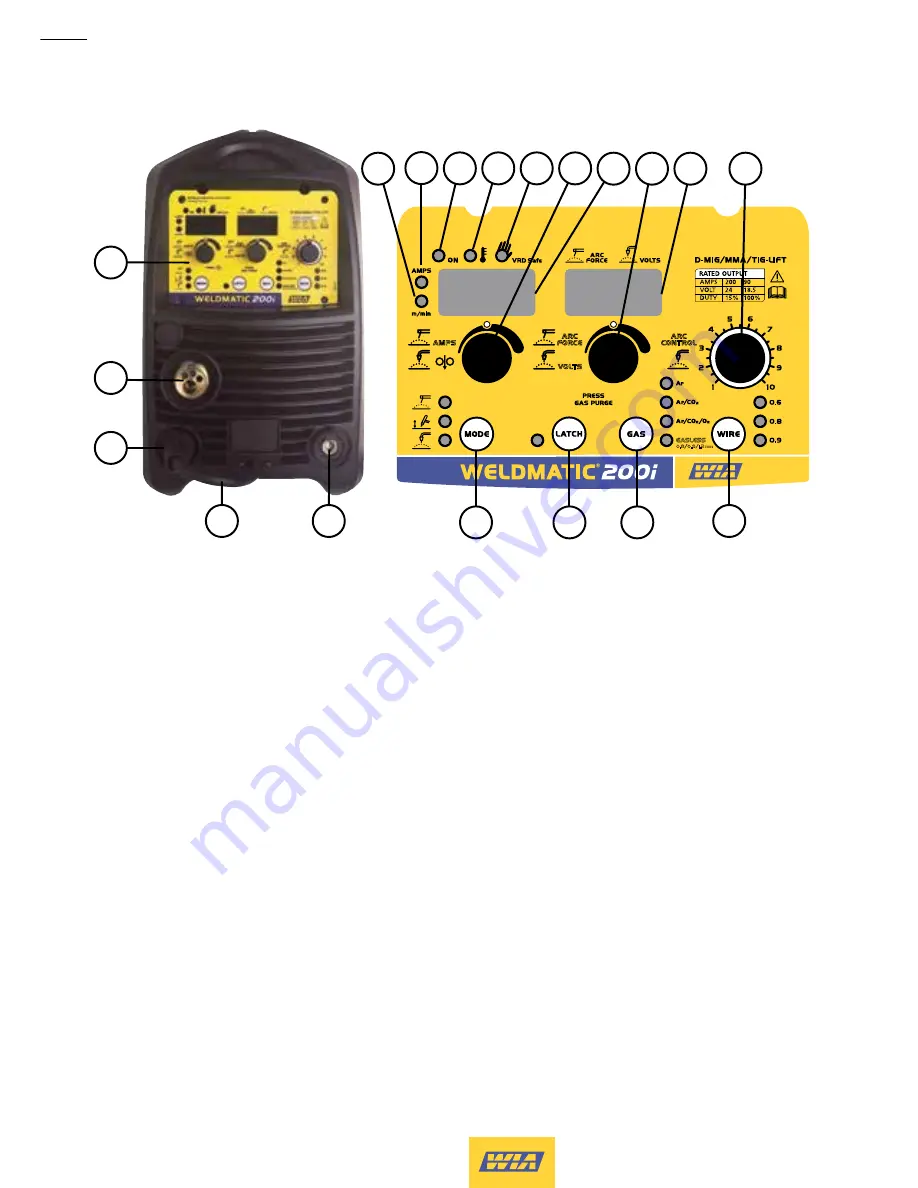
8
Operators Manual
Trusted by the best
WIN540D
AMPS
VOLTS
ARC
FORCE
ARC
CONTROL
GASLESS
0.8/0.9/1.2
mm
Fig 1
Weldmatic 200i Controls
2
1 Control Panel
2 Euro Gun/Cable Connector
3 Positive Welding Output Terminal
4 Negative Welding Output Terminal
5 Polarity Selection Cable
6 m/min Indicator
When this light is on the Digital Display
(12) is indicating the selected wire speed in
metres per minute (MIG Mode).
7 Amps Indicator
When this light is on the Digital Display (12)
is indicating the selected Amps (Stick or TIG
Mode).
8 Power On Indicator
9 Over Temperature Indicator
This light is on if the machine overheats
or mains voltage os too high or low – the
machine will prevent weld output until the
machine has cooled down or mains voltage
returns to normal. Welding output can then
recommence.
10 VRD Safe Indicator
This light is on when the machine is in Stick
Mode (MMAW) and the output voltage is
reduced to a safe level.
11 Weld Current & Wire Speed
Adjustment Control/ Inch Button
Stick Mode (MMAW):
This control sets the
Weld Current level.
MIG Mode (GMAW):
This control sets Wire
Speed.
4 Controls
10
9
11 12 13 14
8
7
6
15
16
17
18
19
4
5
3
1