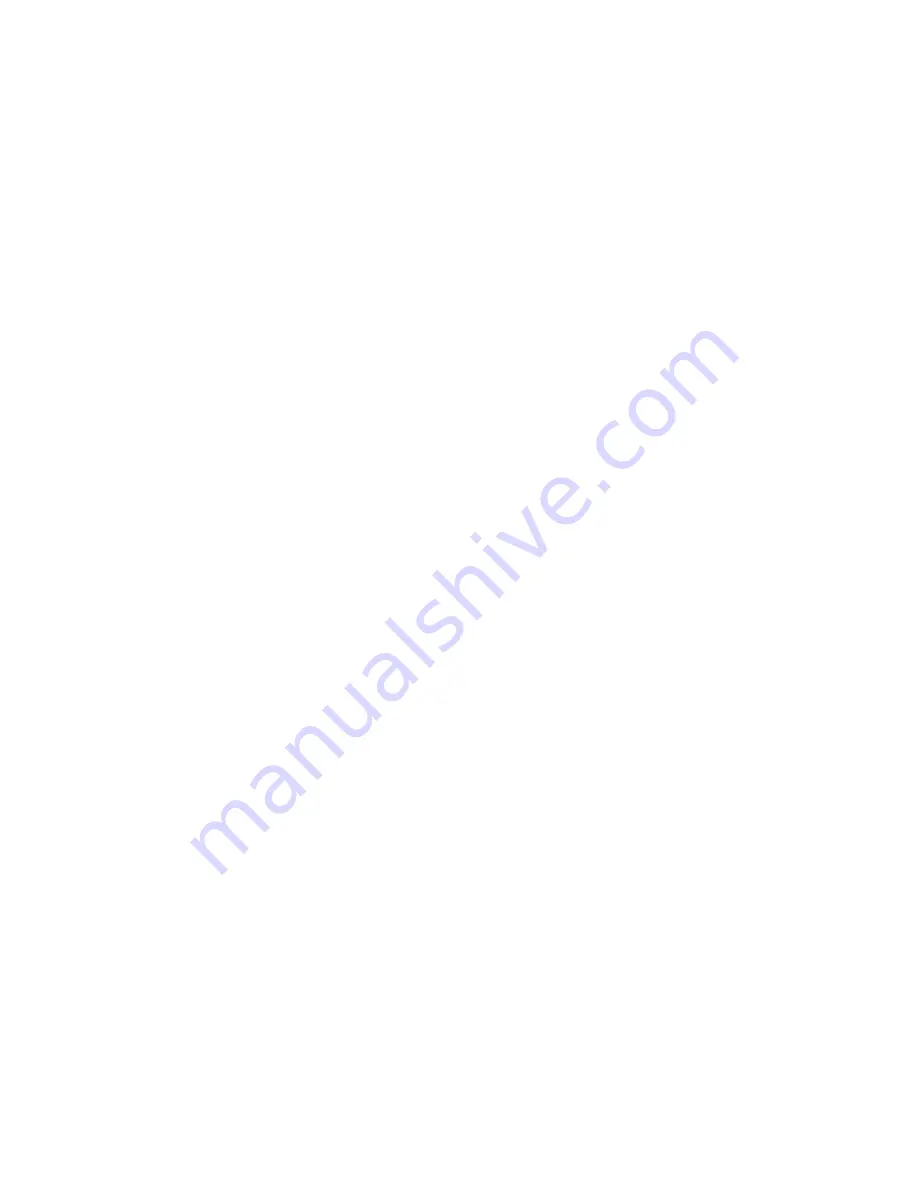
WHL-053 Rev. 00 Rel. 003 Date 7.21.17
41
F. Setting Up a Cascaded System
If the boiler is part of a cascaded system the operation is somewhat
different. The control of each boiler in a cascaded system completes
its own power up system check as described above. One of the
boilers in the cascade system is designated as the master boiler. After
the master boiler completes its power up sequence, it checks the
communication bus to see if any other boilers are present. If other
boilers are present, the master control determines these follower
boiler addresses. The master boiler control will recheck the bus
every few seconds as long as it is powered up to update the status
of the connected boilers. The control in the master boiler processes
all heat demands and dictates which of the follower boilers should
light and what firing rate the followers should try to achieve.
When the master boiler receives a demand for heat, it determines
which boiler is first in the firing sequence and sends that boiler a
command to begin a demand sequence. That boiler will then begin
a demand sequence as described above. Once the boiler ignites, the
master boiler control will increase the firing rate command to that
boiler until the system sensor temperature is at the tank set point
temperature plus the supply offset temperature (installer #4), or that
boiler is at high firing rate. If the command from the master boiler
control gets to the high firing rate of the follower boiler, but the
system sensor is below the required temperature, the master boiler
control will then tell the next boiler in the firing sequence to begin
its demand sequence. The master boiler control will then begin to
ramp up the firing rate command of that boiler. This process will
continue while there is a demand until all boilers in the cascade
system are at high fire or the desired temperature of the system
sensor is reached. If the system sensor temperature reaches tank set
point and installer #4 before all boilers are at high fire, the master
control will modulate the cascade command signal to maintain the
system sensor at tank set point and installer #4 until the demand
is complete. When the tank temperature is equal to the set point
temperature, the demand is complete, and the master boiler control
will extinguish all boilers that may be lit. If the demand decreases,
the firing rate command and amount of boilers lit will decrease
exactly opposite as described above.
