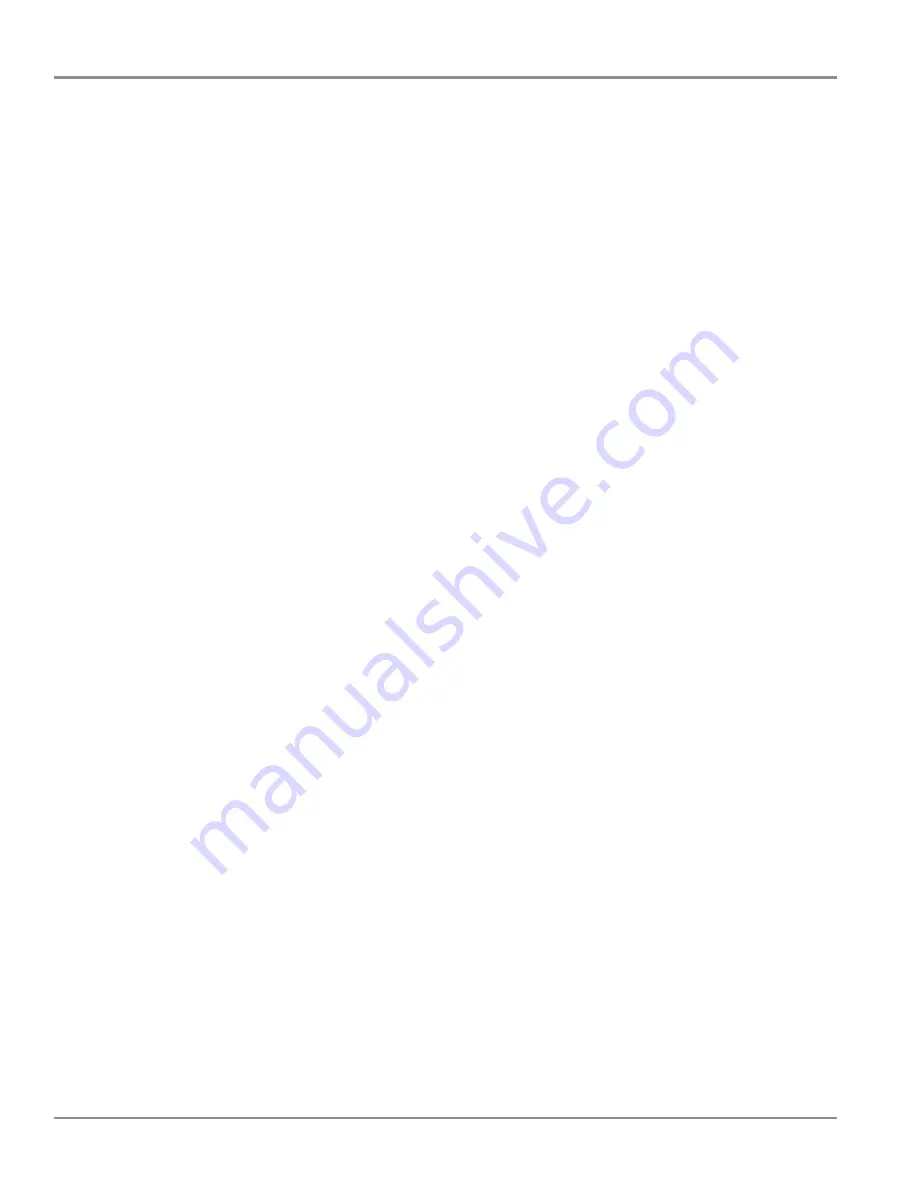
2-2
n
R600A Sealed System
Sealed System Repair
Pre-Work Checks
Pre-Work Checks
Prior to work on an R600a refrigerator, ensure the
immediate area is suitable for working safely, and
the appropriate precautions are in place. Proper
safety checks before beginning work will minimize
the potential for an ignition event. Take the following
precautions before working on the sealed system:
Ensure the area work environment is safe.
•
The work area should be sufficiently sized.
•
R600a refrigerators should not be serviced in small
poorly ventilated spaces such as very small ‘galley’
kitchens, storage closets.
•
Su
g
gested that you not perform sealed system
maintenance in spaces smaller than 6’ X 6’.
•
Refrigerators in insufficiently sized spaces should be
moved to a larger area to work safely.
•
The work area should be properly ventilated. Proper
ventilation allows any refrigerant inadvertently
released to disperse safely.
•
When working behind the appliance, create as
much
clearance as possible between the appliance
and
the wall, or other obstructions, to allow proper
air
movement. Locate the leak detector also behind
the
appliance.
•
Use supplemental ventilation, such as a fan. Ensure
the fan is located at minimum of 9 feet/3 meters
from the nearest sealed system component.
•
Ensure a dry-powder fire extinguisher rated for
Class B fires is accessible on site.
•
Use of a suitable gas detector will alert the
technician of the presence of flammable gas.
•
If flammable refrigerant is detected, immediately
ventilate the room, evacuate the area, and notify
the owner or customer.
•
Recheck with a combustible gas leak detector
before proceeding.
•
If questioned, inform the customer the detector
allows the work to be done safely.
•
Remove any ignition sources from the work area
Disconnect power by unplugging the appliance
before servicing.
•
The area should be free of open flame or burning
materials, including cigarettes, candles, or similar
materials.
•
Do not operate appliances that utilize open flames
or have hot surfaces electric or gas ranges, electric
or gas dryers, toasters, electric or battery powered
tools, and other small appliances while servicing the
appliance.
•
Inform the homeowner/consumer that no open
ignition sources should be present in or near the area,
including cigarette smoking materials.
•
Check the area and the appliance for any signs of
ignition that might have occurred prior to the service.
•
If there are signs of ignition, stop work and ventalate
the work area. Maintain a safe zone around the
appliance during service work to prevent ignition
sources or entry by the customers.
•
An appliance on/off switch, or power button, is not
adequate for removing power, as voltage will still be
present in the unit.
•
Ensure all necessary supplies, tools, and parts are on-
hand.
•
Maintain all equipment in accordance with
manufacturer specifications.
•
Inspect all equipment and hoses for damage prior to
each use. Do not use damaged equipment or hoses.
Sealed System Access
¾
DO NOT access the sealed system by means of cutting
or breaking the sealed system piping.
¾
DO NOT access the sealed system by means of a torch
or any type of open flame.
¾
The sealed system should only be accessed through
the process tube and through the drier.
¾
Quick disconnect fittings must be used when accessing
the sealed system. Use of quick disconnect valves
minimize or eliminate the discharge of any flammable
refrigerant into the work area. Quick disconnect
fittings can be used with Schrader valves, if present, or
with piercing pliers.
¾
If there is no direct means of accessing the sealed
system, use piercing pliers.
¾
If the sealed system is accessed by piercing, ensure the
correct diameter fitting is selected based on the size of
the sealed system pipe.