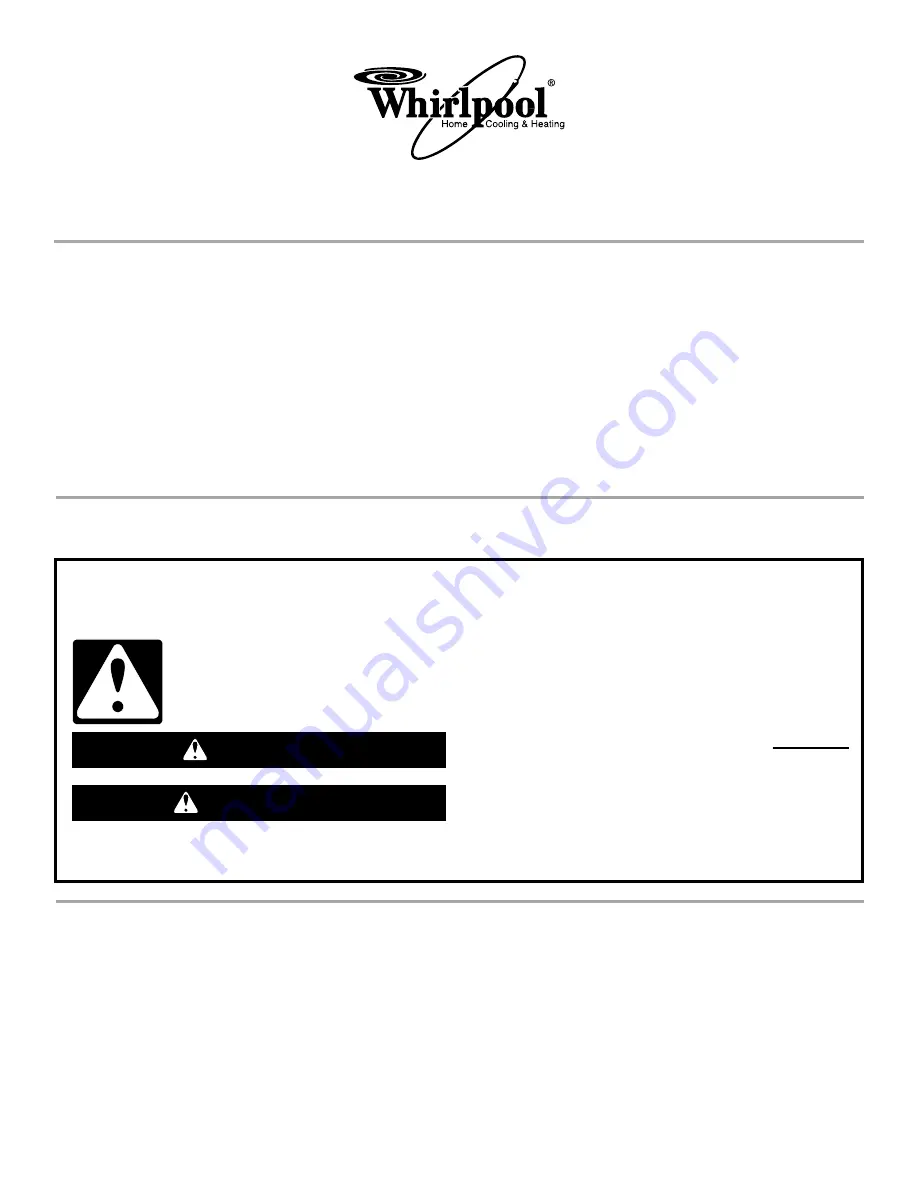
HEAT PUMP INSTALLATION INSTRUCTIONS
HEAT PUMP SAFETY
INSTALLATION REQUIREMENTS
These instructions are intended as a general guide only for use by
qualified persons and do not supersede any national or local
codes in any way. The installation must comply with all state and
local codes as well as the National Electrical Code
■
The heat pump is designed and approved for outdoor use
only.
■
The heat pump must be installed with no ductwork in the
airstream. The outdoor fan is not designed to operate against
any additional static pressure.
Table of Contents
HEAT PUMP SAFETY.....................................................................1
INSTALLATION REQUIREMENTS ................................................1
Tools and Parts ............................................................................2
System Requirements..................................................................2
Location Requirements ................................................................2
Electrical Requirements ...............................................................4
Inspect Shipment .........................................................................4
Flush Refrigerant Lines ................................................................4
Connect Refrigerant Lines ...........................................................6
Make Electrical Connections .......................................................9
Complete Installation .................................................................11
SEQUENCE OF OPERATION ......................................................12
Cooling Cycle .............................................................................12
Heating Cycle .............................................................................12
Defrost Cycle..............................................................................12
Adjust Defrost System ...............................................................13
Troubleshoot the Defrost System ..............................................14
TROUBLESHOOTING ..................................................................15
System Diagnostic Module ........................................................15
SYSTEM MAINTENANCE ............................................................17
ASSISTANCE OR SERVICE .........................................................17
Accessories ................................................................................17
WARRANTY ..................................................................................18
Whirlpool Gold
™
Model W4GH6
48488A006
You can be killed or seriously injured if you don't immediately
You
can be killed or seriously injured if you don't follow
All safety messages will tell you what the potential hazard is, tell you how to reduce the chance of injury, and tell you what can
happen if the instructions are not followed.
Your safety and the safety of others are very important.
We have provided many important safety messages in this manual and on your appliance. Always read and obey all safety
messages.
This is the safety alert symbol.
This symbol alerts you to potential hazards that can kill or hurt you and others.
All safety messages will follow the safety alert symbol and either the word “DANGER” or “WARNING.”
These words mean:
follow instructions.
instructions.
DANGER
WARNING
Summary of Contents for GOLD W4GH6
Page 18: ...18 ...