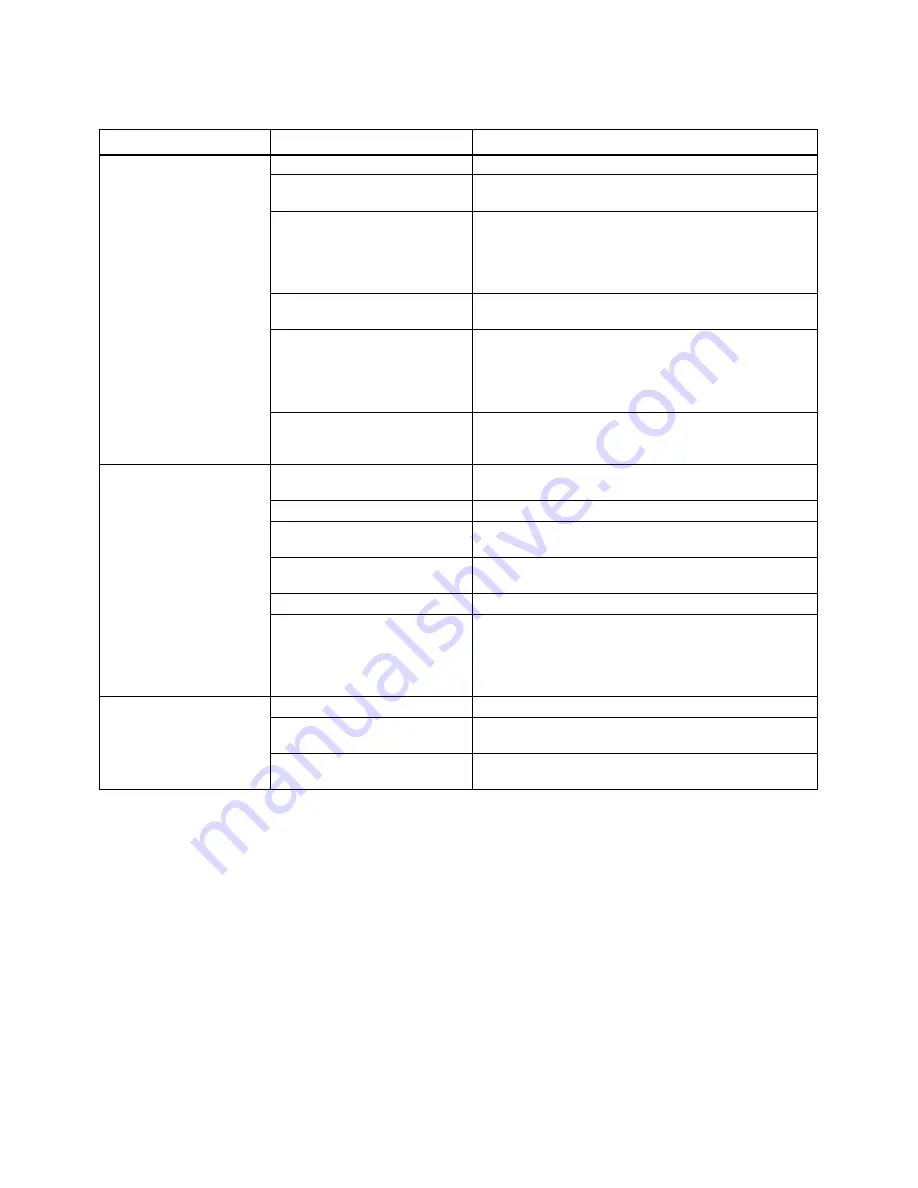
18
Troubleshooting
Troubleshooting – Blade and Cutting Problems
Problem Probable
Cause
Solution
Incorrect lubricant/coolant fluid
Ensure proper coolant flow.
Material too hard
Check the cutting speed, feed speed and air pressure
parameters and the type of blade you are using.
Disc not worn--in correctly
With a new blade it is necessary to start cutting at half
feeding speed. After the wearing--in period (a cutting
surface of about 300 cm2 for hard materials and about
1000 cm2 for soft materials) the cutting and feed
speeds can be brought up to normal values
Disc with excessively fine
tooth pitch
The swarf wedges into the bottom of the teeth causing
excessive pressure on the teeth themselves
New blade inserted in a
partially completed cut
The surface of the cut may have undergone work
hardening. When starting work again, use a lower
cutting speed and head feed speed. A tooth from the
old blade may be left in the cut: check and remove
before starting work again.
Teeth breaking
Work piece not clamped firmly
in place
Any movement of the work piece during cutting can
cause broken teeth: check the vise, jaws and clamping
pressure.
Feed speed too slow
The blade runs over the material without removing it:
increase feed speed.
Cutting pressure too high
Reduce cutting pressure.
Blade speed too high
The teeth slide over the material without cutting it:
reduce the blade speed.
Insufficient coolant
Check the coolant level and clean coolant lines and
nozzles.
Incorrect fluid concentration
Check and use the correct concentration.
Rapid tooth wear
Material defective
The materials may present altered zones either on the
surface, such as oxides or sand, or in section, such as
under-cooled inclusions. These zones, which are
much harder than the blade, cause the teeth to break:
discard or clean these materials.
Feed speed too high
Reduce blade speed.
Teeth in contact with material
before starting the cut
Always check the position of the blade before starting
a new job.
Broken blade
Insufficient coolant
Check the coolant level and clean coolant lines and
nozzles.
Summary of Contents for -SX
Page 7: ...7 FK350 Features FK350 Cold Saw FK350 SX Cold Saw ...
Page 21: ...21 Head Assembly FK350 FK350 SX ...
Page 23: ...23 Power Feed Assembly FK350 SX ...
Page 27: ...27 Stand Assembly FK350 SX ...
Page 29: ...29 Base Assembly FK350 ...
Page 31: ...31 Base Assembly FK350 SX ...
Page 33: ...33 Manual Vise Assembly FK350 ...
Page 35: ...35 Power Vise Assembly FK350 SX File 27 ...
Page 37: ...37 Guard Assembly FK350 FK350 2SX ...
Page 40: ...40 Pneumatic Drawing FK350 SX Wiring Diagram FK350 ...
Page 41: ...41 Wiring Diagram FK350 SX ...
Page 42: ...42 NOTES ...
Page 43: ...43 NOTES ...