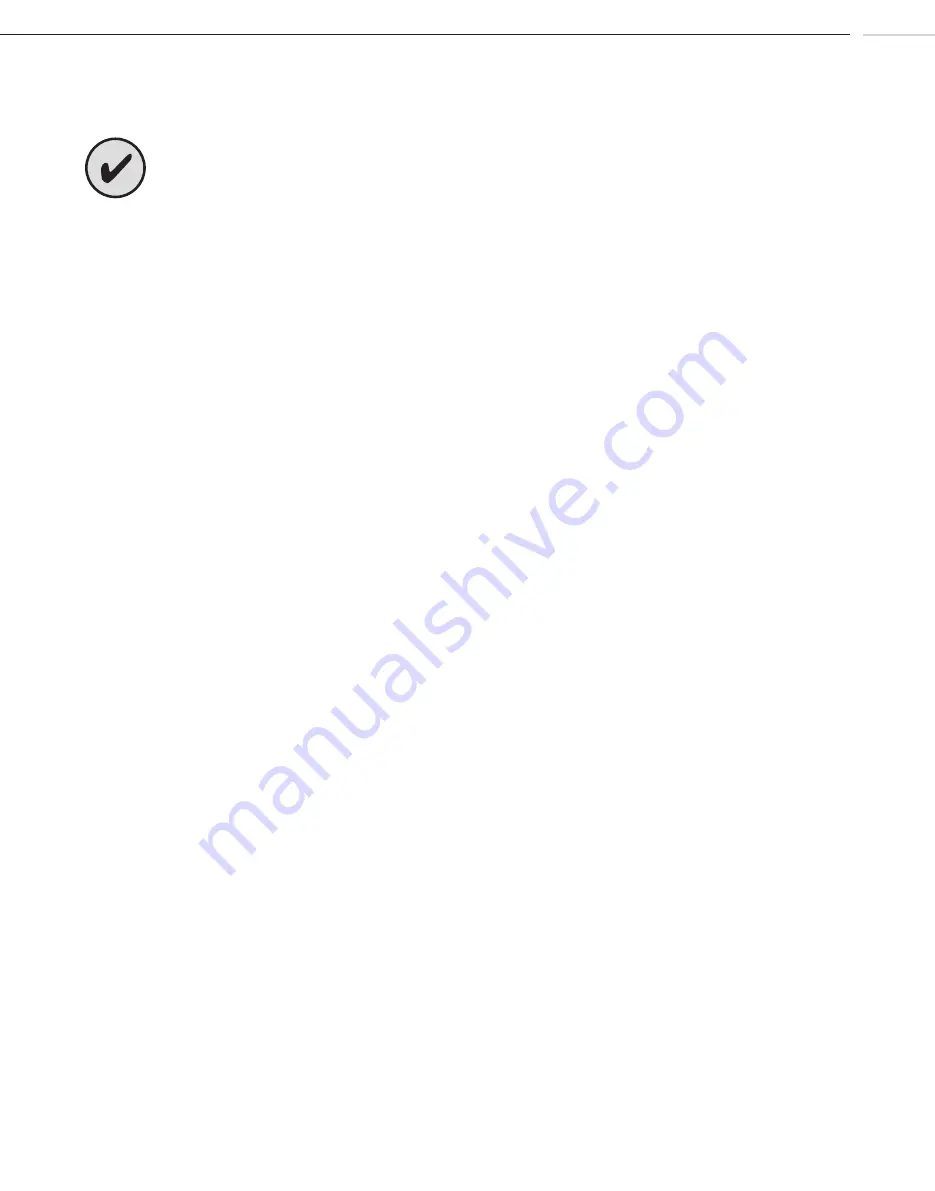
19. FAULT FINDING
Please refer to the safety warnings (“attention” items) stated within paragraph 17.
NOTE
!
Routine maintenance procedures detailed in Paragraph 17, and Table 1 (page 16), of this document are
designed to help keep your fan operational and fault free.
19.1 ELECTRICAL
Check that electrical connections to the fan are secure and are in accordance with the associated wiring connection diagram.
Check that the voltage applied at each fan terminal is as specified on the fan nameplate and is balanced. Measure the current
on each phase (one phase in the case of single-phase motors) of the motor in turn and check that the current consumption is
within the full load current specified on the motor or fan nameplate.
Measure each motor winding to earth, and between each winding, using a 500V dc insulation tester. If the reading is less
than 10 MΩ (Megaohm) the reason is likely to be dampness within the motor. To dry out the motor place it in a warm dry
airstream (typically at +104°F) and regularly monitor the motor until the insulation reading is restored to 10 MΩ (Megaohm)
or greater. If the reading remains at less than ten, then this could indicate that a break-down in motor winding insulation has
occurred, which may require the motor to be either rewound/overhauled (standard temperature machines) or replaced with a
new motor which been manufactured in accordance with current requirements as stated within the EN12101-3 specification.
(smoke extraction machines).
If a smell of burnt motor insulation is detected, then please seek immediate advice from Woods Air Movement USA.
19.2 MECHANICAL
Check that there are no obstructions to the motor shaft or impeller blades, that the blades are clean, and that there are no
loose components, items or debris in the vicinity.
Rotate the motor shaft by hand. Investigate any grinding noises, internal chaffing, rubbing or stiffness. If any of these defects
are observed, this may indicate that bearings require lubrication or replacement.
Ensure that all fasteners are secure and tightened to the correct torque values.
20. DISPOSAL
Metal components of the fan/motor should be segregated and separately recycled. The following items of material should be
safely disposed of in accordance with local health and safety regulations:
- electrical lead coverings,
- motor winding insulation materials,
- bearing lubricant,
- motor/fan terminal block,
- paintwork,
- plastic parts,
- packing materials,
- silencer infill (Note that a face mask and gloves must be worn when handling the infill. If the infill is particularly dry or is
damaged it should be damped down before disposal),
15
Summary of Contents for 911025
Page 19: ...19 NOTES...