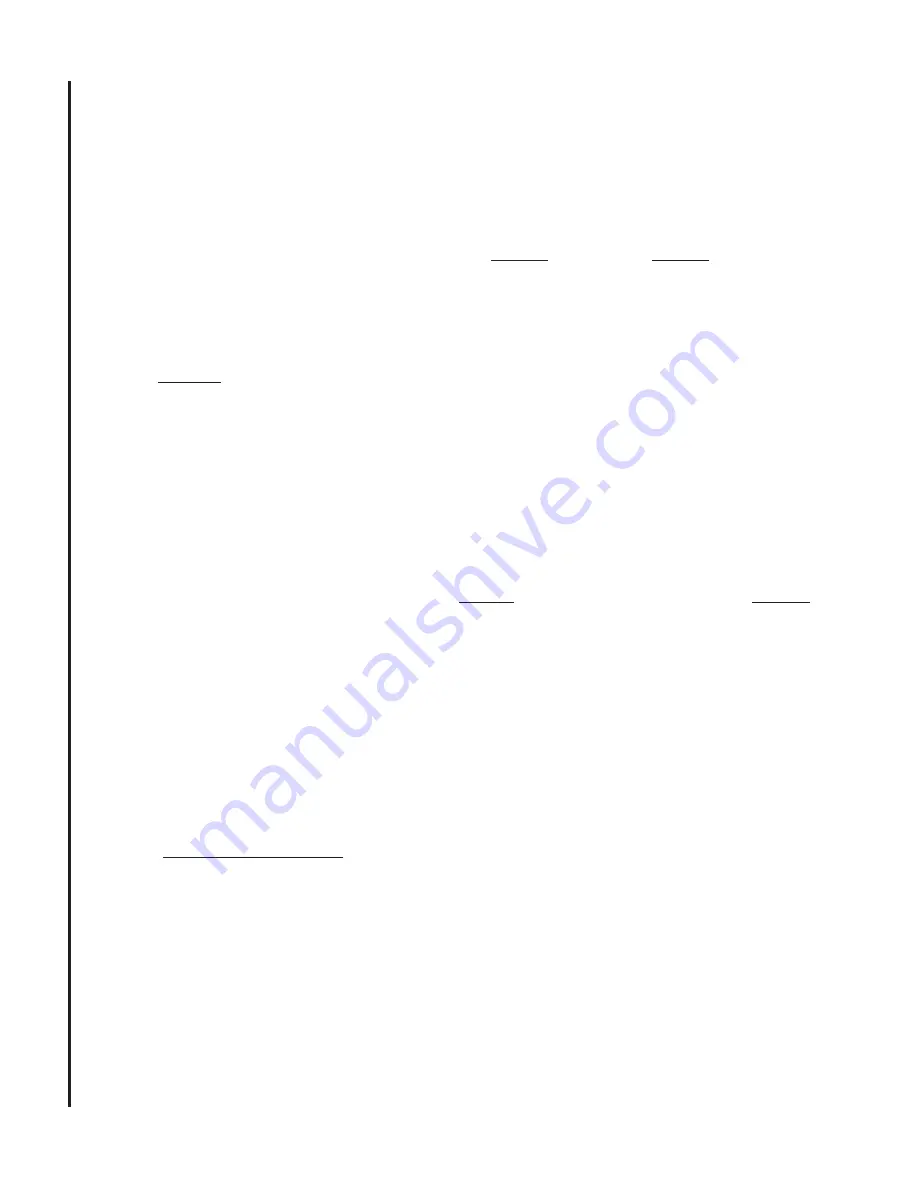
12
Feeds for Drilling
The feed of a drill is governed by the size of the tool
and the material drilled. Because the feed rate
partially determines the rate of production and also is
a factor in tool life, it should be chosen carefully for
each job. In general, the most effective feeds will be
found in the following ranges:
Diameter of Drill
Feed per Revolution
(inches)
(inches)
Under 1/8 .....................0.001 to 0.002
1/8 to 1/4 ......................0.002 to 0.004
1/4 to 1/2 ......................0.004 to 0.007
1/2 to 5/8 ......................0.007 to 0.015
Indication of Extreme Speeds and Feeds
A drill that splits up the web is evidence of too much
feed or insufficient tip clearance at the center as a
result of improper grinding. The rapid wearing away
of the extreme outer corners of the cutting edges
indicates that the speed is too high. A drill chipping
or braking out at the cutting edges indicates that
either the feed is too heavy or the drill has been
ground with too much tip clearance.
