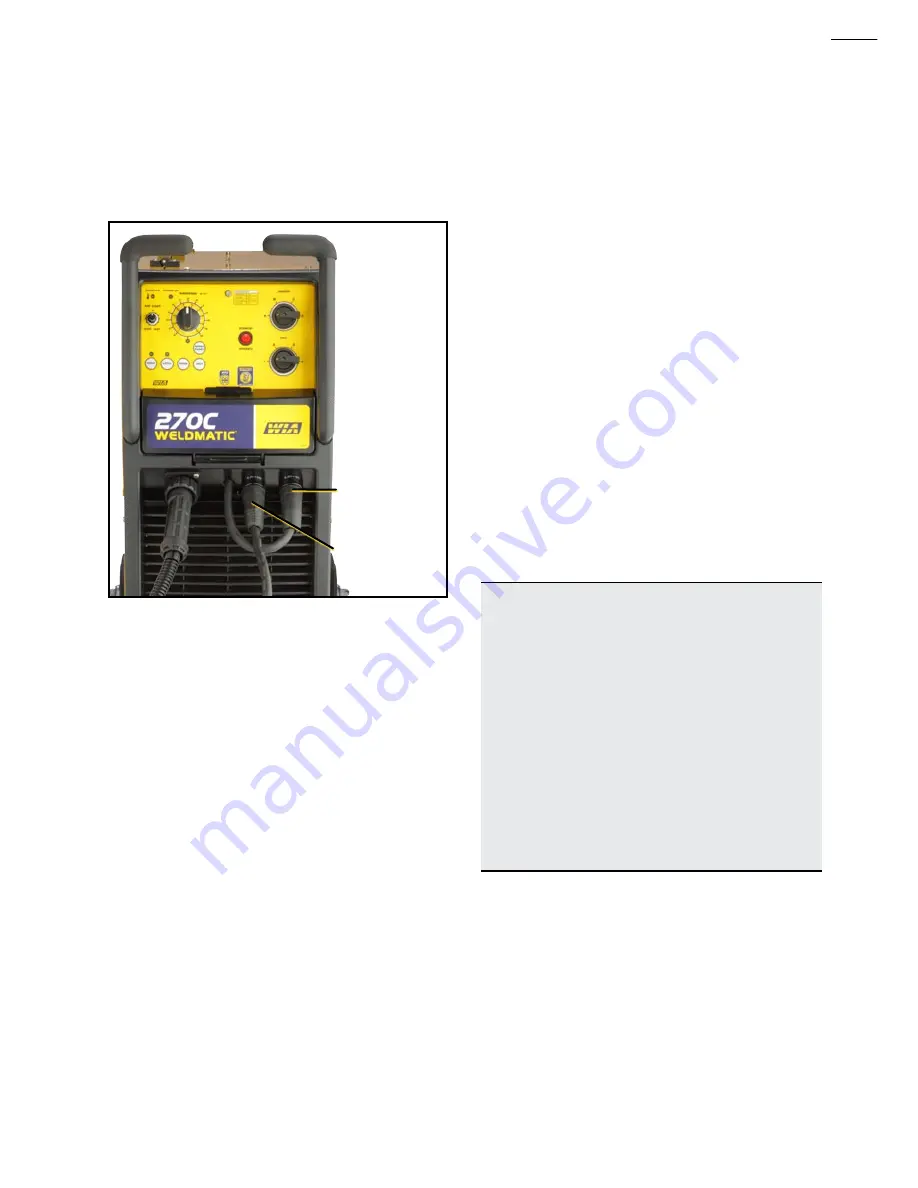
Weldmatic 270C
Model No CP136-2, Iss A 08/12
11
on the Power Source, and the ‘WELDING’
lead from the wirefeeder into the (-) socket
on the Power Source, as in Figure 4.
Fig 4
Negative Wire
To wirefeeder
To work clamp
Fitting the gas cylinder
Place the gas cylinder on the tray at the rear
of the welder. Retain the cylinder with the
chain provided.
Fit the gas regulator to the cylinder. DO NOT
apply grease or oil to these joints.
Fit the end of the supplied gas hose to the
gas larb at the rear of the machine. Secure
with clamp. Fit other end to nut and tail
already attached to regulator and secure
with clamp.
Wirefeeder
The 4RD wirefeeder is supplied fitted with
WF027 bottom rollers which are suitable for
both 0.9 mm and 1.2 mm diameter steel wire.
Fitting The Gun and Cable Assembly
The supplied welding gun/cable assembly is
equipped with a ‘Euro’ wirefeeder connector
which incorporates all required connection
points for welding current, shielding gas and
gun switch control.
To attach the gun/cable assembly to
the wirefeeder mechanism, engage the
mating parts of the male and female Euro
connectors, then rotate the locking ring
clockwise to firmly secure the connection.
Fitting the Consumable Wire
The quality of the consumable
wire greatly affects how reliably a
gas metal arc welder will operate.
For best results when welding
mild steel, we recommend quality
WIA AUSTMIG ES6. Dirty, rusty or
kinked wire will not feed smoothly
through the gun cable and will
cause erratic welding. Deposits
from the wire will clog the gun
cable liner requiring it to be
replaced prematurely.
Place the spool of welding wire onto the
spool holder. The location pin should mate
with a hole provided on the wire spool body.
Secure the spool with plastic nut. Check
the adjustment of the spool brake, which
should be set to prevent over run of the wire
spool at the end of a weld, without unduly
loading the wirefeed motor. The braking can
be adjusted by using an 8 mm allen key to
adjust Hex head bolt inside the hub.