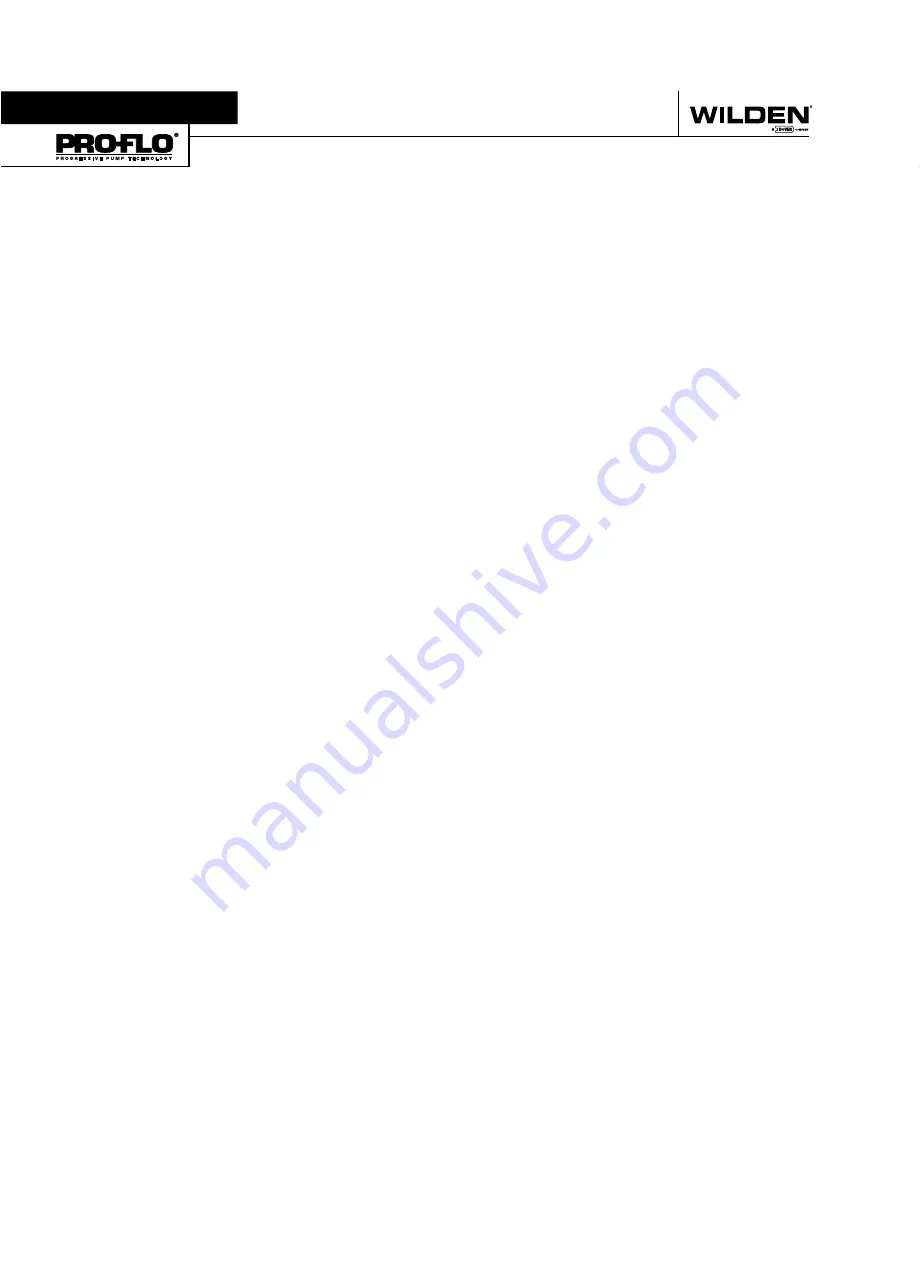
WILDEN PUMP & ENGINEERING, LLC
20
WIL-10131-E-01
The P8 and PX8 have a 51 mm (2") inlet and 51 mm (2")
outlet and is designed for flows to 587 lpm (155 gpm). The
P8 and PX8 Plastic
pump is manufactured with wetted parts
of pure, unpigmented PVDF or polypropylene. A variety of
diaphragms and o-rings are available to satisfy temperature,
chemical compatibility, abrasion and flex concerns.
The suction pipe size should be at least 51 mm (2") diam-
eter or larger if highly viscous material is being pumped.
The suction hose must be non-collapsible, reinforced type
as the P8 and PX8 are is capable of pulling a high vacuum.
Discharge piping should be at least 51 mm (2"); larger diam-
eter can be used to reduce friction losses. It is critical that all
fittings and connections are airtight or a reduction or loss of
pump suction capability will result.