Speeds for High Speed Steel Drills
Speed
Material
In SFPM
Alloy Steel — 300 to 400 Brinell ...................... 20 - 30
Stainless Steel ................................................. 30 - 40
Automotive Steel Forgings ............................... 40 - 50
Tool Steel, 1.2C ............................................... 50 - 60
Steel, .4C to .5C ............................................. 70 - 80
Mild Machinery Steel, .2C to .3C ................... 80 - 110
Hard Chilled Cast Iron ..................................... 30 - 40
Medium Hard Cast Iron ................................. 70 - 100
Soft Cast Iron ............................................. 100 - 150
Malleable Iron ................................................. 80 - 90
High Nickel Steel or Monel .............................. 40 - 50
High Tensile Bronze ....................................... 70 -150
Ordinary Brass and Bronze ........................ 200 - 300
Aluminum and its Alloys .............................. 200 - 300
Magnesium and its Alloys ............................ 250 - 400
Slate, Marble, and Stone .................................. 15 -25
Plastics and similar material (Bakelite) ........ 100 - 150
Wood ........................................................... 300 -400
Titanium Alloys ................................................ 10 - 25
Titanium Alloy Sheet ........................................ 50 - 60
In cases where carbon steel drills are applicable, the
drill should be run at speeds of from 40 to 50 percent
of those given above.
Operating Precautions
The following operating and safety precautions must
be observed in order to avoid harm to the operator or
damage to the drill press.
1.
The head assembly must be locked to the
column so the thrust produced by drilling will not
force the head assembly up the column.
2.
The work table must be locked to the column so
it will not be forced down the column.
3.
Before drilling, release the quill lock nut to
permit free travel of the quill.
4.
Be sure the belt is tightened to the proper
tension.
5.
DO NOT
start to drill the workpiece until making
certain the workpiece is held down securely.
6.
MAKE SURE THE DRIVE MOTOR IS RUN-
NING BEFORE
turning the speed control
handwheel in either direction.
7.
Point of operation protection is required for
maximum safety. This remains the responsibil-
ity of the user/purchaser since conditions differ
between jobs.
8.
Make sure the drill is secured in the spindle or
check before attempting to use the drill press.
9.
Make sure the spindle taper is clean and free of
burrs, scoring, and galling to assure maximum
gripping.
10. Lock the quill in position when using and side-
loaded tool.
Drilling Recommendations
Speeds for Drilling
The speed of a drill is usually measured in terms of
the rate at which the outer periphery of the tool
moves in relation to the work being drilled. The
common term for this is Surface Feet per Minute
(SFM). The relationship of SFM is expressed in the
following formulas:
SFM = 0.26 X rpm X Drill Diameter (in inches)
RPM = 3.8 x ________SFM__________
Drill diameter (in inches)
In general, the higher the speed the shorter the drill
life. Operating at the low end of the speed range for
a particular material will result in longer life. The most
efficient speed for operating a drill depends on many
variables:
1.
Composition and hardness of material.
2.
Depth of the hole.
3.
Efficiency of the cutting fluid.
4.
Type and condition of the drilling machine.
5.
Desired quality of the hole.
6.
Difficulty of set-up.
Summary of Contents for 2221VS
Page 2: ......
Page 13: ...13 Wiring Diagram Models 2221 2223...
Page 18: ...18 Exploded View Drill Head Manual Speed Control Models 2221VS and 2223VS...
Page 20: ...20 Exploded View Drill Head Inverter Speed Control Models 2232AC and 2234AC...
Page 23: ...23 Exploded View Spindle Components All Models...
Page 25: ...25 Exploded View Table and Base All Models...
Page 27: ......
Page 28: ...WMH TOOL GROUP 2420 Vantage Drive Elgin IL 60123 Phone 800 274 6848...