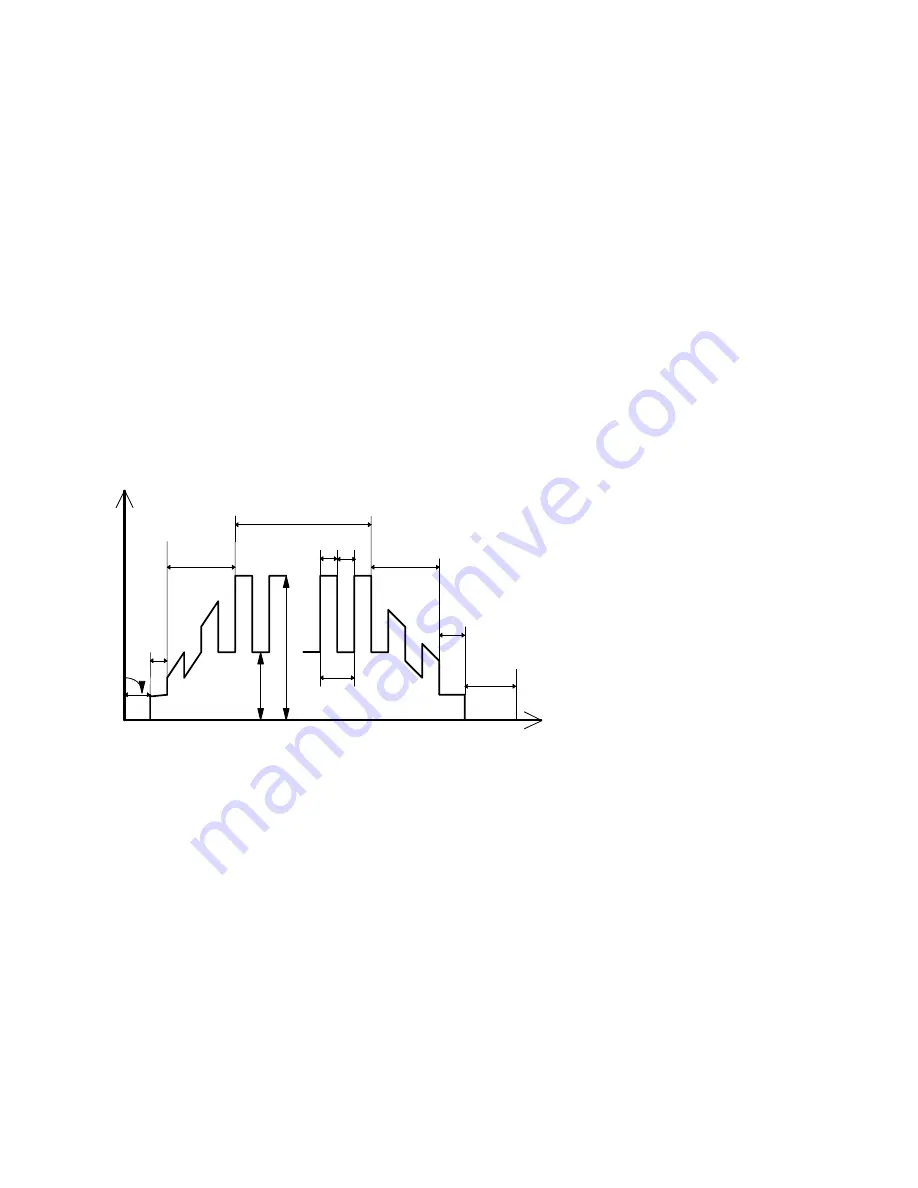
⑥
. Tungsten electrode end is 2-3mm away from the welding workpiece. Press the torch
switch,arc striking will occur.
Notice:
During welding, when the" 12. 2T/4Tswitch"on "2T", switch of the torch must be
pressed and can not be released.otherwise the arc will be broken.
⑦
.Releasing the switch of the torch, welding current will reduce gradually (time is adjustive)
and arc extinguishes.The welding torch can not be removed as soon as the arc extinguishing. Let
the protection gas cooling down for the welding seam not to be oxidized.
⑧
.When the welding operation is finished, turn off argon bottle switch and cut off input power
of the welder.
1.3 PULSE ARGON ARC WELDING
①
. Selection of peak current and base current:
②
. selector "11" onto the position " DC TIG " or "AC TIG "and selector "10" onto the position
" on",
③
.select peak time on ratio: It can be selected between 5%-95%.
④
.select up-slope&down slope time: It can be selected between 0-10S.
⑤
.Gas connecting and testing,are generating and are blowing off etc. are all the same as DC
are welding.
1.4 PULSE ARGON TUNGSTEN WElDING PROCESS (only for reference)
①
.Features and application scope of the process .
The pulse type argon tungsten are welding is different from the continuous(DC) argon are
welding.The welding current is pulsed.The wave form of the current is shown in the following
sketch.Ip and Ib and their continuous time tp and tb can be regulated according to
requirements of the process. The amplitude value of electric current changes periodically with
certain frequency in case of the pulse current, molten base will be formed in the workpiece and
the molten bath will be solidified in care of base current.The welding seam is formed by
reciprocal overlaps. Welding heat input can be controlled by regulating pulse frequency, pulse
current amplitude, size of base current,continuous time of pulse current and base current and
therefore the welding seam,size and quality of the zone influenced from heat can be controlled.
②
.Advantages and application scope of pulse argon gas tungsten arc welding
a. Precisely control the size of the bath inputting heat to workpiece to increase penetration
tp--width time of pulse current
width time of base current
tb--
tp+tb=T
tb
--- = D pulse width
CUR.
(A)
T (s)
t1
gas pre flow
arcing
up-slope
welding process
down-slope
arcing off
post Flow
tp tb
T
Ip
Ib
Ip--pulse current
Ib--base current
tp
Start Amps
End Amps