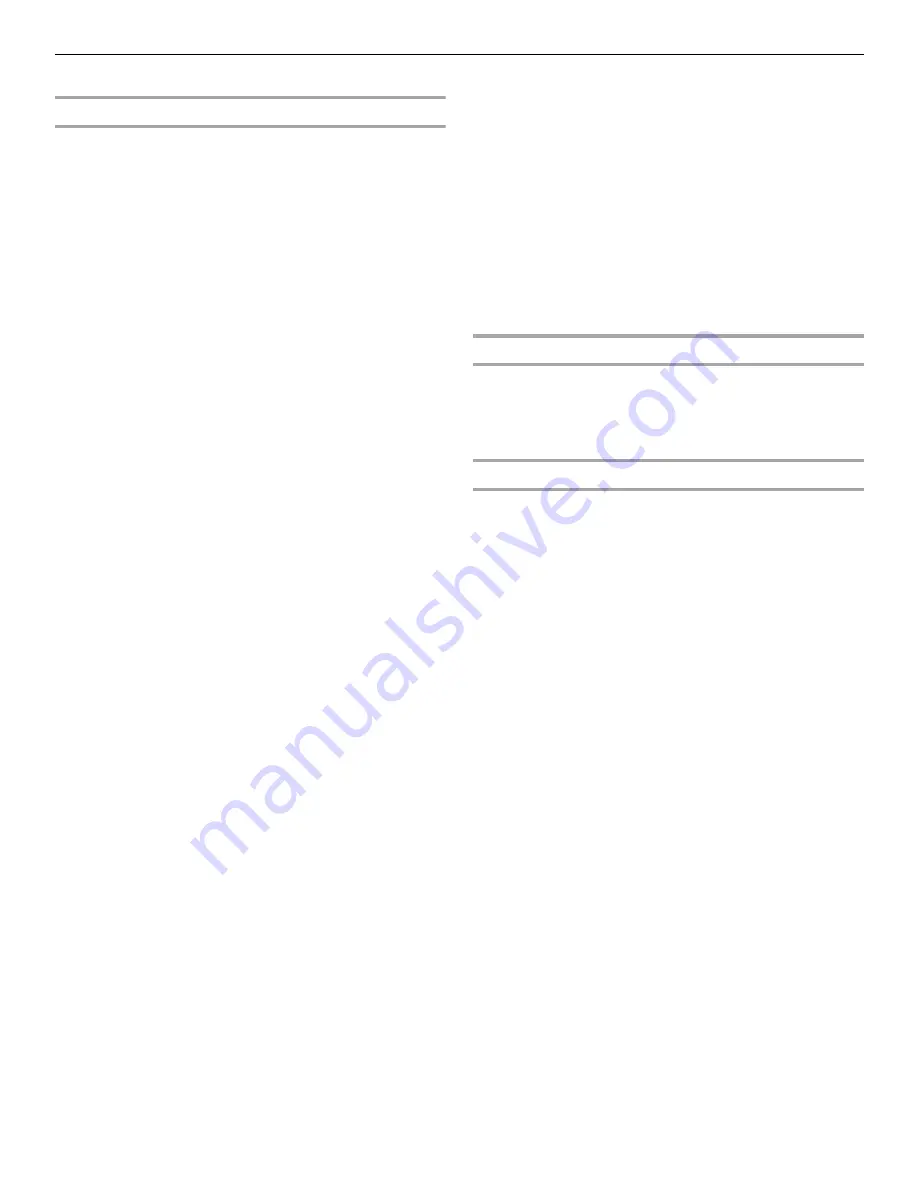
19
Sequence of Operation
Heating
On a call for first stage heat (W1) from the room thermostat, the
ignition control performs a 1-second self-check. Upon
confirmation that the pressure switch contacts are in an open
condition, the ignition control energizes the combustion blower to
high speed. The control then checks for adequate combustion air
by making sure the low-fire pressure switch contacts are closed.
The igniter energizes and is allowed to warm up for 7 seconds
before the gas control valve energizes on first stage and main
burners ignite. 45 seconds after the control confirms ignition has
occurred, the control drops the combustion blower to low speed.
The circulating blower ramps up to 50% of 1st stage heat speed
for one minute (including ramp up time), then at 75% of 1st stage
heat speed for an additional minute. After that, the circulating
blower operates at full 1st stage heat speed until either the heat
call is satisfied or the thermostat initiates a call for 2nd stage
heat. On a call for 2nd stage heat, the control energizes the
circulating air blower on full CFM 2nd stage heat.
If the automatic heat staging option is being used, the furnace
does not switch to 2nd stage heat in response to a call from the
thermostat, but instead operates at 1st stage heat for the
duration of the selected time before automatically switching to
2nd stage heat.
If first stage heating operation is not sufficient to satisfy the
heating demand, the room thermostat initiates a call for second
stage heat (W1 and W2). The control energizes the combustion
blower to high speed and energizes the W1 and W2. When the
high-fire pressure switch contacts close, the gas control valve
energizes on second stage and the circulating blower ramps up
to second stage heat speed.
When the second stage call for heat is satisfied, the ignition
control closes the gas control valve and runs the combustion
blower for an additional 15 seconds. The circulating air blower
continues to run for approximately 120 seconds at 82% of the
selected heating speed, then ramps down to the off mode.
In the event the unit loses ignition, the control will attempt to
recycle up to 5 times before it goes into a 1-hour lockout.
Lockout may be manually reset by removing power from the
control for more than 1 second or removing the thermostat call
for heat for more than 3 seconds.
If during a heating cycle the limit control senses an abnormally
high temperature and opens, the ignition control de-energizes the
gas control valve and the combustion blower while the circulating
blower ramps up to second stage heat speed. The circulating
blower remains energized until the limits are closed.
Fan On
A call for fan from the thermostat closes R to G on the control
board. The control waits for a 1-second thermostat debounce
delay before responding by energizing the circulating blower at
50% of the cooling speed. When the call for fan is turned off, the
control de-energizes the circulating blower.
Cooling
A call for cooling from the thermostat closes R to Y and R to G on
the integrated ignition/blower control board. The control waits for
a 1-second thermostat debounce delay before energizing the
circulating blower to 82% of the cooling speed. After 7.5 minutes,
the circulating blower automatically ramps up to 100% of the
cooling speed. When the call for cooling is satisfied, the
circulating blower ramps back down to 82% of the cooling speed
for 60 seconds, then turns off.
Summary of Contents for WGFBLT
Page 23: ...23 Wiring Schematic DRAIN LOW ...
Page 25: ...25 ...
Page 26: ...26 Notes ...
Page 27: ...27 Notes ...