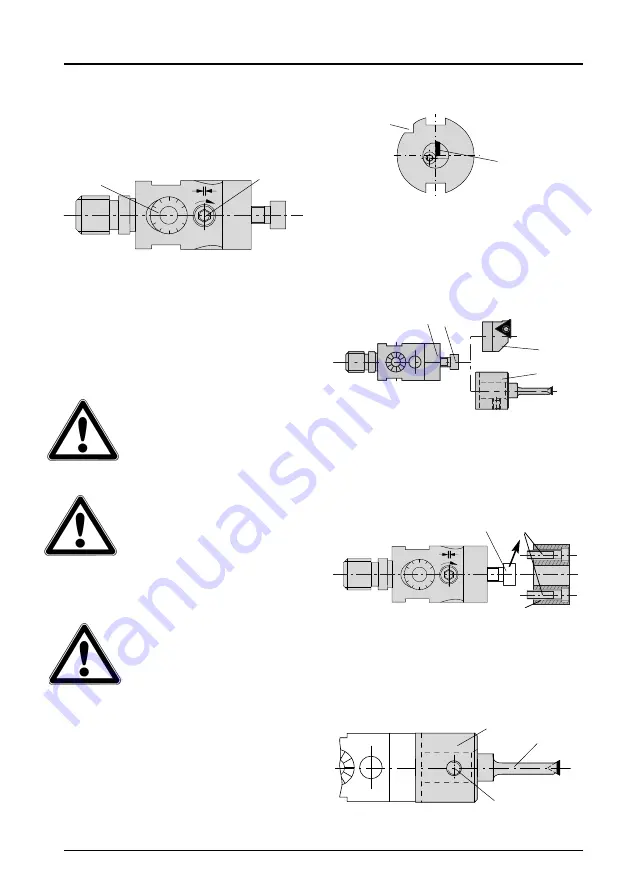
11
English
Example: Steep angle taper to
DIN 69871
c) Securing the adaptor,
tool holder and insert holder
Adjusting plate
8
is serrated to enable
different tool holders
2
and connectors
3
to be mounted quickly and easily
(figure 4).
– Adaptors 248063 / 248064 /
248065 / 248071 “Mini“
Remove cap screw
9
. Secure adaptor
3
for the tool holder centrally on the adjus -
ting plate (figure 5). Secure the adaptor
using cap screw
0
. Apply
1,5 Nm
(13.23 in. lbs.) torque.
– Tool holder
Insert tool holder
4
into adaptor
3
and
secure using thread pin
ß
. Apply torque
of
2,5 Nm
(22.125 in. lbs.) (figure 6).
4. Operation
a) Clamping
To clamp the adjusting pin, all tools are
fitted with a clamping screw
6
(figure 2).
When removing metal, this clamping
screw
6
must be used to clamp the
adjusting pin. Before and after each
adjustment, the clamping arrangement
must be operated. Graduated dial
7
for
the spindle adjustment is located next to
the tool clamping point. Only one key is
needed to operate both functions.
To avoid damage to parts of the
adjustment mechanism, do not
make any diameter adjust-
ments in the clamped state.
b) Fixing the tool to the connector shank
Secure the tool to the shank apply ing
a torque of 20 Nm (177.015 in. lbs.)
Using a higher torque you will
damage the thread M 8.
Service keys see page 13.
To do this, we suggest you to grip the
shank in a collet chuck:
When gripping the shank in the
collet chuck, please take
account of the cutter position
relative to the chuck’s
grooves or serrations (figure 3).
10
1
5
0
5
7
6
Serration
Indexable
insert
8 9
2
3
10
1
5
0
5
0
9
3
4
3
ß
figure 2
figure 3
figure 4
figure 5
figure 6