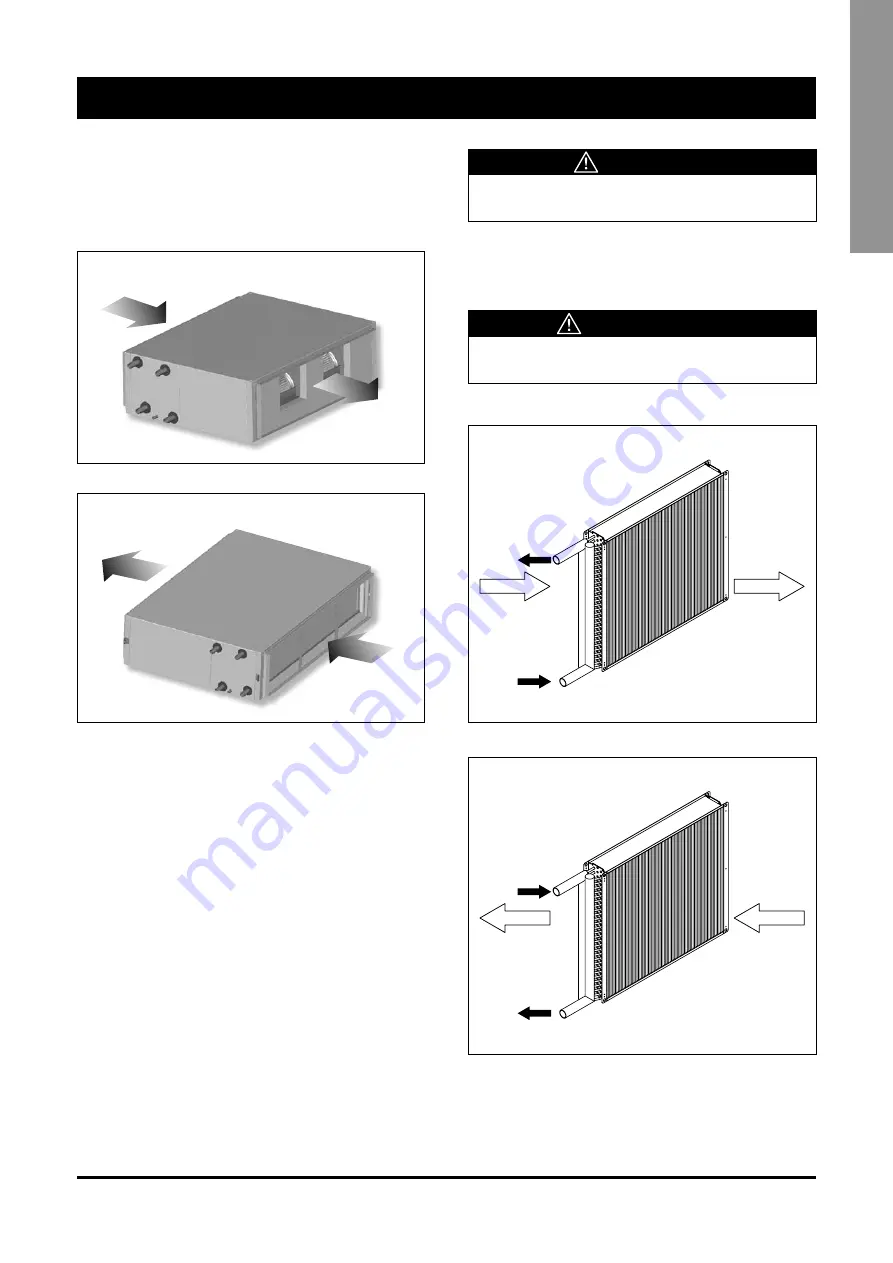
9
English
LEFT-HAND connection
RIGHT-HAND connection
RIGHT-HAND service side
LEFT-HAND service side
7 - Water Connections
7.1 - Definition of the service side
The service side, the side where coil connections are located,
is defined left-hand or right-hand, when observer looks at the
unit from above in the direction of air.
Caution
If the units are not equipped with control valves, the air
temperature must not exceed 50 °C.
Warning
To avoid any damage on coil, use two spanners to tighten
the water pipe fittings on each header.
7.2 - Water coil connections
Each water coil is equipped with headers having Ø33/42
male threaded type connection on water supply and water
return.
Air vent must be installed at highest point of the water
piping.
To ensure an optimum heat transfer efficiency, connections
of water supply and return should be arranged in such
a
way that a counter flow configuration between air and
water is obtained.
Flexible hoses are recommended for coil connections.
Tighten normally the water connections. Note that an
excessive tightening can cause too strong material stresses
at the time of significant temperature changes.
All water lines should be insulated to prevent sweating and
heat loss.
Air out
Air in
Air out
Air in