For
P8 & PX8 Plastic
models, Wilden offers 150 lb. flanges. The
following details should be noted when mating these to pipe
works:
• A 60–80 shore gasket that covers the entire flange face
should be used.
• The gasket should be between 1.91 mm (.075") and 4.45
mm (.175") thickness.
• Mating flanges with flat as opposed to raised surfaces
should be used for proper mechanical sealing.
• The flanges should be tightened to aminimum of 6.8 N·m
(5 ft-lbs) but no more than 13.5 N·m (10 ft-lbs).
INSTALLATION: Months of careful planning, study, and selec-
tion efforts can result in unsatisfactory pump performance if
installation details are left to chance.
Premature failure and long term dissatisfaction can be avoided
if reasonable care is exercised throughout the installation
process.
LOCATION: Noise, safety, and other logistical factors usually
dictate where equipment be situated on the production floor.
Multiple installations with conflicting requirements can result
in congestion of utility areas, leaving few choices for addi-
tional pumps.
Within the framework of these and other existing conditions,
every pump should be located in such a way that five key factors
are balanced against each other to maximum advantage.
ACCESS: First of all, the location should be accessible. If it’s
easy to reach the pump, maintenance personnel will have an
easier time carrying out routine inspections and adjustments.
Should major repairs become necessary, ease of access can
play a key role in speeding the repair process and reducing
total downtime.
AIR SUPPLY: Every pump location should have an air line
large enough to supply the volume of air necessary to achieve
the desired pumping rate (see Section 5). Use air pressure up
to a maximum of 8.6 bar (125 psig) depending on pumping
requirements.
For best results, the pumps should use a 5µ (micron) air filter,
needle valve and regulator. The use of an air filter before the
pump will ensure that the majority of any pipeline contami-
nants will be eliminated.
SOLENOID OPERATION: When operation is controlled by
a solenoid valve in the air line, three-way valves should be
used, thus allowing trapped air to bleed off and improving
pump performance. Pumping volume can be set by count-
ing the number of strokes per minute and multiplying by
displacement per stroke.
Sound levels are reduced below OSHA specifications using
the standard Wilden muffler. Other mufflers can be used but
usually reduce pump performance.
ELEVATION: Selecting a site that is well within the pump’s
dynamic lift capability will assure that loss-of-prime trou-
bles will be eliminated. In addition, pump efficiency can be
adversely affected if proper attention is not given to site
location.
PIPING: Final determination of the pump site should not be
made until the piping problems of each possible location have
been evaluated. The impact of current and future installations
should be considered ahead of time to make sure that inad-
vertent restrictions are not created for any remaining sites.
The best choice possible will be a site involving the shortest
and straightest hook-up of suction and discharge piping.
Unnecessary elbows, bends, and fittings should be avoided.
Pipe sizes should be selected so as to keep friction losses
within practical limits. All piping should be supported inde-
pendently of the pump. In addition, the piping should be
aligned so as to avoid placing stresses on the pump fittings.
Flexible hose can be installed to aid in absorbing the forces
created by the natural reciprocating action of the pump. If
the pump is to be bolted down to a solid location, a mount-
ing pad placed between the pump and the foundation will
assist in minimizing pump vibration. Flexible connections
between the pump and rigid piping will also assist in minimiz-
ing pump vibration. If quick-closing valves are installed at any
point in the discharge system, or if pulsation within a system
becomes a problem, a surge suppressor should be installed
to protect the pump, piping and gauges from surges and
water hammer.
When pumps are installed in applications involving flooded
suction or suction head pressures, a gate valve should be
installed in the suction line to permit closing of the line for
pump service.
For P8 and PX8 Plastic models, a non-raised surfaced-flange
adapter should be utilized when mating to the pump’s inlet
and discharge manifolds for proper sealing.
The P8 cannot be used in submersible applications.
Pro-Flo X
TM
can be used in submersible applications when
using the PX single point exhaust option. If the pump is to be
used in a self-priming application, be sure that all connections
are airtight and that the suction lift is within the model’s ability.
Note: Materials of construction and elastomer material have
an effect on suction lift parameters. Please consult Wilden
distributors for specifics.
Pumps in service with a positive suction head are most effi-
cient when inlet pressure is limited to 0.5–0.7 bar (7–10 psig).
Premature diaphragm failure may occur if positive suction is
10 psig and higher.
THE P8 AND PX8 WILL PASS 6.4 MM (1/4") SOLIDS. WHEN-
EVER THE POSSIBILITY EXISTS THAT LARGER SOLID
OBJECTS MAY BE SUCKED INTO THE PUMP, A STRAINER
SHOULD BE USED ON THE SUCTION LINE.
CAUTION: DO NOT EXCEED 8.6 BAR (125 PSIG) AIR
SUPPLY PRESSURE.
S e c t i o n 6
S U G G E S T E D I N S T A L L A T I 0 N