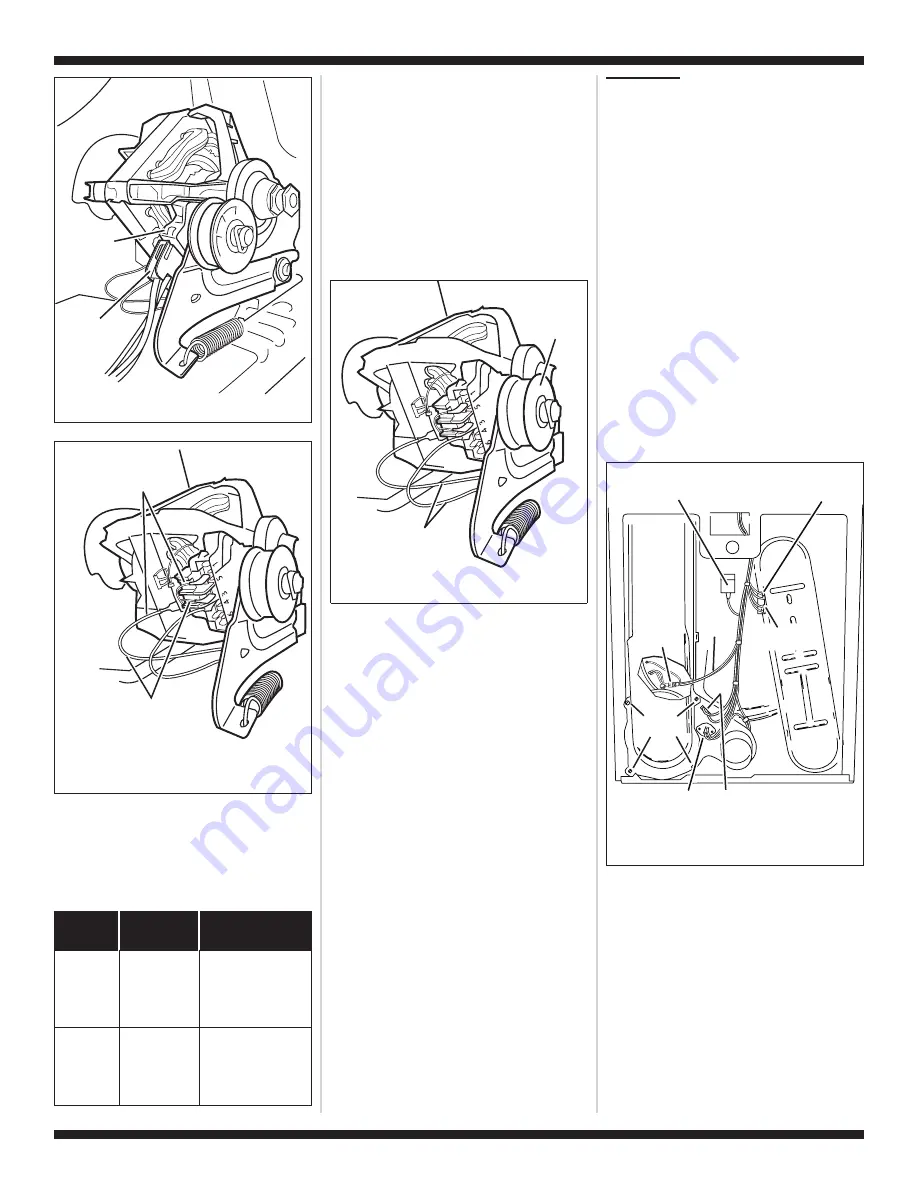
TECH SHEET - DO NOT DISCARD
PAGE 7
FOR SERVICE TECHNICIAN’S USE ONLY
PART NO. W10054160
6.
Using figure 8, check for the resistance
values of the motor’s Main and Start
winding coils as shown in the following
table.
NOTE:
Main and Start winding coils
must be checked at the motor.
WINDING
RESISTANCE
Ω
CONTACT POINTS
OF MEASUREMENT
MAIN
1.4–2.6
Blue wire in back
at pin 4 and bare
copper wire on pin 5
of black drive motor
switch
START
1.4–2.8
Blue wire in back
at pin 4 and bare
copper wire on pin 3
of black drive motor
switch
➔
If the resistance at the motor is
correct, there is an open circuit
between the motor and machine
control electronics. Check for failed
belt switch.
➔
If the Start winding resistance is
much greater than 4 ohms, replace
the motor.
7.
Check the belt switch by measuring
resistance between the two blue wires
as shown in figure 9, while pushing up
the belt switch tension pulley.
➔
If the resistance reading goes from
infinity to a few ohms as pulley arm
closes the switch, belt switch is OK.
If not, replace the belt switch.
➔
If belt switch is OK and there is still
an open circuit, check and repair the
wiring harness.
8.
Door switch problems can be
uncovered in the Door Switch
Diagnostic Test, page 1; however, if this
was not done, the following can be
done without applying power to the
dryer. Connect an ohmmeter across
P8-3 (neutral, white wire) and P8-4
(door, tan wire).
➔
With the door properly closed, the
ohmmeter should indicate a closed
circuit (0–2 ohms).
➔
If not, replace the door switch
assembly. See figure 12, page 10;
and Removing the Front Panel/Drum
Assembly, page 10.
TEST #4
Heater
This test is performed when either of the
following situations occur:
✔
Dryer does not heat
✔
Heat will not shut off
This test checks the components making
up the heating circuit. The following items
are part of this system:
–
Harness/
connection
–
Heater relay
–
High limit
thermostat
–
Thermal cut-off
–
Thermal fuse
–
Gas burner
assembly
–
Centrifugal switch
–
Exhaust thermistor
–
Machine control
electronics. See
ESD information,
page 1.
–
Gas supply
Dryer does not heat:
Locate the components using figure 2,
page 5; and figure 10.
1.
Unplug dryer or disconnect power.
2.
Remove the back panel to access the
thermal components. See Removing
the Back Panel, page 11.
3.
Perform TEST #4b, page 9. If the
thermal fuse is OK, go to step 4.
4.
Perform TEST #4c, page 9. If the
thermal cut-off is OK, go to step 5.
5.
Locate the high limit thermostat. See
figure 10. Measure the continuity
through it by connecting the meter
probes on the red wire and blue wire
terminals.
Main Winding:
Blue Wire in Back and Bare
Copper Wire (5 Position)
Start Winding:
Blue Wire in Back and Bare
Copper Wire (3 Position)
Figure 8.
Main and start winding
measure points.
Belt Switch
Tension Pulley
Blue Wires
(Back and 4 Position)
Figure 9.
Checking the belt switch.
Drive Motor
Switch
White
Connector
Figure 7.
Remove white connector.
4 Duct
Screws
Thermal
Cut-Off (TCO)
High Limit
Thermostat
Harness
Connection
Thermal
Fuse
Sensor
Wires
Drum
Light
Lint
Duct
Exhaust
Thermistor
Figure 10.
Thermal components,
viewed from rear.