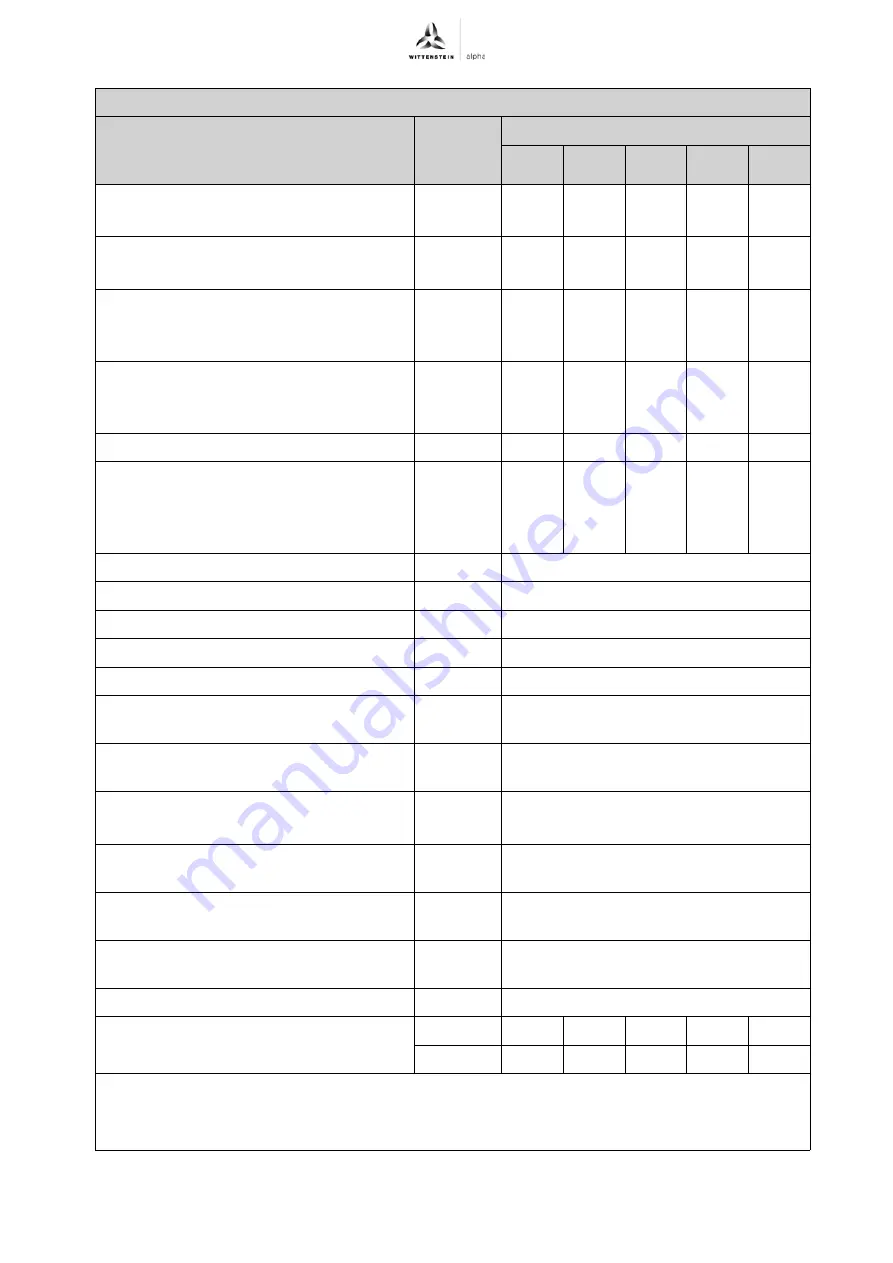
Appendix
SP
+
ATEX MC
en-42
2022-D014985
Revision: 07
Technical data for SP
+
140, 2-stage, i = 40 – 100
Clamping
hub Ø
[mm]
Ratio i
40
50
64
70
100
Max. acceleration torque T
2B
[Nm]
(max. 1000 cycles per hour)
264
264
210
264
210
Nominal output torque T
2N
[Nm]
(At n
1N
)
211
211
168
211
168
Emergency stop torque T
2Not
[Nm]
(1000 times possible during the service life
of the gearbox)
–
710
710
380
710
380
Permissible average input speed n
1N
[min
-1
]
(At T
2N
)
a
–
3600
3600
3600
3600
3600
Max. input speed n
1Max
[min
-1
]
–
4500
4500
4500
4500
4500
Average no-load running torque T
012
[Nm]
(For n
1
=3000 min
-1
and gearbox
temperature 20 °C)
b
–
0.55
0.45
0.45
0.40
0.40
Max. backlash j
t
[arcmin]
–
Standard ≤ 6 / Reduced ≤ 4
Torsional rigidity C
t21
[Nm/arcmin]
–
53
Max. axial force F
2AMax
[N]
c
–
6900
Max. lateral force F
2QMax
[N]
c
–
6600
Max. tilting moment M
2KMax
[Nm]
–
660
Service life L
h
[h]
–
see Chapter 7.2.4 "Replacing the
Weight incl. standard adapter plate m
[kg]
–
17
Operating noise L
PA
[dB(A)]
(For n
1
= 3000 min
-1
w/o load)
–
≤ 63
Max. permissible housing temperature
[°C]
–
+80
Ambient temperature [°C]
–
see Chapter 10.4 "Specifications for
Lubrication
–
High-performance lubricating grease
based on mineral oil
Direction of rotation
–
In- and output same direction
Mass moment of inertia J
1
[kgcm
2
]
Refers to the drive
24
2.1
2.1
2.1
2.1
2.1
38
9.2
9.2
1.4
9.1
9.1
a
In the case of mounting position V1, reduce the average drive speed n
1N
by 20%.
b
No-load running torques diminish during operation
c
Refers to the center of the output shaft or flange
Tbl-29: SP
+
140, 2–stage, i = 40 – 100: Technical data for use in potentially explosive atmospheres