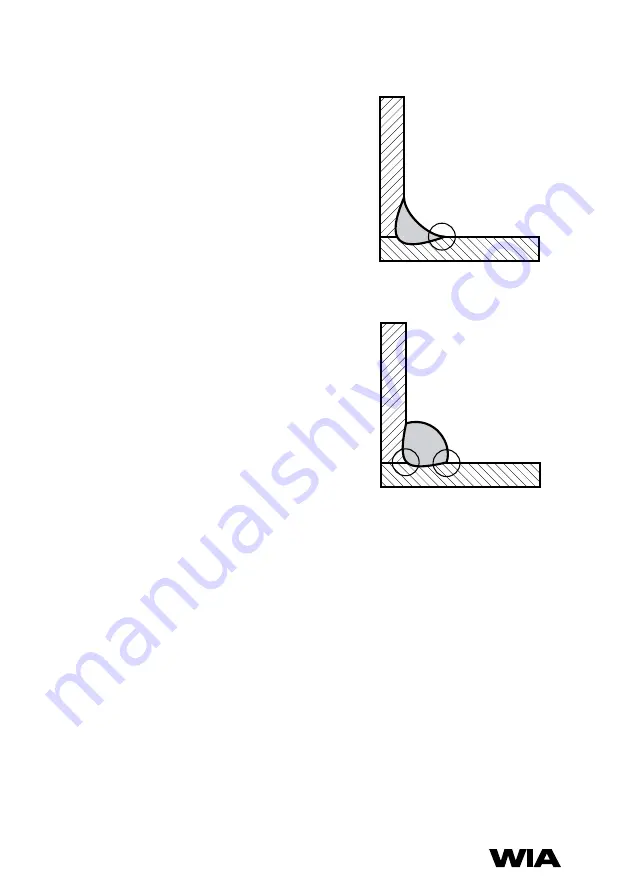
13
12
Establishing a Weld Setting
Once the consumable wire type, wire size
and shielding gas have been chosen, the
two variables that are adjusted in order to
obtain a the desired weld setting are;
– Wirefeed speed,
– Welding arc voltage.
The wirefeed speed determines the
welding current; increasing the speed
increases the current, and decreasing it
decreases current.
The selected wirefeed speed must be
matched with sufficient arc voltage; a speed
increase requires an increase of arc voltage.
If the voltage is too low the wire will stub
and stutter, and there will not be a steady
arc. If the voltage is too high the arc will
be long with metal transfer occurring as a
series of large droplets.
Important: Do not operate the Voltage
Control switches during welding.
The weld setting should be chosen to suit
the application and the thickness of the
metal to be welded. It is important to check
that the deposited weld provides sufficient
strength to suit the application.
A “good” weld will have the characteristics
illustrated in Figure 4. The weld has penetrated
into the parent metal, fusing the root of the
joint where the two plates meet, and the
weld blends smoothly into the side walls.
A “bad” weld is shown in Figure 5. The weld
has not penetrated the joint root, and there
is poor side wall fusion. This lack of fusion
would normally be corrected by increasing
the arc voltage, or by increasing both
wirefeed speed and arc voltage to achieve
a higher current weld setting.
Fig 5 “Bad” Weld
Fig 4 “Good” Weld