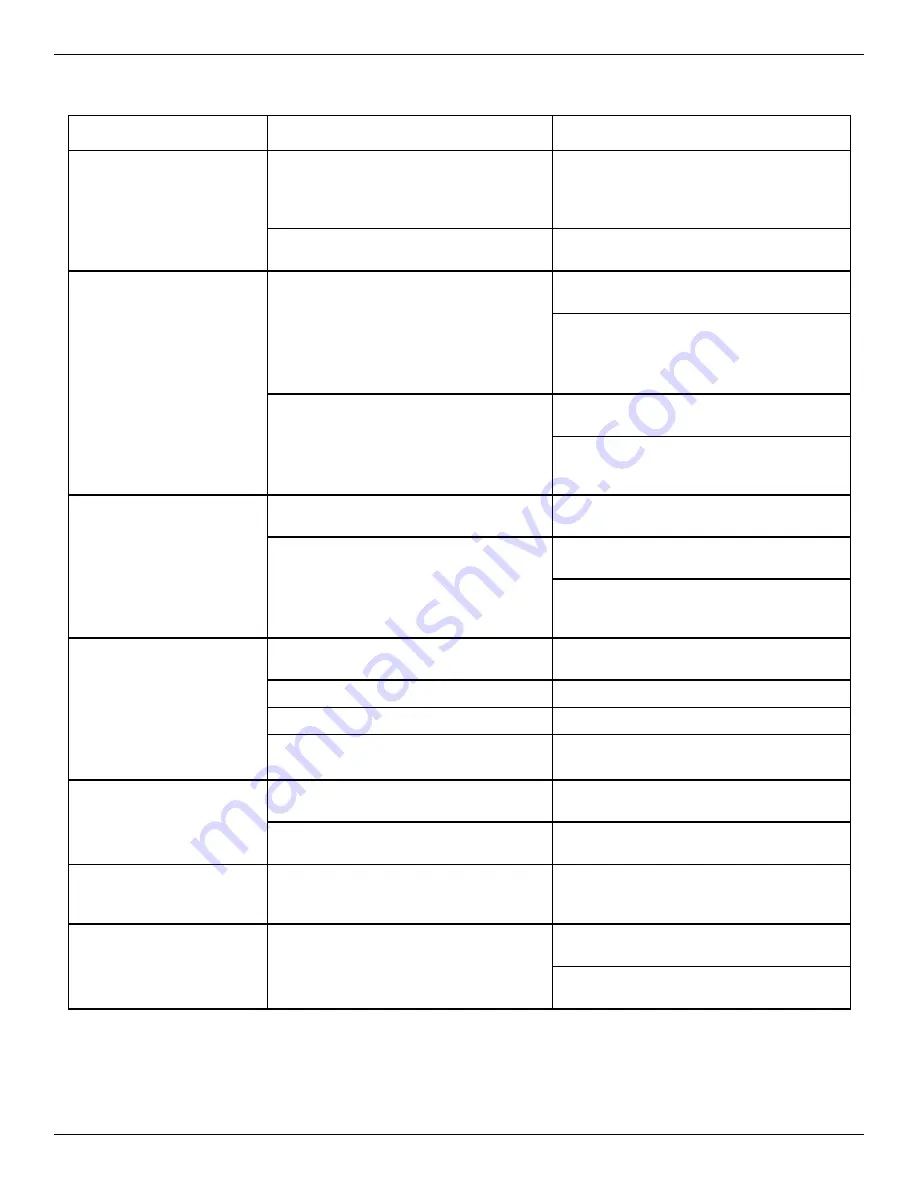
18
Troubleshooting
PROBLEM
CAUSE
CORRECTION
Water has black or gray
color
(NEW SYSTEM) Start up procedure has
not been completed
Run start up procedure (See Page 13) or
run consecutive Clean Rinse cycles (See
Page 15) until water color returns to nor-
mal.
(NOT A NEW SYSTEM) Normal abra-
sion of filtration media
Manually initiate a Clean Rinse cycle
(See Page 15).
Low water pressure at
house faucets
Sediment filter screen is clogged
Manually initiate a Clean Rinse cycle
(See Page 15).
Clean sediment filter screen (See Page
20). If the filter screen is frequently plug-
ging, it may be necessary to adjust the
frequency of Clean Rinse cycles.
Filtration media is fouled
Manually initiate a Clean Rinse cycle
(See Page 15).
If the filtration media is frequently fouling,
it may be necessary to increase the fre-
quency of Clean Rinse cycles.
Water has objectionable
taste and/or odor
System is in bypass
Move bypass valve(s) to normal operating
(non-bypass) position
Filtration media is fouled
Manually initiate a Clean Rinse cycle
(See Page 15).
If the filtration media is frequently fouling,
it may be necessary to adjust the frequen-
cy of Clean Rinse cycles.
No water flow to drain
during Clean Rinse cycle
System is in bypass
Move bypass valve(s) to normal operating
(non-bypass) position.
Drain flow control is plugged
Clean drain flow control (See Page 19).
Drain hose is plugged or kinked
Straighten drain hose.
Transformer is unplugged from wall
electrical outlet (display will be blank)
Check for loss of power and correct.
Clean Rinse cycle does
not run automatically
If display reads “VAC”, then Clean
Rinse function has been disabled
Press and release the CLEAN button until
display no longer reads “VAC”.
If display is blank, transformer may be
unplugged from wall electrical outlet
Check for loss of power.
Clean Rinse cycle does
not run at the pro-
grammed time of day
If time display is flashing, then a long
power loss caused the clock to lose its
time setting
Reset the clock to the correct time of day
(See Page 14).
Valve motor stalled or
clicking
Motor is defective or inner valve defect
is causing high torque on the motor
Replace rotor/seal kit (instructions includ-
ed with kit).
Replace motor and switch (See parts list
at end of this manual).
Summary of Contents for WHELJ1
Page 23: ...23 Notes ...