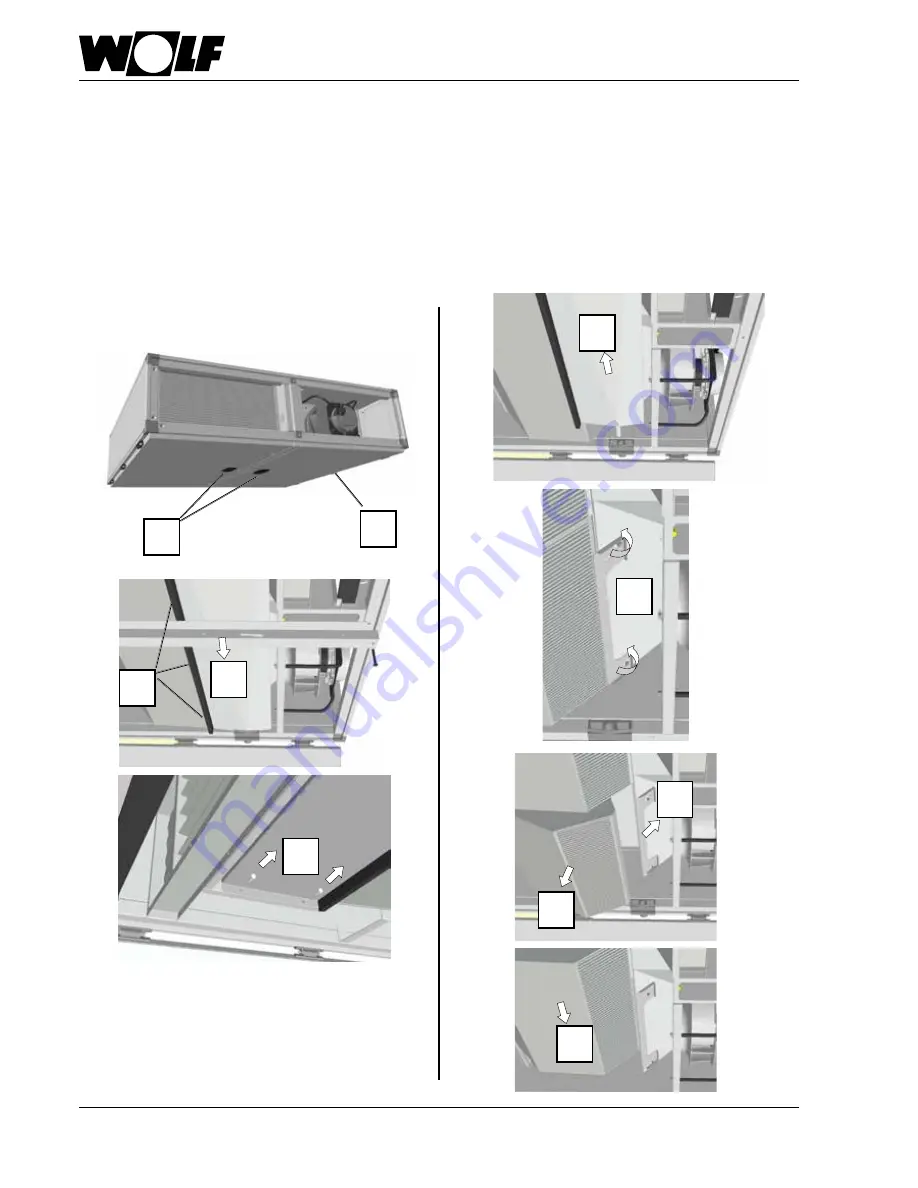
26
3065065_201704
2.
1.
3.
4.
12. Maintenance instructions
5.
6.
7.
8.
1. Disconnect trap drain connection
2. Open inspection doors
3. Undo unit partition screws and remove partition
4. Remove seals (sealant) from condensate pan and condensate drain
5. Undo condensate pan threaded connection
6. Remove condensate pan by lowering slightly (side where screws have been removed) and pulling
7. Slightly loosen tensioning bracket screws
8. Push tensioning bracket upwards
9. Remove first part of countercurrent plate heat exchanger
10. Push further parts along the guide and remove them as well
11. Reassemble in reverse order (re-establish seal with sealant)
1.
2.
3.
5.
6.
7.
8.
4.
CFL 10 / 15 / 22
10.
9.