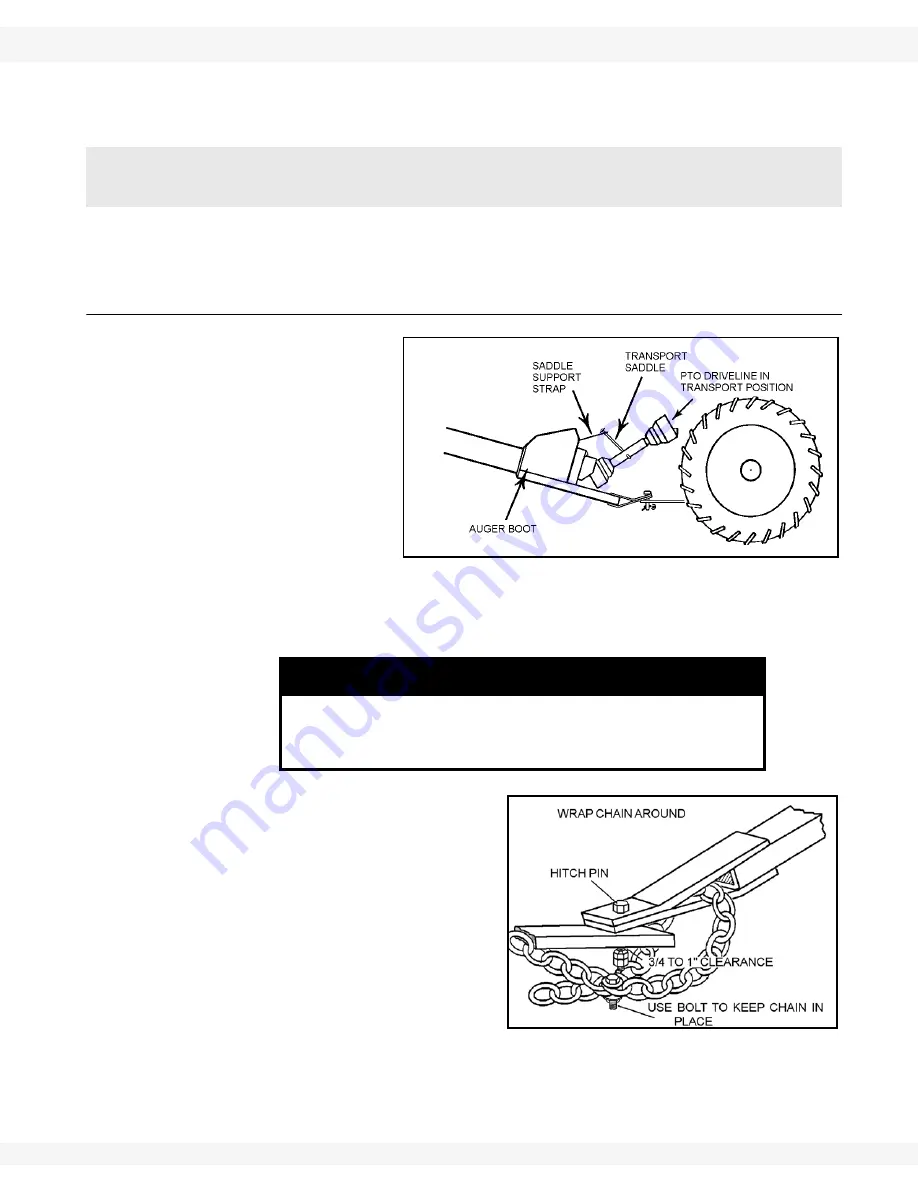
W
ESTFIELD
- G
RAIN
A
UGERS
4. T
RANSPORT
& P
LACEMENT
MK 100/130 P
LUS
X
91’ - 111’
4.1. T
RANSPORT
P
ROCEDURE
30260 R0
43
4. Transport & Placement
This auger is designed to be transported and operated without unhitching unit
from tractor.
4.1. TRANSPORT PROCEDURE
1. Place auger in full
down position.
• Disconnect PTO
driveline from
tractor and
secure in trans-
port saddle, see
Figure 4.1.
• Seat lift-assist
arm against the
track and the
track shoe
against the trackstop with slight tension on the lift cable, see “Lowering &
Completion” on page 53.
2. Position and secure hitch pin
and safety chain. Place safety
chain through clevis welded to
auger hitch tube and bolt
together before attaching to
tractor. Refer to Figure 4.2.
3. Raise intake feed hopper into
transport position and secure
with saddle pin and hairpin.
Use a type of hitch pin that will not
allow auger to separate from towing
vehicle.
Warning:
Before continuing, please reread the safety information relevant to this section at
the beginning of this manual. Failure to follow the safety instructions can result in serious
injury, death, or property damage.
NOTICE
If PTO is not disconnected, driveline will bottom out,
severely damaging the CV u-joint end lower flight shaft. See
manual for maintenance.
Figure 4.1
Figure 4.2
Important: