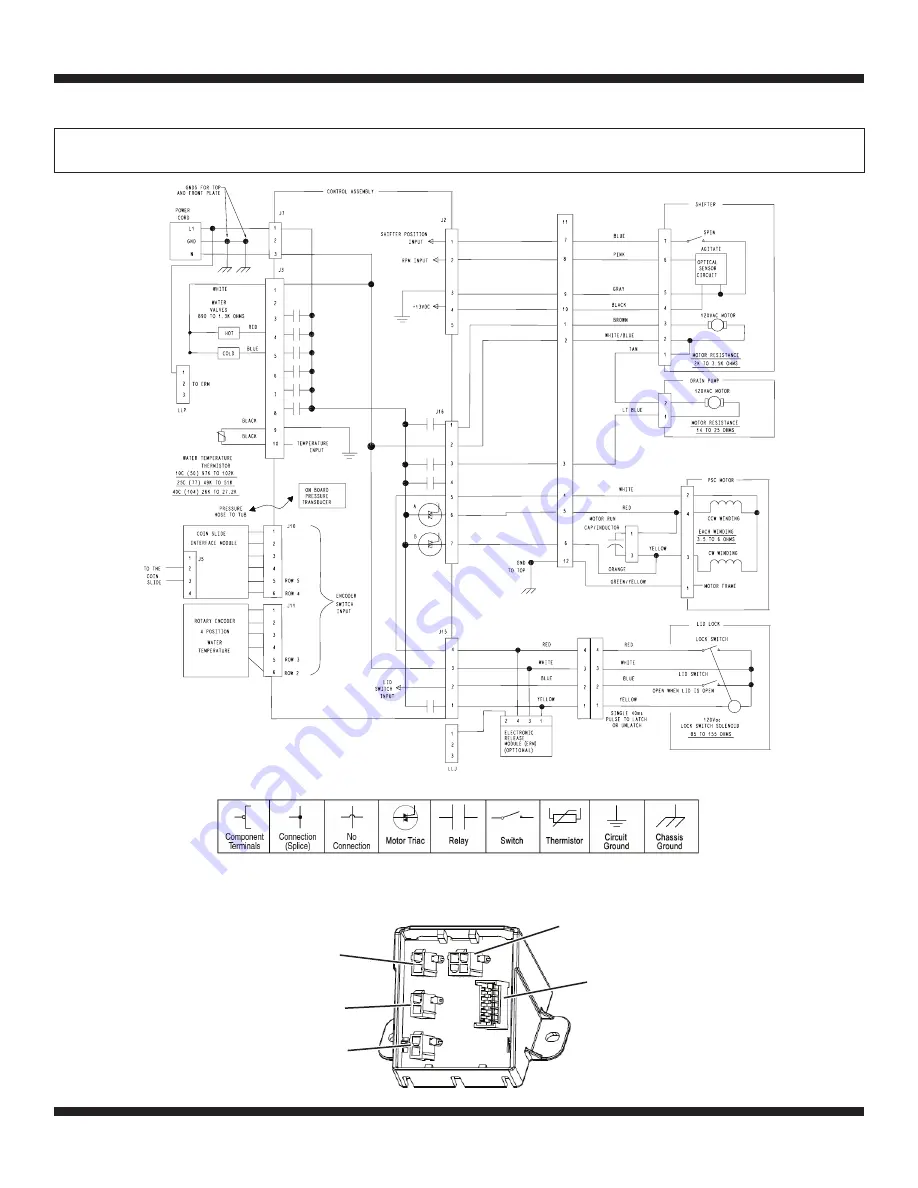
PAGE 20
FOR SERVICE TECHNICIAN’S USE ONLY
DO NOT REMOVE OR DESTROY
Wiring Diagram (No payment system) (Figure 9)
IMPORTANT:
Electrostatic discharge may cause damage to machine control electronics. See page 1 for ESD information.
NOTE:
Schematic shows shifter in SPIN position, lock switch open, and motor off.
Legend
Sets to Pay (jumper loaded)
or No Pay (jumper removed)
Enables Thermistor (jumper loaded)
Disables Thermistor (jumper removed)
Enables DOE Rinse (jumper loaded)
Disables DOE Rinse (jumper removed)
Coin Slide Connection
CCU Connection
Coin Slide Interface Module (Figure 10)