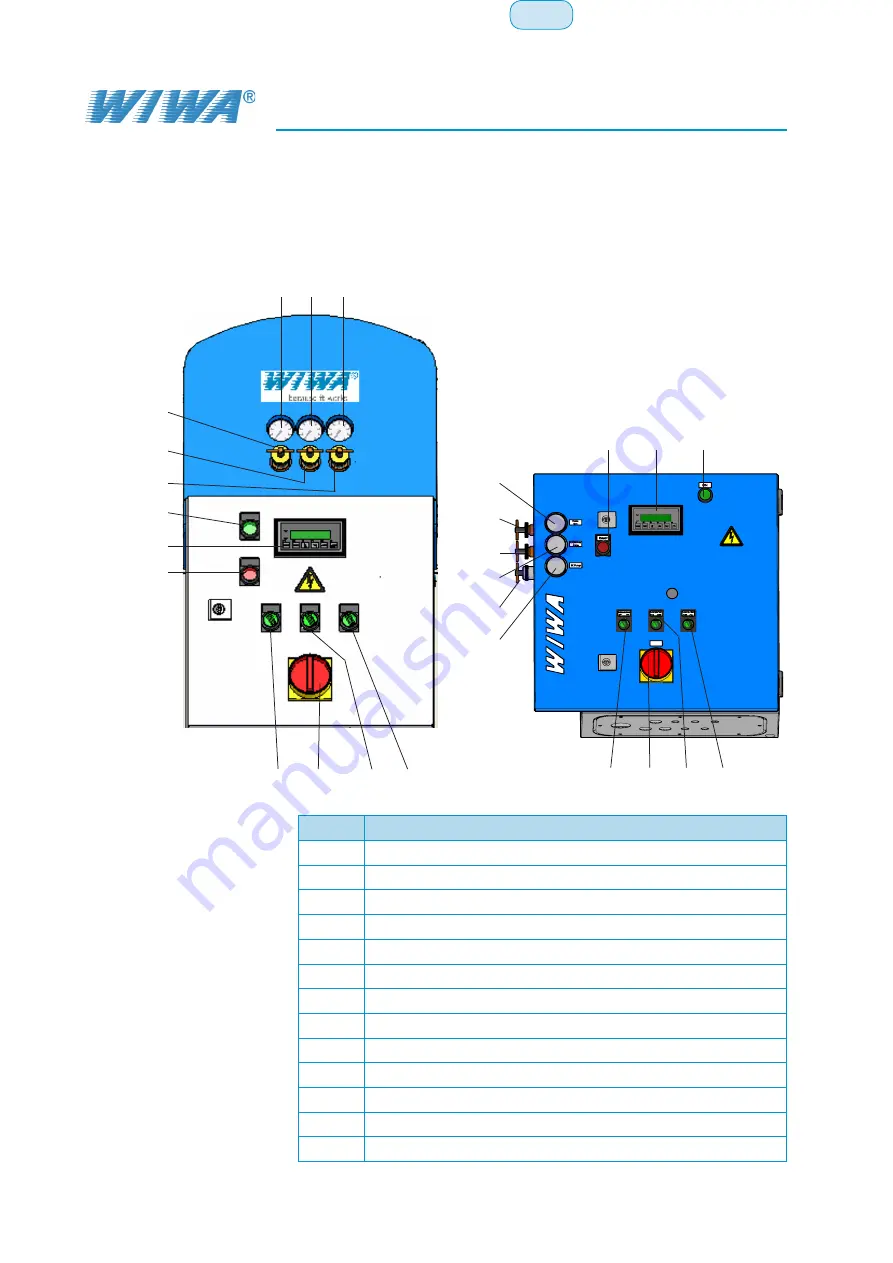
Original Operation Manual
3-7
•1307_PU280_SV1018DV1020_BAoDB_en•ski
en
Machine Description
1
2
3
4
5
6
7
8
9
10
13
11
12
Figure 3.5
400 V
10
9
8
7
4
6
5
1
11
2
3
12
13
Figure 3.6 230V
Position Description
1
Compressed air regulator spray gun
2
Compressed air regulator feed pumps
3
Compressed air regulator metering pump
4
Button “SYSTEM ON”
5
Display
6
Button reset malfunction
7
Heating hose package “ON / OFF”
8
Master switch
9
Material flow heater “ON / OFF”, component Poly
10
Material flow heater “ON / OFF”, component Iso
11
Compressed air pressure gauge spray gun
12
Compressed air pressure gauge feed pumps
13
Compressed air pressure gauge metering pump
3.11 Control
cabinet
3.11.1 Components
on the control
cabinet
Summary of Contents for DUOMIX PU280
Page 68: ......