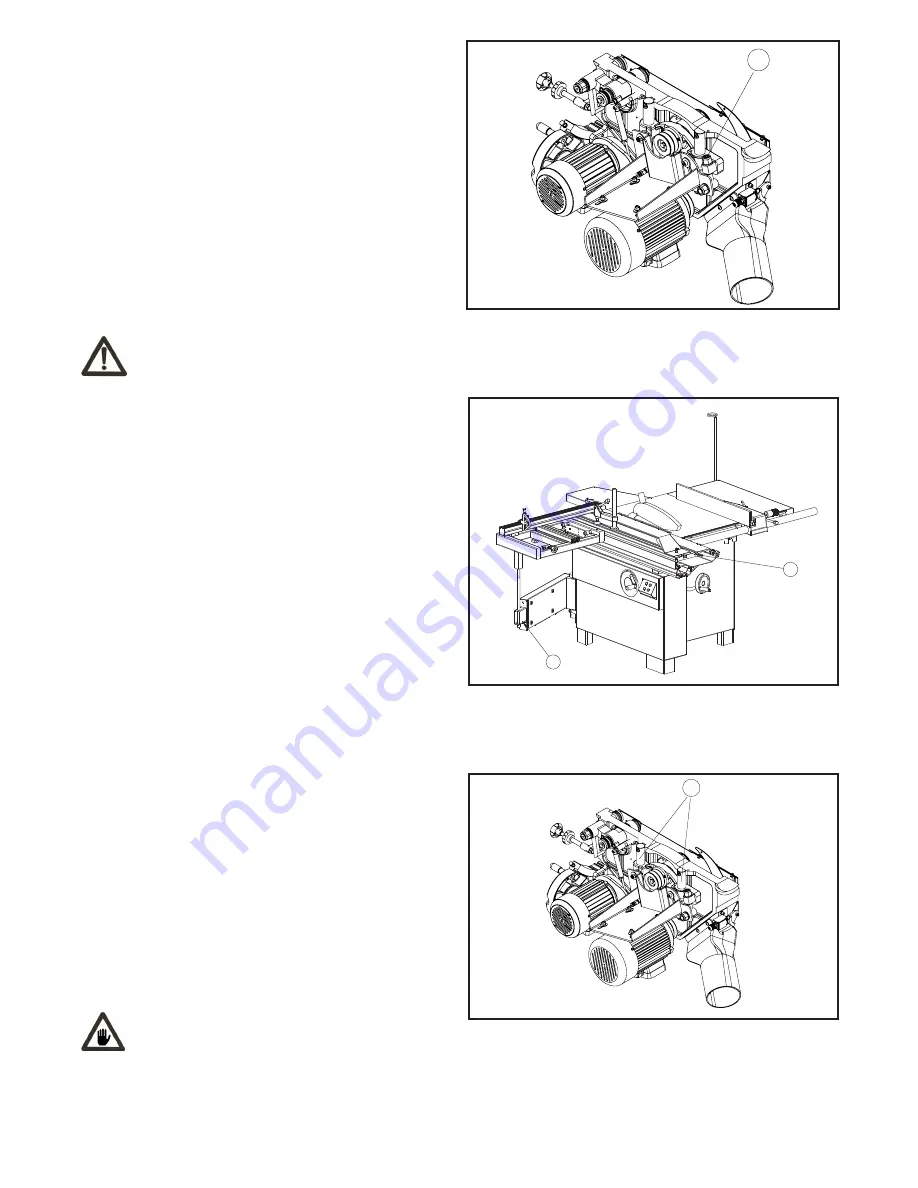
7.5 REPLACEMENT AND DISPOSAL
Should replacement become necessary, the machine
parts must be replaced with original components in order
to guarantee their efficiency.
The replaced parts must be disposed of in compliance
with the laws in force in the country of use.
Component replacement requires specific training and
technical skills; for this reason, the above interventions
must be carried out by qualified personnel to prevent
damage to the machine and risks to the safety of persons.
-18-
Fig.7.3
7.4 GENERAL LUBRICATION
- Weekly clean and lubricate all the mobile couplings of
the machine A with a thin film of oil and grease.
- Protect all belts and pulleys to avoid contamination with
oil.
Fig.7.4
7.3 OVERALL CLEANING
Please DO NOT to try removing chips while the saw
blade is running.
WARNING
After each working cycle, thoroughly clean the machine
and all of its parts, vacuum the shavings and dust and
remove any resin residues.
Use compressed air only when strictly necessary, using
protective glasses and a mask.
In particular, clean the following parts:
- the sliding table rail A;
- the sliding support extension B;
CAUTION
- In case of mechanical or functional faults in the machine, including guards or tools, please call the local authorized
agent for technical assistance and maintenance.
- Any maintenance must be only done when the machine is isolated from all energy sources (plug out).
A
A
B
Fig.7.2
A
7.2
REPLACE
BELT
Tools Required for Assembly:
- 4mm allen wrench
- 6mm allen wrench
-Open right side plate with 4mm allen wrench, then rotate
the screw rod at A of figure 7.2 with 6mm allen wrench.
-When rotating the wrench clockwise, belt becomes loose;
when rotating the wrench anticlockwise, belt becomes
tight.