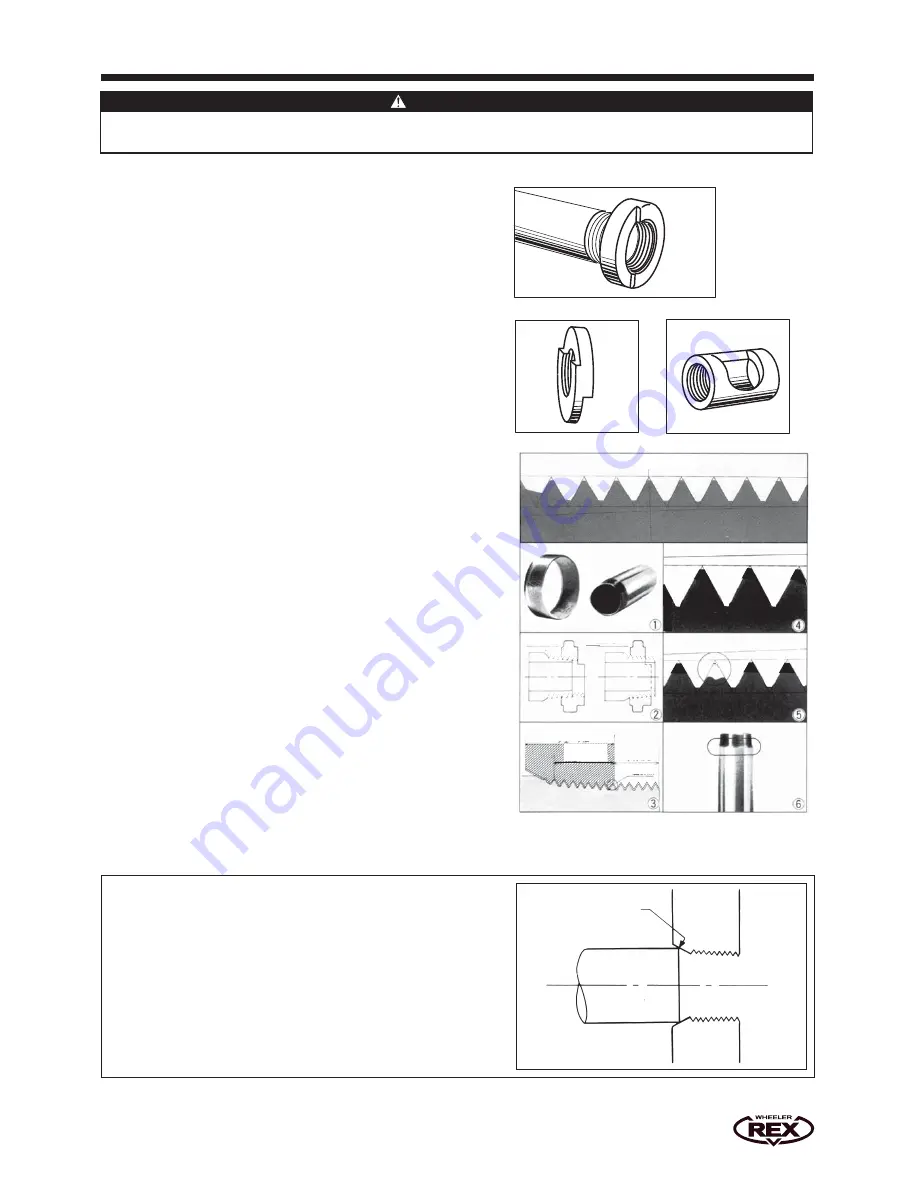
13
(Measuring threads with a gauge / Precautions when threading)
Operation Guide
14. Measuring threads with a gauge
Unacceptable threads
-
Irregular shaped threads (Fig. 32 - 1)
Recognising irregular shaped threads
a
.
Visually inspect the thread after wiping off any oil or dirt with a
rag; you will find a wave-like formation.
b
.
Gently check the surface of the thread with your fingers, feeling
for any irregularity.
c
.
Check if bits of scrap are produced when cutting.
-
The diameter of the thread is too small or too large (Fig. 32 - 2)
Check
with a thread gauge
-
Distorted threads (in the case of manual die heads)
Fig. 32 - 3)
When cutting threads that are wider than the width of the dies,
you can gradually open up the eccentric handle; but then if you
leave the eccentric handle in the same position and cut a thread
longer than the width of the dies, the taper will remain the same
width as the die and the rest of the thread will be straight.
-
Threads are too small (Fig. 32 - 4)
-
The thread is chipped (Fig. 32 - 5)
-
Thread with uneven thickness (Fig. 32 - 6)
Confirming the thread diameter
- Use a thread gauge to confirm the diameter is as it should be.
Threads may be affected by the condition of the dies (blades), cutting oil etc., so be sure to use a thread gauge to
check the thread. This is especially important after you have changed the die set.
Thread gauge
Other pipe thread gauges
Fig. 32
Fig. 29
Fig. 30
Fig. 31
WARNING
Correct thread
Complete
taper thread
Parallel
thread
Angled point
Die width
Wide thread
Narrow thread
Precautions when threading
- Care when the dies come into contact with the pipe (
Fig. 25)
Engage the cutting edge of the dies very lightly with the end of the pipe.
Bringing the dies too forcefully into contact with the pipe will result in
damage to the dies and shorten their working life. Once the dies engage
the end of the pipe, apply light pressure to the carriage handle in a
clockwise direction and then gradually increase the pressure.
As the dies cut into the pipe, it is no longer necessary to apply pressure
to the carriage handle as the carriage will move on its own.
Fig. 33
Dies
Pipe
Cutting edge