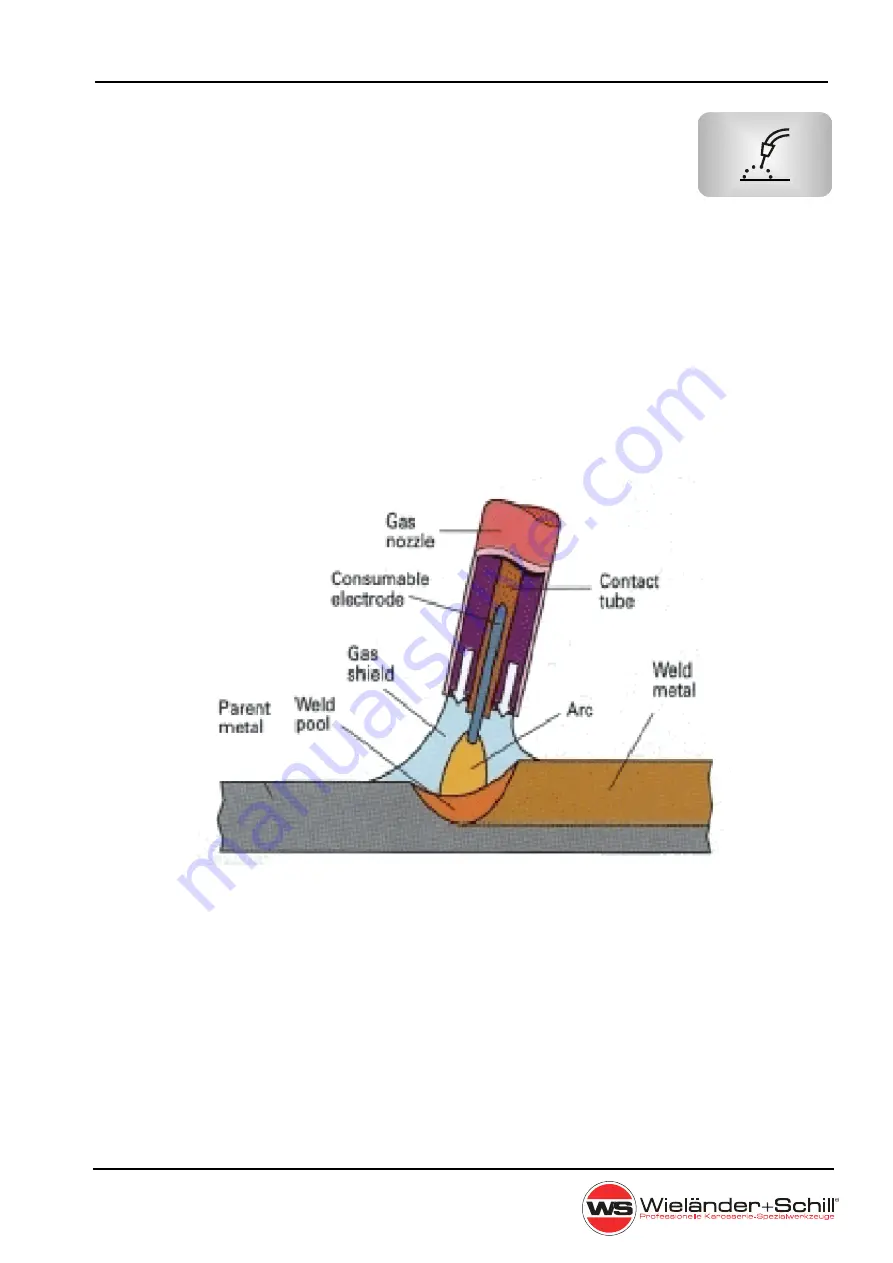
IM 240-i
Operation manual
Seite 12
4 WELDING PROCESSES
4.1
MIG/MAG Welding
Partial mechanical gas shielded arc welding (MIG), optionally as MIG (inert gas welding, EN
ISO 4063: process 131) or MAG welding (metal welding with active, ie reactive gases, EN ISO
4063: process 135), is an arc welding process in which the consumable welding wire is
continuously tracked by a variable speed motor. The usual welding wire diameters are
between 0.8 and 1.2 mm (more rarely 0.6 mm). Simultaneously with the wire feed the welding
point is supplied via a nozzle the protective or mixed gas with about 10 l / min (rule of thumb:
inert gas volume flow 10 l / min per mm welding wire diameter). This gas protects the liquid
metal under the arc from oxidation, which would weaken the weld. In metal active gas (MAG)
welding, either pure CO2 or a mixed gas of argon and small amounts of CO2 and O2 (e.g.,
"Corgon") is used. Depending on their composition, the welding process (penetration, drop
size, splash losses) can be actively influenced; Metal inert gas welding (MIG) uses argon as
a noble gas, and more rarely also the expensive noble gas helium. The MAG process is
primarily used for steels, the MIG process preferred for non-ferrous metals.
MIG/MAG welding process
For the MIG / MAG welding process, a DC current with decreasing characteristic and plus
potential at the welding wire is used.
MIG / MAG welding uses different types of arc used based on voltage and wire feed speed -
short arc, mixed arc, spray arc.
In addition to the standard arc types, there are other special shapes for special applications.