Whenever the master boiler control needs to fire a follower boiler,
it sends a firing rate command to that boiler. The follower boiler
will respond to the command until its supply sensor temperature
gets to be 5
o
F above the tank set point temperature plus the supply
offset temperature (installer #4), at which point the individual boiler
will modulate on its own so as not to overheat. As a result, it is not
uncommon to see the cascade output at maximum but individual
boilers firing at less than their maximum firing rate.
G. Lockout Condition
If any boilers, including the master boiler in the cascade system, are
in a lockout condition, the master control will recognize the lockout
condition and skip over the boiler in the firing sequence. Each boiler
in the cascade system is responsible for its own safety functions.
So, if any individual boiler control senses an unsafe condition, it will
extinguish the burner and, if necessary, go to a lockout condition. In
this way, every boiler in the system has its individual safety controls
intact and operational, even if the firing of the boiler is under control
of the master boiler.
In the event that the system sensor fails, all boilers in the system will
ignite simultaneously when there is a demand, and each boiler will
individually regulate firing rates to maintain the master set point
temperature (tank set point + installer #4) at the individual supply
sensors built into the boiler. If this should happen, the master boiler
will display an E03 fault code, indicating that the supply sensor has
failed.
H. Cascade System Programming
1. If the boiler is used alone, skip this section.
2. Programming the Master Boiler:
a. Make sure there is no demand for heat being supplied to the
boiler.
b. Apply power to the boiler.
c. Enter the system setting program navigation following
instructions in Part 10 of this manual.
d. Verify that cascade address function 15 is set to 0. This makes
the master boiler address 0. NOTE: The Master Boiler MUST be
addressed as 0.
e. Change Cascade Mode Function 23 to 928 Boilrs. This makes it
the master boiler.
f. Exit the installer menu.
NOTE:
The temperature set point of the master must match the
follower boiler set point in order for the system to operate properly.
3. Programming Follower Boilers:
NOTE: READ THE NOTES BELOW BEFORE PROGRAMMING
FOLLOWER BOILERS
• The boiler addressed as 1 will share its alarm output with the master
boiler.
• It is recommended but not necessary to address boilers in the order
that they are wired.
• No two boilers can have the same address.
• It is not required to use all consecutive address numbers.
a. Make sure there is no demand for heat being supplied to the
master boiler
b. Apply power to the follower boiler you are working on.
c. Enter system settings following instructions in Part 10 of this
manual
d. Set cascade address parameter 15 to 1 for the first follower, 2
for the second follower, etc. depending on which boiler you are
programming based on the above notes.
e. Change “CASCADE MODE” parameter to “926 BOILRS”. This makes
the boiler a follower boiler and enables all data to be transferred
between boilers as needed for the system to function to full
capability.
f. Exit the installer menu.
NOTE:
The temperature set point of the follower must match the
master boiler set point in order for the system to operate properly.
Once flow through the boiler is adequate, the control will measure
the supply temperature. If it is below the set point temperature
minus the ignition differential set point, the control will ignite the
burner. After the burner is lit, the control modulates the firing rate to
control the supply water temperature at the set point temperature
plus the supply offset temperature (installer #4) above the tank set
point temperature. When the tank temperature is equal to the tank
set point temperature, the control will extinguish the burner and run
the combustion fan to purge gasses from the combustion chamber.
In addition, the pump will run for a pump post purge interval. The
control will then be in standby, waiting to process the next demand
for heat.
During this process, the control will extinguish the burner if it senses
a dangerous or unsafe condition. If the control determines that a
dangerous or unsafe condition has occurred, the control may lock
out the boiler and prevent it from igniting until a maintenance
person diagnoses the problem, repairs it, and resets the control. In
the event that the control goes into lockout, it will show a diagnostic
code on the display, illuminate the LED fault indicator, and close the
alarm relay contacts to aid in recognition of the condition, diagnosis,
and repair.
Summary of Contents for 220VWH
Page 36: ...WHL 053 Rev 00 Rel 003 Date 7 21 17 36 Figure 25 Internal Connection Diagram...
Page 57: ...WHL 053 Rev 00 Rel 003 Date 7 21 17 57 Figure 29 Condensate Detail...
Page 60: ...WHL 053 Rev 00 Rel 003 Date 7 21 17 60 Figure 32 Replacement Parts All Models...
Page 66: ...WHL 053 Rev 00 Rel 003 Date 7 21 17 66 Maintenance Notes...