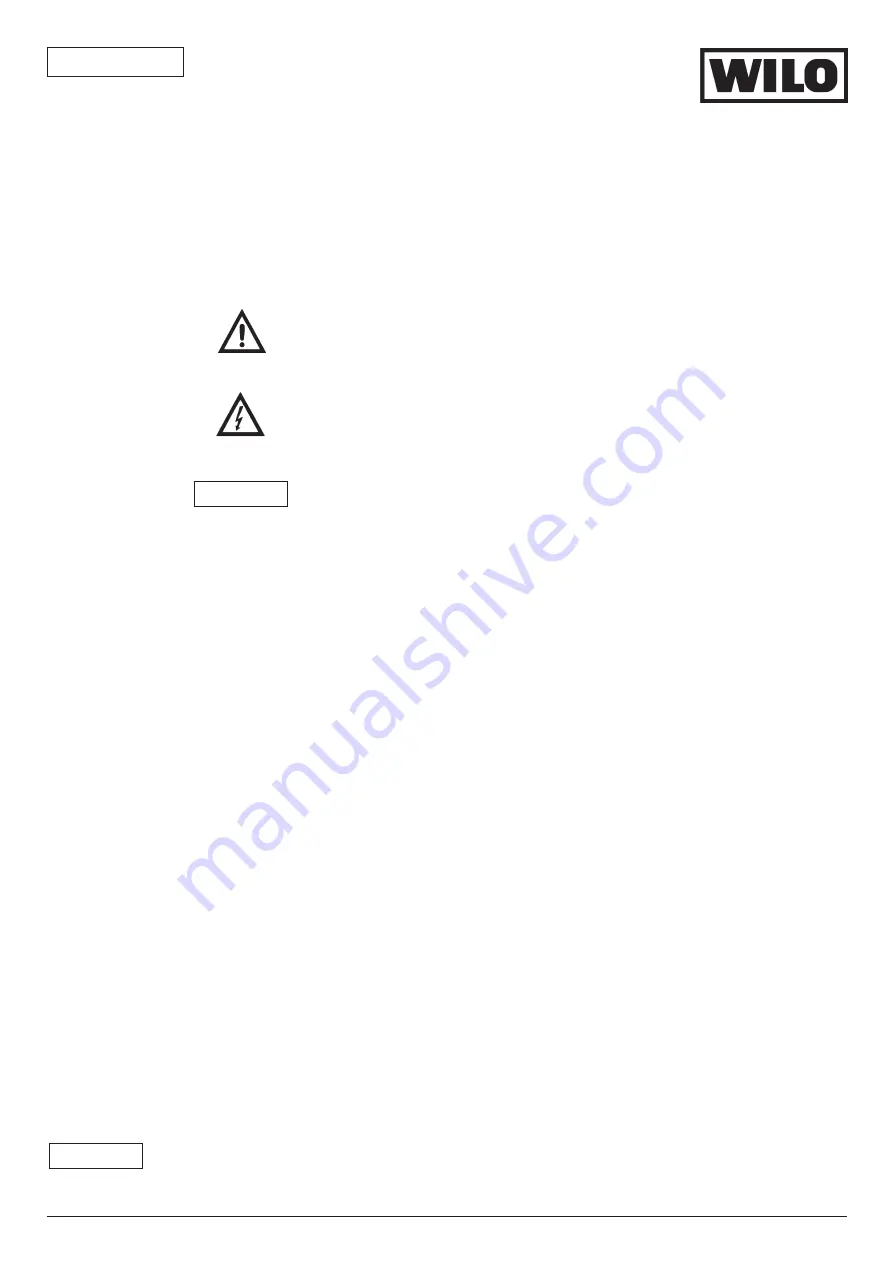
ENGLISH
2. Safety precautions
These instructions contain important information which must be
followed when installing and operating the pump. It is therefore im-
perative that they be read by both the installer and the operator before
the pump is installed or started up.
Both the general safety instructions in the ‘Safety precautions’ section
and those in subsequent sections indicated by danger symbols should
be carefully observed.
2.1 Danger symbols used in these operating instructions
Safety precautions in these operating instructions which, if not follow-
ed, could cause personal injury are indicated by the symbol:
Safety precautions warning of danger due to electricity are indicated
by the symbol:
Safety precautions which, if not followed, could damage the pump or
installation and cause it to malfunction are indicated by the word:
2.2 Qualified Personnel
The personnel installing the pump must have the appropriate qualifica-
tions for this work.
