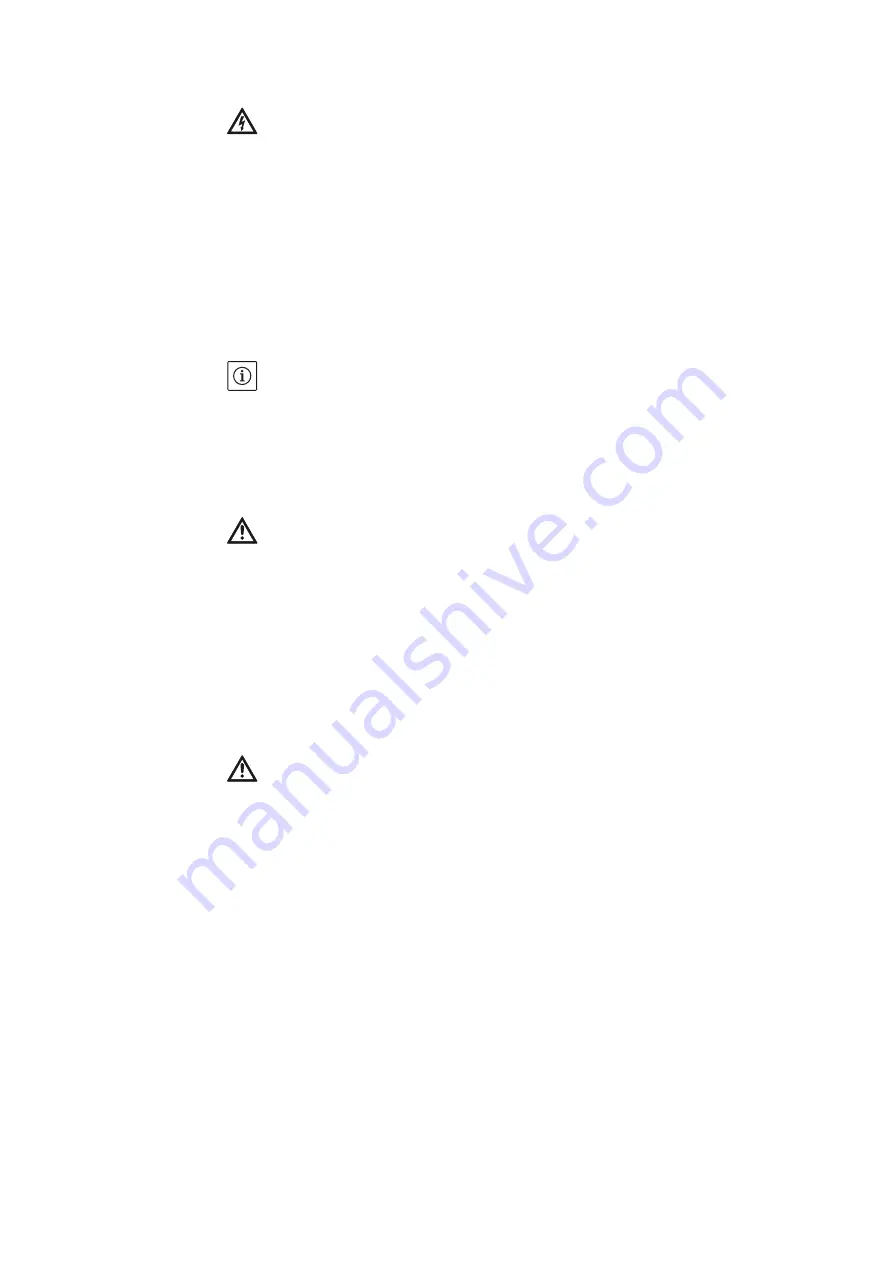
English
Installation and operating instructions Wilo-DrainLift M1/8
33
Connection of the external alarm signal
DANGER! Risk of fatal injury!
When working on the open switchgear, there is a danger of electric shock from touch-
ing the live components.
The work may only be carried out by skilled personnel.
To connect the alarm signal, switch the device so that it is voltage-free and secure it
against being switched on again without authorisation.
Observe the installation and operating instructions of the EC-Drain LS1 switchgear!
• Pull out the mains plug!
• Open the cover of the switchgear.
• Remove the protective cover from the threaded cable connection.
• Feed the cable through the screwed connection and connect to the potential-free alarm
contact according to the wiring diagram.
• After the cable has been connected for the alarm signal, seal the cover of the switchgear
and tighten the threaded cable connection.
• Plug the
mains plug back in.
NOTE: In the factory settings, the alarm signal triggers when the tank filling level is about
220 mm above the upper edge of the unit's installation surface. This is to be observed
when drainage fixtures are also to be secured with the unit's alarm which lie relatively low
(e.g. floor drains).
8 Commissioning
It is recommended that commissioning be carried out by Wilo After-Sales Service.
8.1 Checking the unit
CAUTION! Risk of damage!
Dirt and solids as well as incorrect commissioning can lead to damage to the unit or
individual components during operation.
• Before commissioning, clean the entire unit to remove contaminants, particularly
solids.
• Observe the installation and operating instructions of the switchgear and the accesso-
ries!
Commissioning may only be carried out when the relevant safety regulations,
VDE regulations as well as regional regulations have been met.
• Check for the presence of and proper versions of all required components and connections
(inlets, discharge pipe with check valve, ventilation via the roof, floor fixation, electrical
connection).
• Check the position of the venting screw on the non-return valve to make sure the flap can
move freely in its seat and for the sealing position of the sealing nut.
CAUTION! Risk of damage!
If the venting screw with sealing nut is not in the required position, this can lead to
damage on the flap and unit, as well as to high noise development.
• Check the level control for perfect mechanical condition. To do this, open the screw lid and
check the float switch installed inside to make sure it can move easily and check that the
float and the counter nut on the rod have a tight fit. Seal the screw lid tightly again.
8.2 Initial commissioning
• Plug the mains plug in.
• Open the check valves.
• Fill the system via the connected inlet until the pump has pumped out at least twice and
the pressure pipeline is completely filled.
With the pressure pipeline filled and the inlet closed, the filling level in the tank must not
rise. If the filling level continues to rise, the flap of the non-return valve is leaky (must
check the flap and the position of the venting screw).
For a test start-up, the “manual mode” button on the switchgear can also be pressed
before reaching the switch-on level in the tank.
• Check the unit and pipe joints for impermeability and perfect function (switch the pump
on and off).