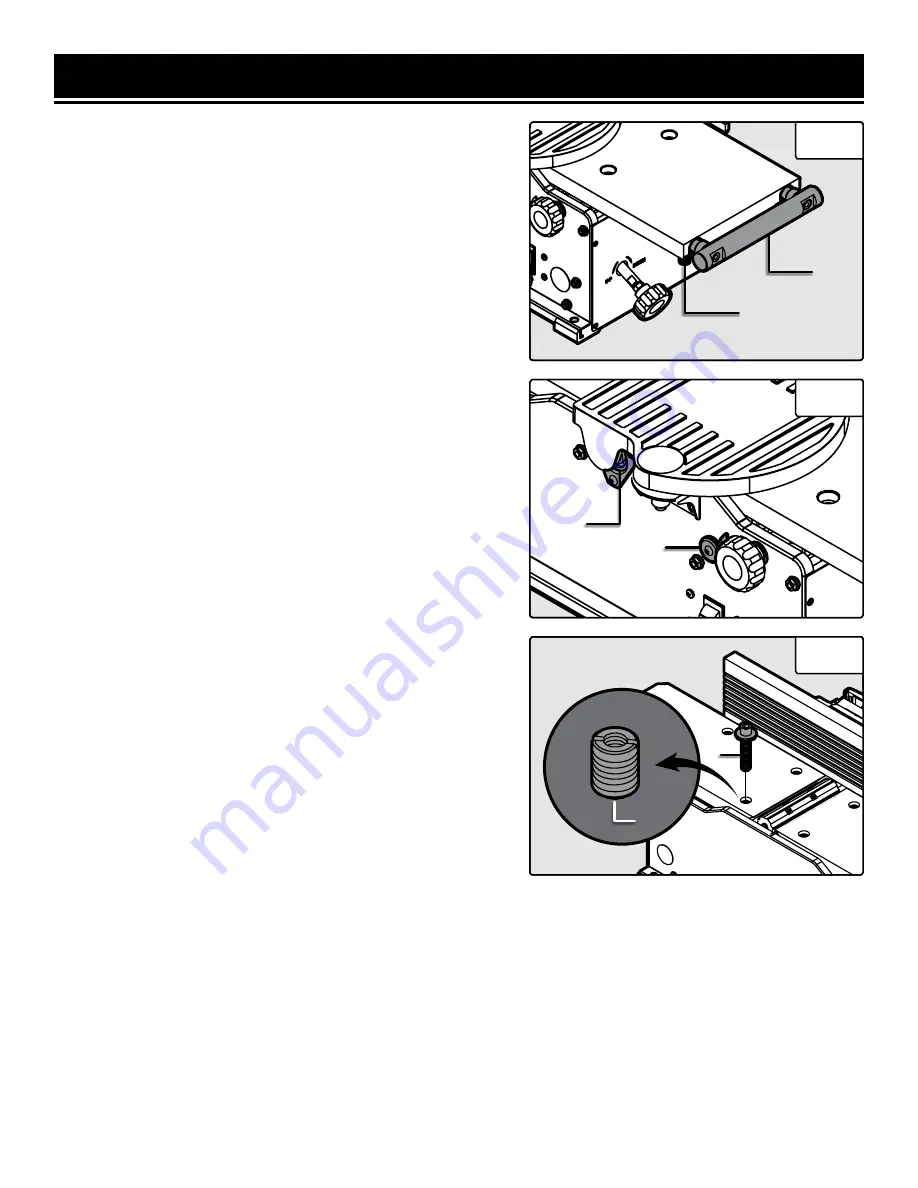
12
ASSEMBLY & ADJUSTMENTS
ADJUST THE TABLE SUPPORTS
The 8” jointer, JT833H, is equipped with a extendable table sup-
ports (Fig. 6 - 1). To extend the supports, loosen the two knobs
(Fig. 6 - 2) on each side of the support bar and reposition the
support to the desired position. Once the support is in the de-
sired position, re-tighten the knobs underneath the table.
ADJUST AND LEVEL THE TABLE
The infeed and outfeed table have been pre-set at the factory to
be level and in line with the blades. However, if shipping or use
has caused the table to shift out of level, adjust the tables with
the following steps. Make sure that the unit is unplugged from
any power supply before adjusting the table.
NOTE:
This procedure involves close proximity to the helical
blades. To avoid cuts, wear cut-proof or cut-resistant gloves
when performing maintenance work. Remove the gloves before
operating the jointer.
1. Set the depth of cut scale (Fig. 7 - 1) to “0” to bring the infeed
table to its most up most position.
2. Rotate the cutterhead such that some of the blades are at
their highest point. The cutterhead can be safety rotated using
the included 4 mm hex wrench at the front end of the cutterhead
under the blade guard flange (Fig. 7 - 2).
3. Use a long metal straight edge to check the height of the
outfeed table. Place the straight edge over the outfeed table and
the cutterhead blades. Check that the blades barely touch the
straight edge at both the front and back of the cutterhead. You
will need to rotate the cutterhead to check both the front and
back alignment of the table.
4. If the blades do not touch the straight edge or drastically hit
the straight edge, the outfeed table will need to be adjusted.
a. Use the included 4 mm hex wrench to loosen and remove
the bolt (Fig. 8 - 1) countersunk in the table. Remove the
washer as well to access the slotted (Fig. 8 - 2) screw under-
neath.
Fig. 6
1
2
Fig. 7
1
b. Use a flat head screwdriver to adjust the slotted screw. Turning the screw clockwise will lift the table up and
turning counterclockwise will lower the table. Adjustments to the screw should be minimal, with only a 1/20th
turn before rechecking the table’s position with the straight edge.
c. Once the table is level and at the correct height, reinstall the washer and bolt to secure the table.
5. Once the outfeed table is set at the correct height, follow the steps above to ensure that the infeed table is at the
correct height.
Directions continue on the next page.
Fig. 8
2
1
2
Summary of Contents for JT630H
Page 19: ...19 EXPLODED VIEW PARTS LIST JT630H...
Page 22: ...EXPLODED VIEW PARTS LIST JT833H 22...
Page 26: ...26 NOTES...
Page 27: ...27 NOTES...