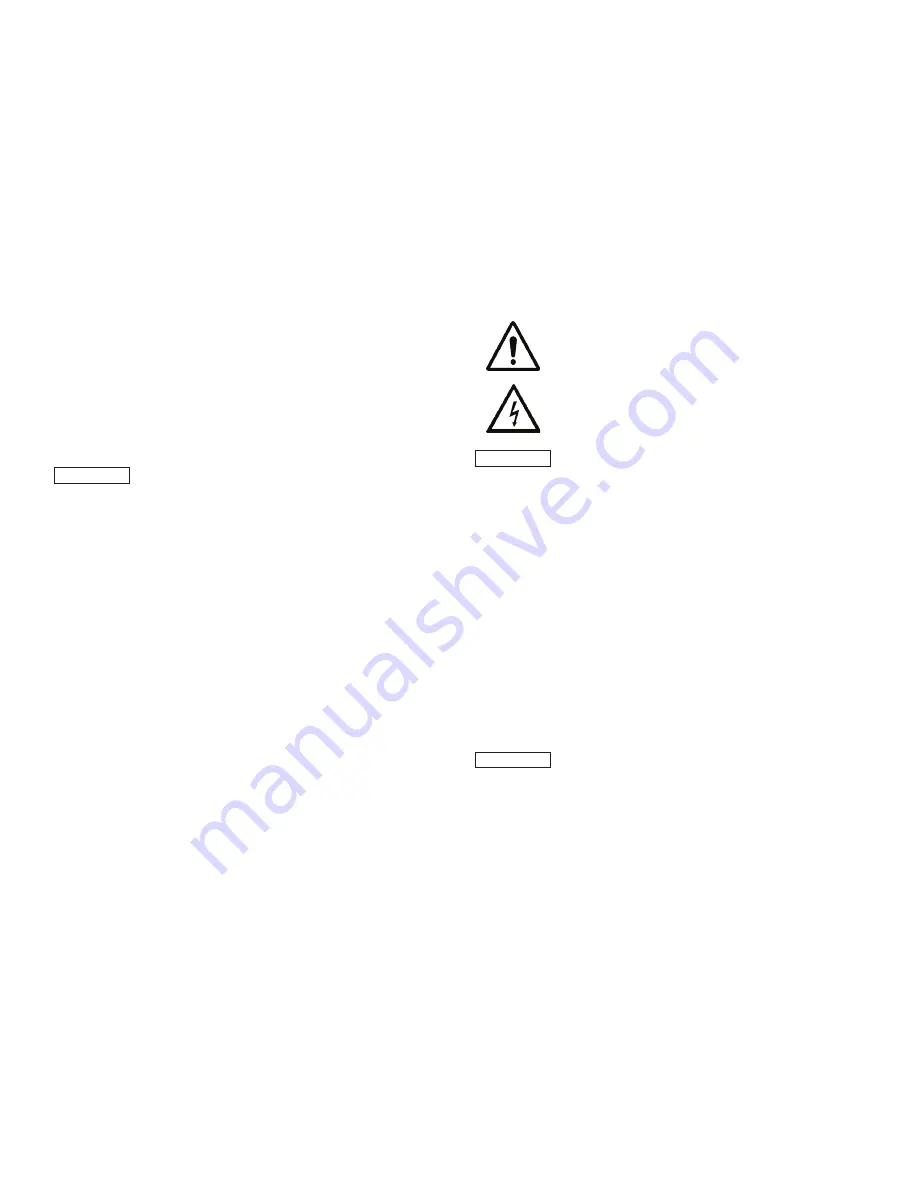
3
Wilo TWI - Installation and Operation Manual
4.3
Accessories
Accessories must be ordered separately.
• Switching/controlling equipment (motor prot
pump control) assembly
• Float
• Shut-off valves
• Manometer
• Safety valve
• Dry-run
• Electrodes
• Float switch
• Motor cable as assembly (incl. plug)
• Heat-shrink cable connections
• Steel cable (stainless steel)
• Pressure vessel
• Cooling-shroud (stainless steel/PVC)
• Etc.
1 Assembly / Installation
The pump can be operated either vertically or horizontally
(for horizontal position only with a cooling-shroud).
5.1
Assembly
• The bore-holes or pump stations must be created/
arranged in accordance with the generally applicable
technical rules.
• Please ensure that the flow of water in the bore-hole or
well is sufficient for the capacity of the pump.
• Ensure that the pump never runs dry and make sure that
even in dry periods the water level never falls below the
pump’s check valve (uppermost position).
In the case of installation in a deep well (well shaft diameter
greater than a bore-hole), a reservoir, horizontal installation
or in a deep well, a cooling-shroud (accessory) must be
fitted to the unit to ensure the motor is properly cooled (fig.
2, pos.
A).
• It must be ensured that the well shaft in the bore-hole
has a constant internal diameter to allow the pump to be
lowered freely for the entire depth of the shaft.
• Never raise or lower the pump by the electric cable.
• The electrical connection and extension of the motor
cable must take place before the pump is lowered and be
tested/measured to ensure they are working.
• The final installation position must be guaranteed such
that the pump sits at least 1 foot above the bottom of
the bore-hole or well (fig. 1).
• The rating plate must be affixed in the immediate vicinity
of the well head to allow access at all times to the unit’s
technical data.
• Before lowering (and while lowering in deep bore-holes)
the insulation resistance of
• The motor and cable must be measured several times
(min. 2 M).
5.2
Hydraulic connections (see fig. 1)
• Connections to pipes. 1” through 6” depending on size
of pump. In the case of larger types (8” / 10”), the pump
is only connected directly to the pipework.
• It is recommended that a check valve be fitted every
200 Feet to the surface of the borehole.
ATTENTION!
5.3
Electrical Connection
Electrical work must be carried out by a qualified contractor
strict compliance with local regulations.
The maximum cable length depends on the nominal motor
current and the permissible drop in voltage over the entire
cable length. Consult motor manufacturer’s documentation
for more information.
A faulty electrical connection will result in damage to the
motor.
6 Operation
6.1
Controlling the direction of rotation in 3-phase
installations:
To determine the correct direction of rotation for the pump,
only the shutoff pressure at the well head needs to be
checked, taking into account that the correct motor
direction of rotation generates the greater pressure.
• To rectify an incorrect direction of rotation swap any
two phases in the switchbox or motor protection switch.
See motor manufacturer’s documentation for more
information.
6.2
Operation
The pump must never run while dry, not even for brief
periods.
7 Maintenance
Before carrying out any maintenance work, switch off the
pump and ensure that it cannot be switched on again by
unauthorized people. Never carry out work on a running
pump.
No special maintenance is required during normal operation.
7.1
Spare parts
Please contact Wilo Customer Service directly for spare
parts, standard replacements or repairs to the hydraulic
pump parts.
ATTENTION!
ATTENTION!