2.3 Risks incurred by failure to comply with the safety precautions
Failure to comply with the safety precautions could result in personal
injury or damage to the pump or installation. Failure to comply with the
safety precautions could also invalidate any claim for damages.
In particular, failure to comply with these safety precautions could give
rise, for example, to the following risks:
– the failure of important parts of the pump or installation,
– personal injury due to electrical and mechanical causes.
2.4 Safety precautions for the operator
Existing regulations for the prevention of accidents must be followed.
To prevent the risk of electric shock or electrocution, VDE regulations
and those of the local supply company must be followed.
2.5 Safety precautions for inspection and installation
The operator must ensure that all inspection and installation work is
carried out by authorized and qualified specialists who have carefully
studied these instructions. In principle, work should not be carried out
on a running pump or installation.
2.6 Unauthorized alterations and manufacture of spare parts
Alterations to the pump or installation may only be carried out with the
manufacturer's consent. The use of original spare parts and accesso-
ries authorized by the manufacturer will ensure safety. The use of other
parts may invalidate claims invoking the manufacturer’s liability for any
consequences.
2.7 Improper use
The operational safety of the pump or installation supplied can only be
guaranteed if it is used in accordance with paragraph 1 of the operat-
ing instructions. The limits given in the catalogue or data sheet must
under no circumstances be exceeded.
3. Transport and storage
During transport and in storage the pump must be
protected against moisture, frost and mechanical
damage.
WARNING!
WARNING!
4. Description of product and accessories
4.1 Pump description
(Fig. 1)
The pump is a multistage (4-5 stage) self suction, horizontal high pres-
sure centrifugal pump with a block design with horizontal inlet (1) and
vertical pressure glands (2).
The hydraulic section is equipped with the given number of stage
housings (5) and impellers (6) in a modular construction. The impellers
are fitted on a single motor-pump shaft (7). The pressure casing (8)
surrounding the hydraulic section guarantees a fail-safe seal. All parts
in contact with the fluid, such as stage chambers, impellers are made
of plastic, the pressure casing is of chrome nickel steel. The shaft hole
through the pump casing is sealed to the motor with an axial face
seal (9).
The single phase motors are equipped with a thermal cut-out. This
switches off the motor when the permissible temperature of the motor
coil is exceeded and switches it back on again automatically once it
has cooled down.
Low-water protection. The pump and in particular the axial face seal
must not run dry. Low-water protection should be provided by the
customer by fitting the relevant parts from the WILO range of accesso-
ries.
4.2 Components supplied
– EM or DM version of pump,
– Installation and Operating Instructions
4.3 Accessories
Accessories must be ordered separately.
– Suction tube, foot valve,
– WV/COL switching unit with relevant accessories for automation,
– CO-ER switching unit with relevant accessories for automation,
– Low-water protection:
– WMS kit for direct connection to the supply pipe,
– WA 65 float switch,
– SK 277 with 3 dipped electrodes,
– WVA pressure switch,
– WILO fluid control (only for EM-version),
– Installation switching:
– WAO 65 float switch.
5. Assembly and Installation
5.1 Installation
Fig. 2 (pump under pressure) and Fig. 3 (pump in suction) shows a
typical pump installation. Installation and assembly instructions, which
must be observed with this type of operation, are listed as follows:
– Before installing the pump, make sure that all welding and soldering
on the pipe system has been completed and that the pipe system
has been completely flushed out. Foreign bodies and dirt will dam-
age the pump.
– Install the pump in a dry place free of frost.
– Leave room for maintenance work to be carried out.
– The motor ventilator inlet must be kept clear, at least 0.30 m from
the wall to the rear.
– Install in a horizontal and flat position.
– Pump in suction operation should be located as close as possible to
the water source. Limit the horizontal length of the suction pipe as
possible, to insure no losses of head. The complete suction pipeline
must be installed with continuous rise. Prevent the use of armatures
in the suction pipeline, that may reduce the suction performance.
– The pump must be held in place with two 8 mm diameter screws,
on a vibration-absorbing base. Commercially available rubber-metal
connectors can also be used to hold it in place and absorb vibra-
tions.
– To ensure that the drain valve can be accessed, the pump must be
installed with the drain valve at least 20 mm above the floor.
– The diameter of the suction pipe/-tube must never be smaller than
the one of the pump. Morover, for the pumps of 6 m
3
/h series, with
a suction height (SH) superior to 6 m, it is necessary to have a pipe
of inside
l
28 mm minimum.
8
Summary of Contents for MultiCargo MC304
Page 2: ...Fig 1 Fig 2 Fig 3...
Page 3: ...Fig 4 Fig 5...