing. Tubing with an OD
that is too small will bow seal cage and ruin seal.
5.
Carefully press seal into housing, avoiding
distortion to the metal seal cage.
Figure 16
. Seal Installation
GEARBOX REPAIR - BB48.30, BB60.30,
BB72.30
(Figure 17)
NOTE:
Repair to this gearbox is limited to replacing
bearings, seals, and gaskets. Replacing gears, shafts,
and a housing is not cost effective. Purchasing a com-
plete gearbox is more economical.
Gearbox is heavy: do not attempt to move without
mechanical assistance.)
Remove Gearbox from Cutter
1.
Disconnect and remove the driveline from the
gearbox.
2.
Remove vent plug (9) and siphon gear lube from
housing through this opening.
WARNING
CAUTION
1. Seal
2. Pipe or tube
3. Seal seat
4. Casting
Pipe or tube must
press at outer
edge of seal.
Incorrect
Installation