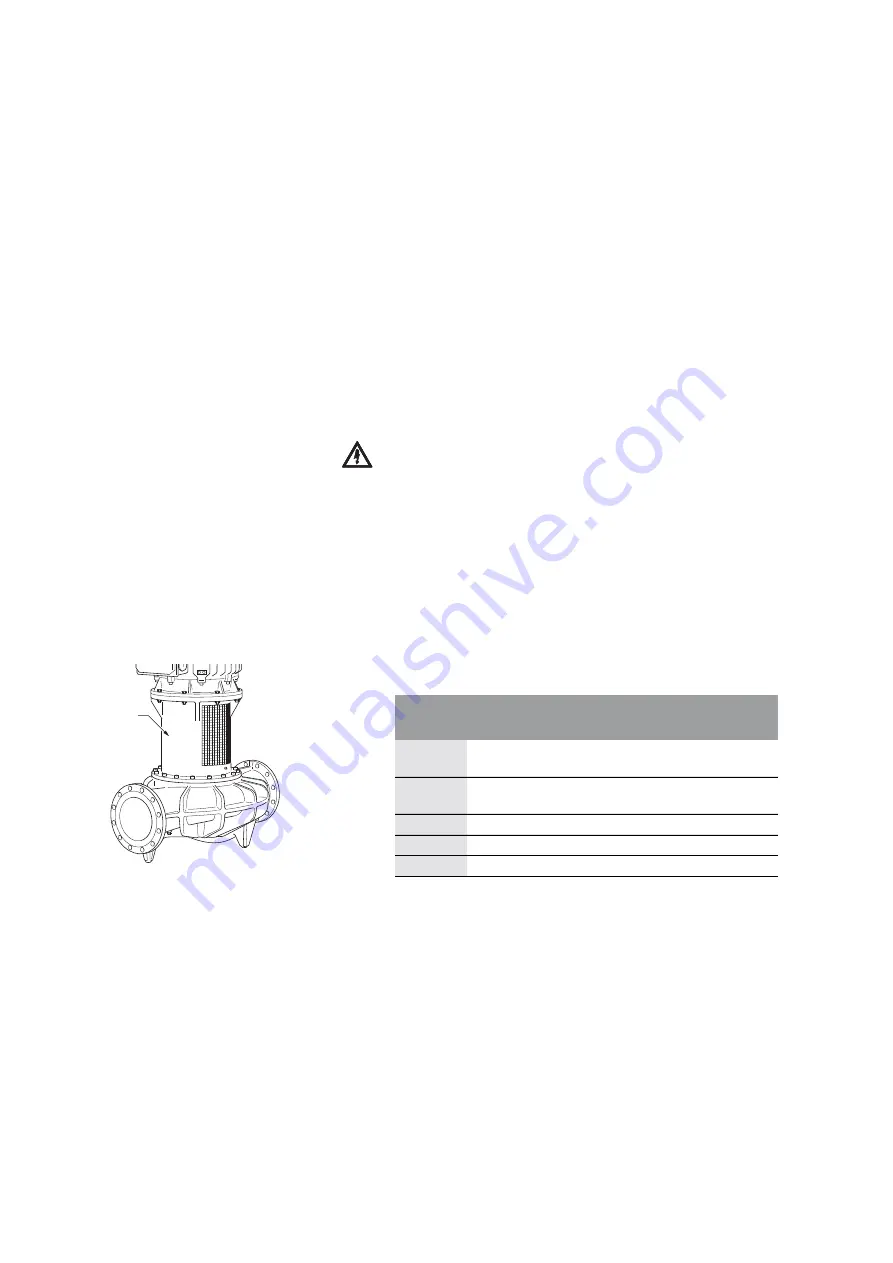
English
Installation and operating instructions Wilo-CronoLine-IL/CronoBloc-BL (with cartridge mechanical seal)
35
4
Intended use
Purpose
The glanded pumps of the IL (in-line single pump) and BL (monobloc
pumps) series are meant to be used as circulators in building services.
Fields of application
They may be used for:
• Hot-water heating systems
• Cooling and cold water circulation systems
• Process water systems
• Industrial circulation systems
• Heat carrier circuits
Contraindications
Typical installation locations are technical rooms within the building
with other domestic installations. No provision has been made for
direct installation of the device in rooms used for other purposes (res-
idential and work rooms).
For these series, it is possible to set them up outdoors only in their
corresponding, special version, on request (see chapter 7.3 "Anti-
condensation heater connection" on page 46).
CAUTION! Risk of property damage!
Non-permitted substances in the fluid can destroy the pump.
Abrasive solids (e.g. sand) increase pump wear.
Pumps without an Ex rating are not suitable for use in potentially
explosive areas.
• Intended use includes compliance with this manual.
• Any other use is regarded as non-compliant with the intended use.
5
Product information
5.1
Type key
The type key consists of the following elements:
Pump type rating plate:
Fig. 36, item 1 shows the arrangement of the pump rating plate.
Fig. 36: Arrangement of the pump rating
plate
1
Example:
IL 250/420-110/4
BL 125/315-45/4
IL
BL
Flange-end pump as
I
n-line single pump
Flange-end pump as
B
loc pump
250
Nominal diameter DN of the pipe connection
(for BL: pressure side) [mm]
420
Nominal impeller diameter [mm]
110
Rated power P
2
[kW]
4
Number of poles, motor
Summary of Contents for CronoBloc BL Series
Page 3: ...Fig 7 Fig 8 2 1 3 Fig 9 Fig 10 3 2 1 Fig 11 ...
Page 5: ...Fig 18 Fig 19 1 2 1 Fig 20 Fig 21 Fig 22 Fig 23 1 1 2 ...
Page 37: ......
Page 38: ......
Page 39: ......