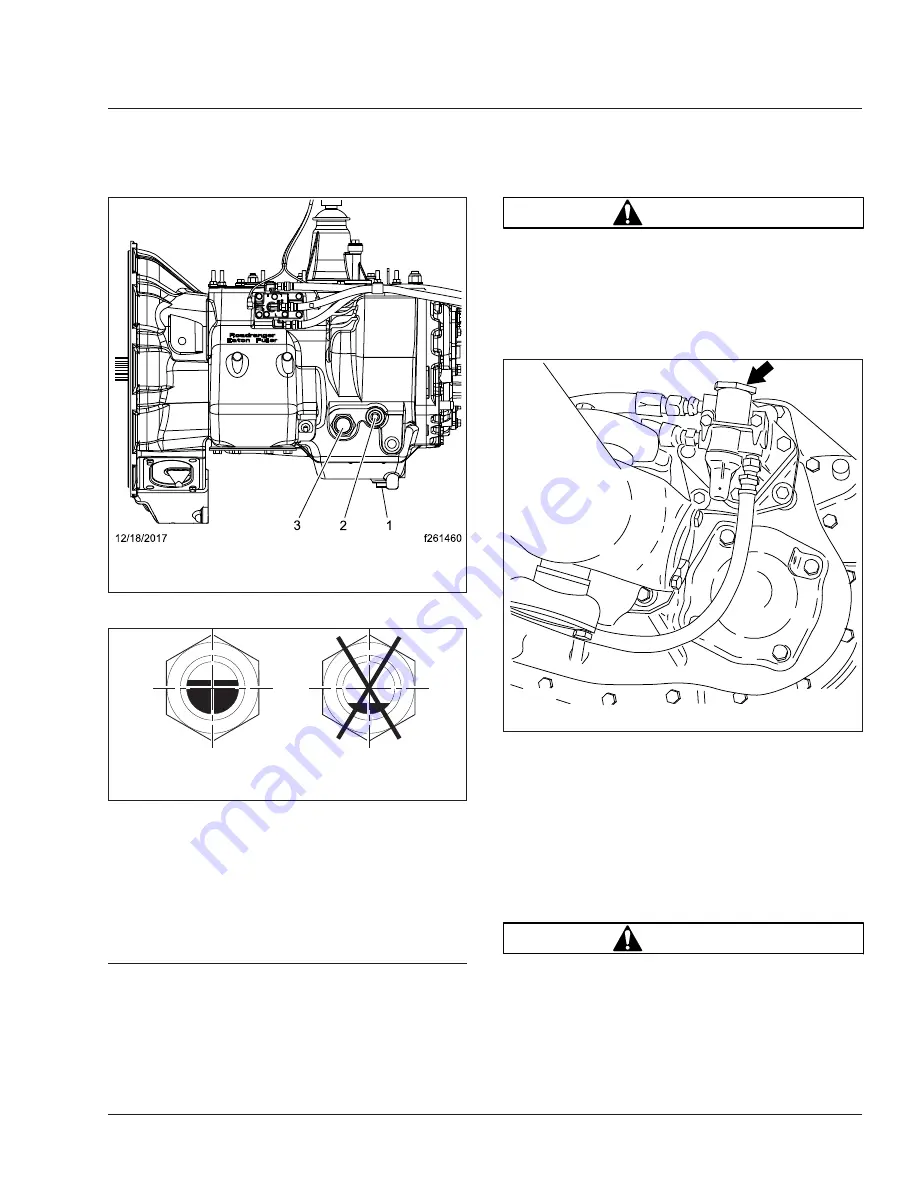
26–05 Eaton Fuller Manual
Transmission Air Filter/
Regulator Check,
Cleaning, or
Replacement
1.
Apply the parking brakes, and chock the rear
tires. Drain the air reservoirs.
WARNING
Drain the air supply; if the air supply is not
drained before the air filter/regulator is serviced,
serious injury and component damage could re-
sult.
2.
Clean the outside of the air filter/regulator with
cleaning solvent. See
3.
Remove the end cap, large O-ring, and filter ele-
ment from the filter housing. See
. Remove
the small O-ring from the end cap.
NOTE: Do not remove, disassemble, or adjust
the air regulator. If the air regulator is not keep-
ing air pressure between 58 and 63 psi (400
and 435 kPa), replace the air filter/regulator. It
cannot be repaired.
WARNING
Wear safety goggles when using compressed air
to clean parts, as permanent harm to eyes could
result from flying debris.
4.
Clean the filter element by dipping it in alcohol or
other cleaning solvent. Blow compressed air
1.
Drain Plug
2.
Fill Plug
3.
Sight Glass
Fig. 3, Eaton Fuller Transmission With a Sight Glass
02/23/2015
f261461
A
B
A. Full
B. Low
Fig. 4, Transmission Fluid Level Sight Glass
f260037a
10/05/2016
Fig. 5, Air Filter/Regulator Location
Transmission
26
47X and 49X Maintenance Manual, June 2021
26/5
Summary of Contents for 47X 2020
Page 2: ......
Page 10: ......
Page 26: ......
Page 28: ......
Page 32: ......
Page 34: ......
Page 36: ......
Page 38: ......
Page 42: ......
Page 48: ......
Page 52: ......
Page 54: ......
Page 62: ......
Page 70: ......
Page 72: ......
Page 78: ......
Page 80: ......
Page 94: ......
Page 96: ......
Page 106: ......
Page 108: ......
Page 110: ......
Page 112: ......
Page 118: ......
Page 132: ......
Page 134: ......
Page 138: ......
Page 144: ......
Page 146: ......
Page 148: ......
Page 150: ......
Page 154: ......
Page 158: ......
Page 166: ......