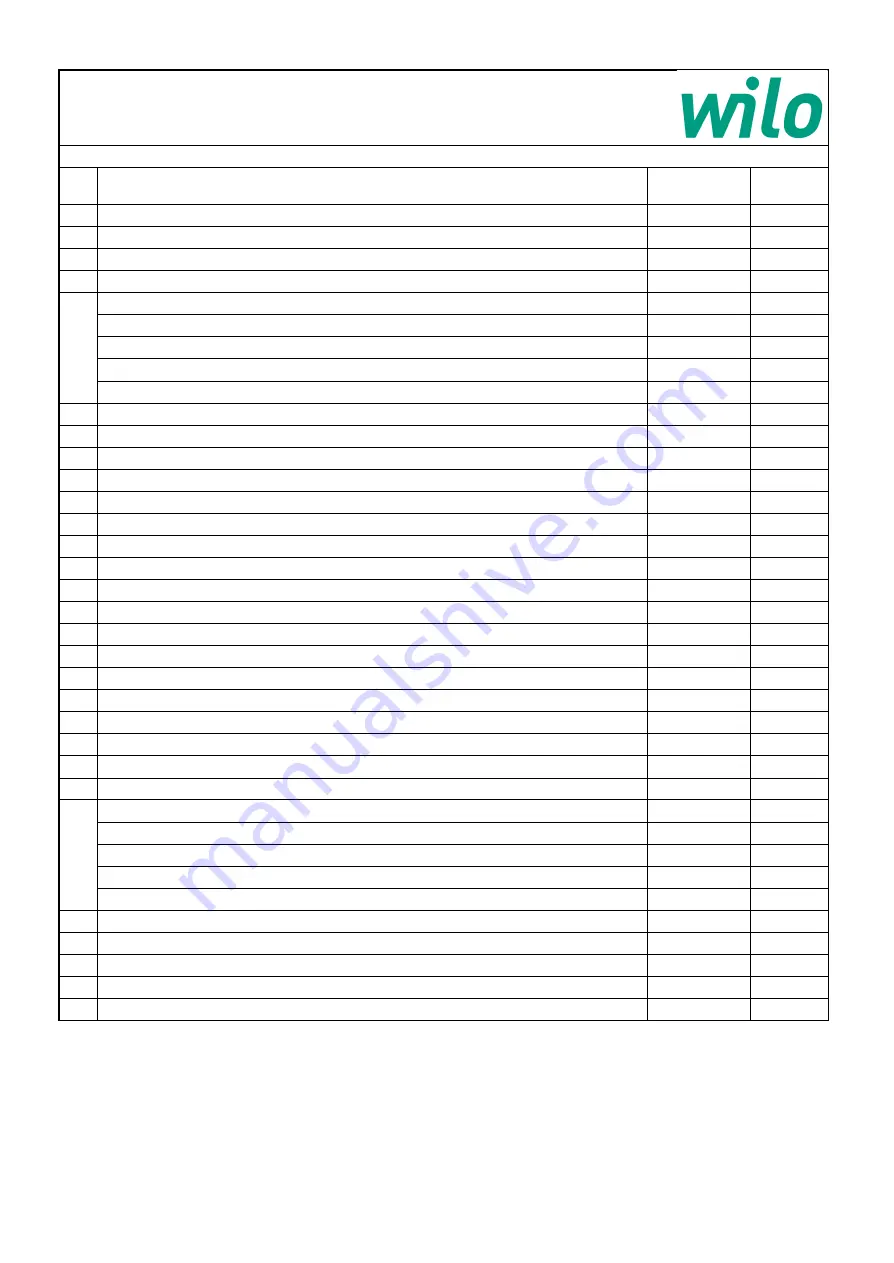
Pre-commissioning checklist Pump with Engine
Sr.
No.
Activities
Checked on
Remarks
1
Levelling of Pump set
2
Alignment with and without piping
3
Flushing of pipelines and ensures no leakages
4
Availability of sufficient liquid in sump/suction as per specifications
5
Installation of all instruments
Suction and delivery pressure gauges
Pressure switches
Temperature gauges
Any other as supplied/specified
6
Operation of suction, delivery and inline valves
7
Proper supports for piping and other allied equipment
8
Engine is installed properly on foundation with AVM pads
9
In case of HE cooled engine, all external water connections are done
10
Availability of flushing/sealing liquid for stuffing box
11
Availability of sufficient cooling liquid for bearings as specified
12
Free rotation of pump and drive shafts
13
Batteries are fully charged
14
Battery cables and lead are available
15
Exhaust silencer and all required exhaust piping is completed
16
Fuel tank is supplied. Supply & return fuel lines connected to engine
17
Engine coupled with water pump and all discharge piping is completed
18
Lube oil, coolant and fuel is available at site
19
Lubrication of bearings
20
Checking of insulation resistance of motor (if supplied by WILO M&P)
21
Proper cable termination (Clients Scope)
22
Motor Protection Relay Setting (Check with Clients)
22
Check all interlocks as specified/provided
23
No load trial operation of drive
Direction of rotation is ok
Noise and vibration are within limits
Bearing temperatures and winding temperatures are within limits
Overall operation is satisfactory
24
Coupling of pump and drive and free rotation of shafts in coupled condition
25
Suction valve is fully opened
26
Pump is fully primed, and all air is vented
27
Delivery valve is closed (if required)
28
Emergency shutdown is possible
Installation and operating instructions WILO-Split Case Pumps
35