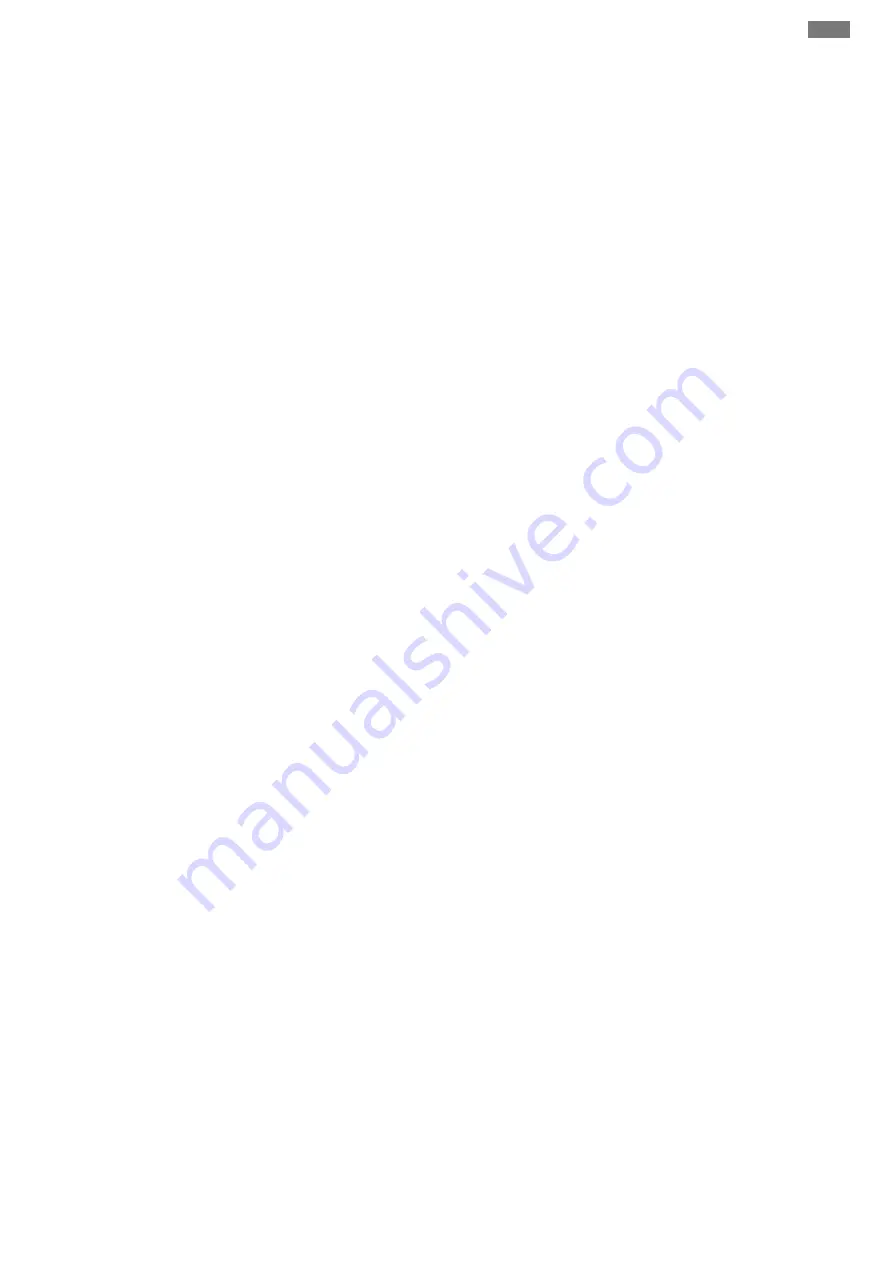
en
Installation and operating instructions • Wilo-Rexa PRO-S • Ed.01/2022-03
27
•
Maintenance work: trained sewage technology professional
Application/disposal of operating fluids used, basic engineering knowledge (installation/
dismantling)
9.2
Operator responsibilities
•
Provide the necessary protective equipment and make sure that the personnel wears it.
•
Collect operating fluids in suitable tanks and dispose of properly.
•
Dispose of protective clothing used in accordance with regulations.
•
Use only original parts of the manufacturer. The use of any non-original parts releases
the manufacturer from any liability.
•
Collect any leakage of fluid and operating fluid immediately and dispose of it according
to the locally applicable guidelines.
•
Provide the tools required.
•
If flammable solvents and cleaning agents are used, fire, naked flames and smoking are
prohibited.
•
Document maintenance tasks in the system’s inspection list.
9.3
Operating fluid
9.3.1
Oil types
•
ExxonMobile: Marcol 52
•
ExxonMobile: Marcol 82
•
Total: Finavestan A 80 B (NSF-H1 certified)
9.3.2
Filling quantities
The filling quantity depends on the motor power (see rating plate “P
2
”):
•
1.1 kW = 900 ml (30 US.fl.oz)
•
1.5 kW = 900 ml (30 US.fl.oz)
•
2.5 kW = 900 ml (30 US.fl.oz)
•
3.9 kW = 1500 ml (50.5 US.fl.oz)
•
5.0 kW = 1500 ml (50.5 US.fl.oz)
9.4
Maintenance intervals
•
Regularly carry out maintenance tasks.
•
Contractually adjust maintenance intervals depending on the actual environmental con-
ditions. Contact customer service.
•
If strong vibrations occur during operation, check the installation.
9.4.1
Maintenance intervals for normal
conditions
8000 operating hours or after 2 years
•
Visual inspection of the connection cables
•
Visual inspection of accessories
•
Visual inspection of the coating and housing
•
Function test of monitoring devices
•
Sealing chamber oil change
NOTICE! If a sealing chamber monitoring is installed, the oil
is changed according to the indicator!
5000 operating hours or after 10 years
•
Complete overhaul
9.4.2
Maintenance intervals for use in
sewage lifting units
When the pump is used in sewage lifting units inside buildings or on plots of land, carry out
maintenance intervals and measures in accordance with
DIN EN 12056‑4
!
9.4.3
Maintenance intervals for harsh
conditions
Under the following operating conditions, shorten the specified maintenance intervals in
consultation with the customer service:
•
Fluids with long-fibre components
•
Turbulent inlet (e.g. due to air entry, cavitation)
•
Highly corrosive or abrasive fluids
•
Strongly gassing fluids
•
Operation at an unfavourable duty point
•
Pressure surges
If there are harsh operating conditions, it is recommended to conclude a maintenance con-
tract.