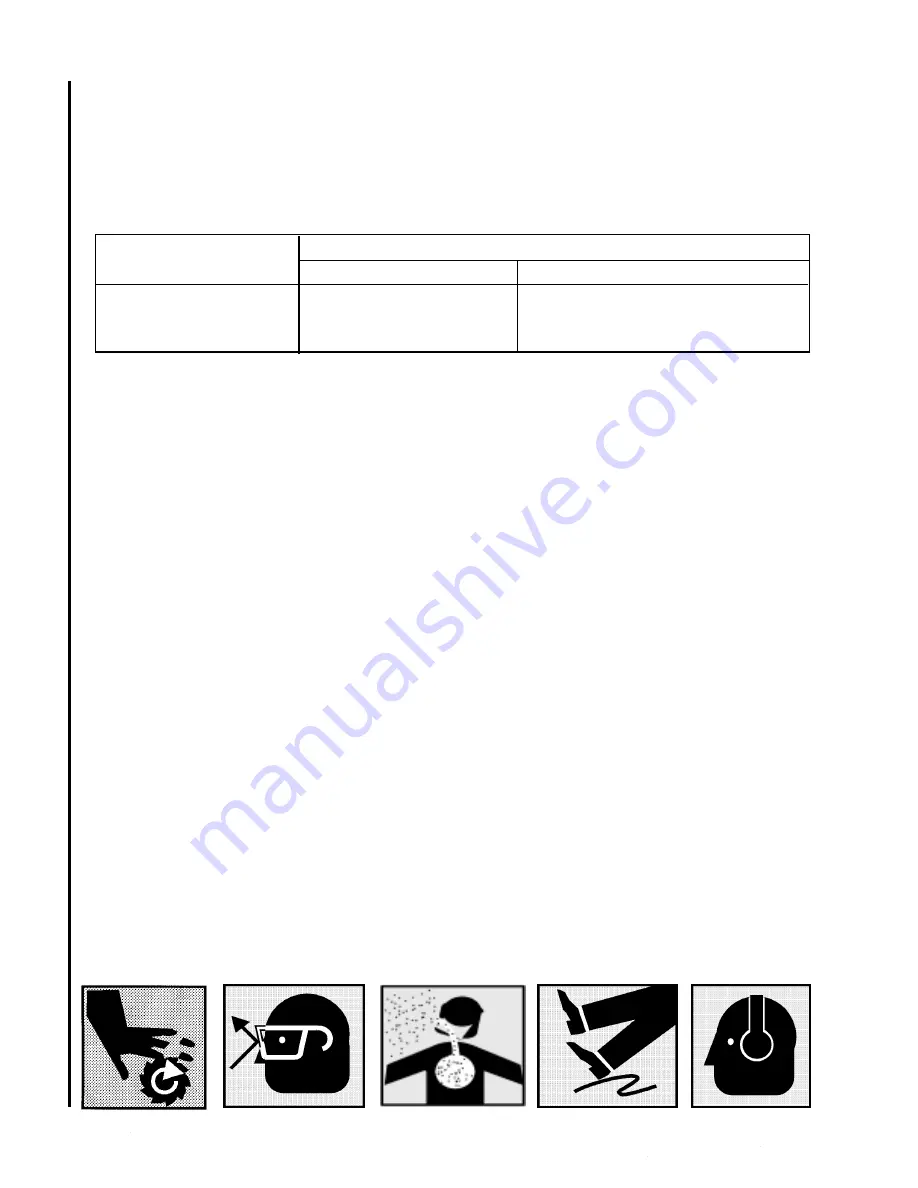
6
A B C
D E
General electrical cautions
The drill press should be grounded in accordance
with the National Electrical Code and local codes
and ordinances. This work should be done by a
qualified electrician. The drill press should be
grounded to protect the user from electrical shock.
Wire sizes
Caution:
for circuits which are far away from the
electrical service box, the wire size must be
increased in order to deliver ample voltage to the
motor. To minimize power losses and to prevent
motor overheating and burnout, the use of wire sizes
for branch circuits or electrical extension cords
according to the following table is recommended.
AWG (American wire gauge) number
Conductor length
240 volt lines
120 volt lines
0-50 feet
No. 14
No. 14
50-100 feet
No. 14
No. 12
Over 100 feet
No. 12
No. 8
5. Keep hands in sight. Do not put hands or fingers
around, on, or below any rotating cutting tools.
Leather safety gloves should be used when handling
any sharp objects or cutting tools. See Figure A.
6. Always wear protective eye wear when operating,
servicing or adjusting machinery. Eyewear shall be
impact resistant, protective safety glasses with side
shields complying with ANSI Z87.1 specifications.
Use of the eye wear which does not comply with
ANSI Z87.1 specifications could result in severe
injury from breakage of eye protection. See Figure
B.
7. When drilling in material which causes dust, a
dust mask shall be worn. See Figure C.
8. Avoid contact with coolant, especially guarding
the eyes.
9. Non-slip footwear and safety shoes are recom-
mended. See Figure D.
10. Wear ear protectors (plugs or muffs) during
extended periods of operation. See Figure E.
Safety Instructions for Drill
Presses
1. All work shall be secured using either clamps or a
vise to the drill press table. It is unsafe to use your
hands to hold any workpiece being drilled.
2. Drill press head and table shall be securely
locked to the column before operating the drill press.
This must always be checked prior to starting the
machine.
3. Always use the correct tooling. Tooling shall
always be maintained and properly sharpened. All
tooling must be run at the proper speeds and feeds
as they apply to the job. Use only recommended
accessories and follow those manufacturers instruc-
tions pertaining to them. Tooling shall be not be
forced in to any workpiece but fed according to the
proper specifications. Failure to follow these instruc-
tions will not only ruin the tooling as well as the
machine, but can cause serious injury.
4. Never brush away any chips while the machine is
in operation. All clean up should be done when the
machine is stopped.