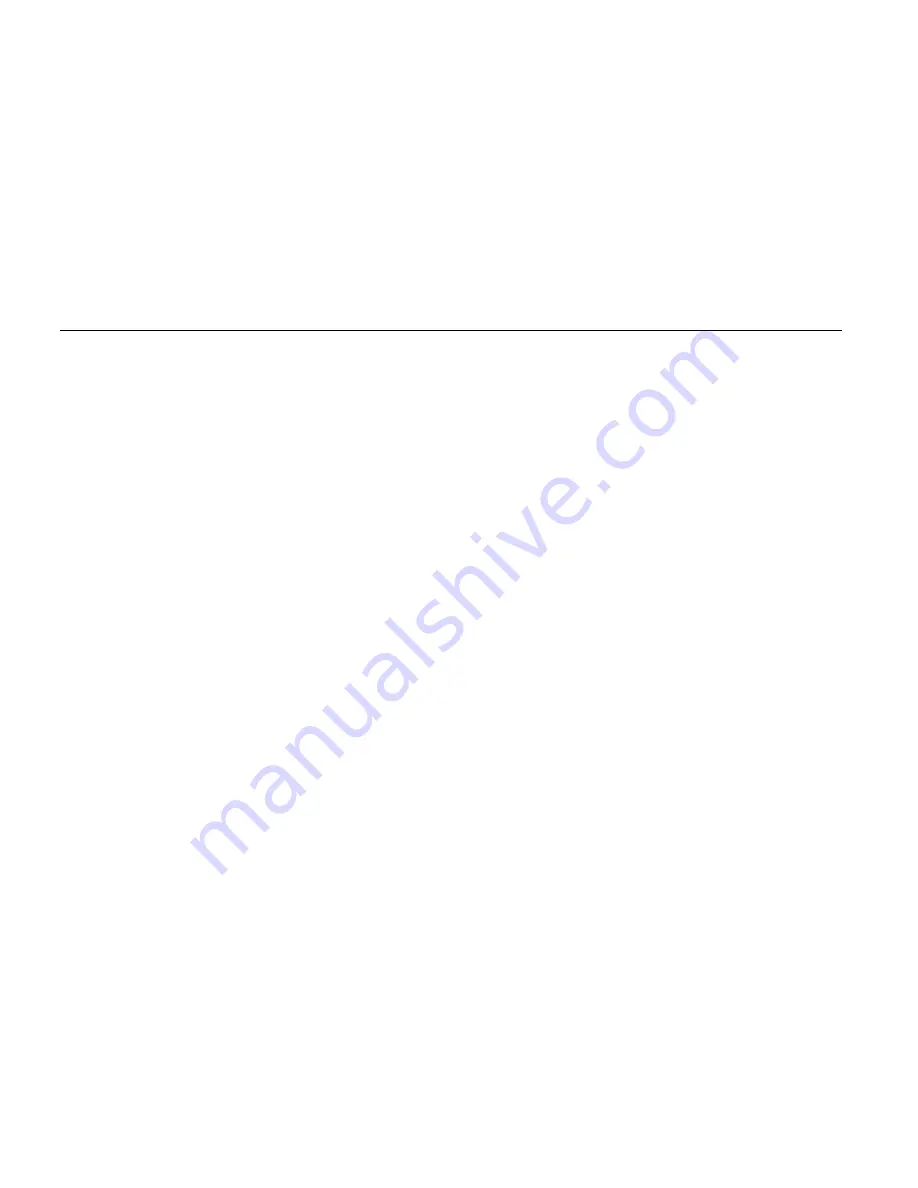
Installation and commissioning
7
1.2
Hardware connection and preparatory work
1.2.1
General tasks
Place the coffee machine horizontally on the counter (breadth and depth); adjust feet where adjustable
Connect the water infeed
Water filter needed? If yes– connect (for details, see the following chapter)
Connect the drain – use angle 33 2165 8000 from horizontal to vertical!
All drains must be sloped.
Connect to the power supply
Switch on the coffee machine
1.2.2
Recommended water filter
A WMF water filter is recommended for carbonate hardness above 5 °dKH.
For the WMF 5000S, the –bestmax XL– water filter is recommended in the standard price list.
After measuring the carbonate hardness with a test kit - which is within the sell-by date - cut to size according to the capacity table
(see the User manual which comes with the filter).
Summary of Contents for 5000S
Page 1: ...WMF 5000S Service manual KMT Technical Support Revision 03 2015 Rev 01 ...
Page 3: ...Change history 3 Change history Rev 01 1st edition for series launch ...
Page 23: ...Maintenance 23 3 2 Installation of maintenance packages required for different brewing times ...
Page 30: ...Special tools and aids 30 ...