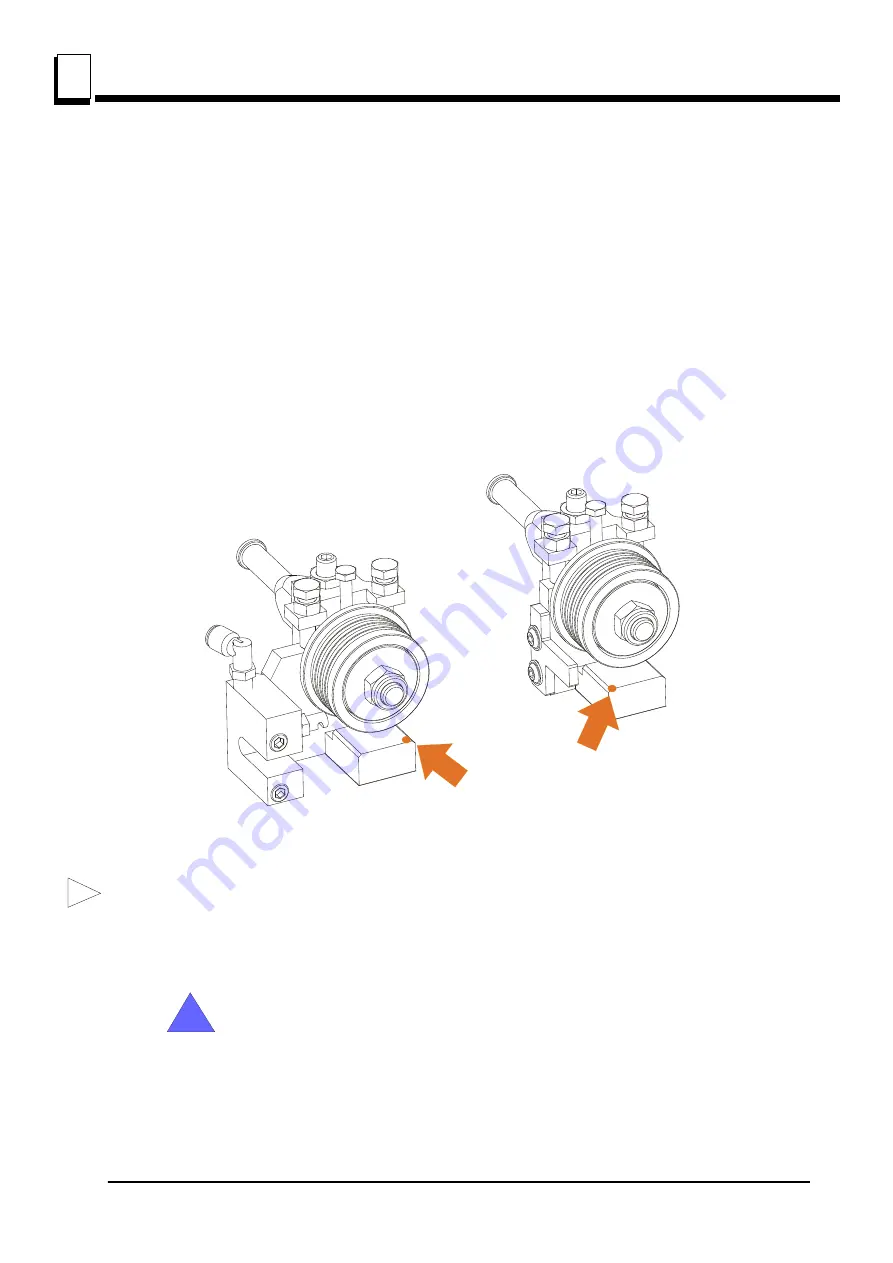
Maintenance
Blade Guides
3
3-2
HDdoc012020
Maintenance
3.2
Blade Guides
1.
Check the rollers for performance and wear every blade change. Make sure the rollers are clean and spinning
freely. If not, rebuild them. Replace any rollers which have worn smooth or have become cone shaped. See
The LT40 Series DH Parts manual for blade guide rebuild kits and complete roller assemblies.
Steel Blade Guide Blocks
2.
Inspect the blocks at every blade change for damage or wear. If the block is bent or damaged, replace the
block assembly.
As the blocks wear, the front inside corner will wear more than the body of the block. When the corner wears
far enough, sawing performance will be affected even if the body of the block is adjusted properly to the blade.
At this point, the block should be replaced. If you have access to the appropriate equipment, you can grind or
mill the blocks to a new flat surface and reuse them. It is recommended you develop a routine schedule for
replacing the blade guide blocks based on your sawing conditions and experience.
3.
Check the inserts are properly spaced from the bottom of the blade every 25 hours of operation. As the rollers
wear, the gap between the blade and inserts will become larger. Use the provided shim or a feeler gauge to
check the inserts are adjusted 0,3 - 0,5 mm from the blade.
To adjust the disks up, loosen the bottom guide disk mounting bolt and clamp bolt. Use the provided adjust-
ment tool to raise bottom disk. Retighten the bottom disk mounting bolt and clamp bolt.
IMPORTANT!
The inserts should be parallel to the blade. Check the space
between the insert and the blade at each side of the insert to insure it is paral-
lel. Use the appropriate outer adjustment bolt to tilt the insert mounting plate
so the insert is parallel to the blade.
After adjusting the drive side blade guide block insert up, check the deflector. If necessary, loosen the two
deflector mounting screws and adjust the deflector so it does not touch the blade.
See Figure 3-1.
FIG. 3-1
25
!