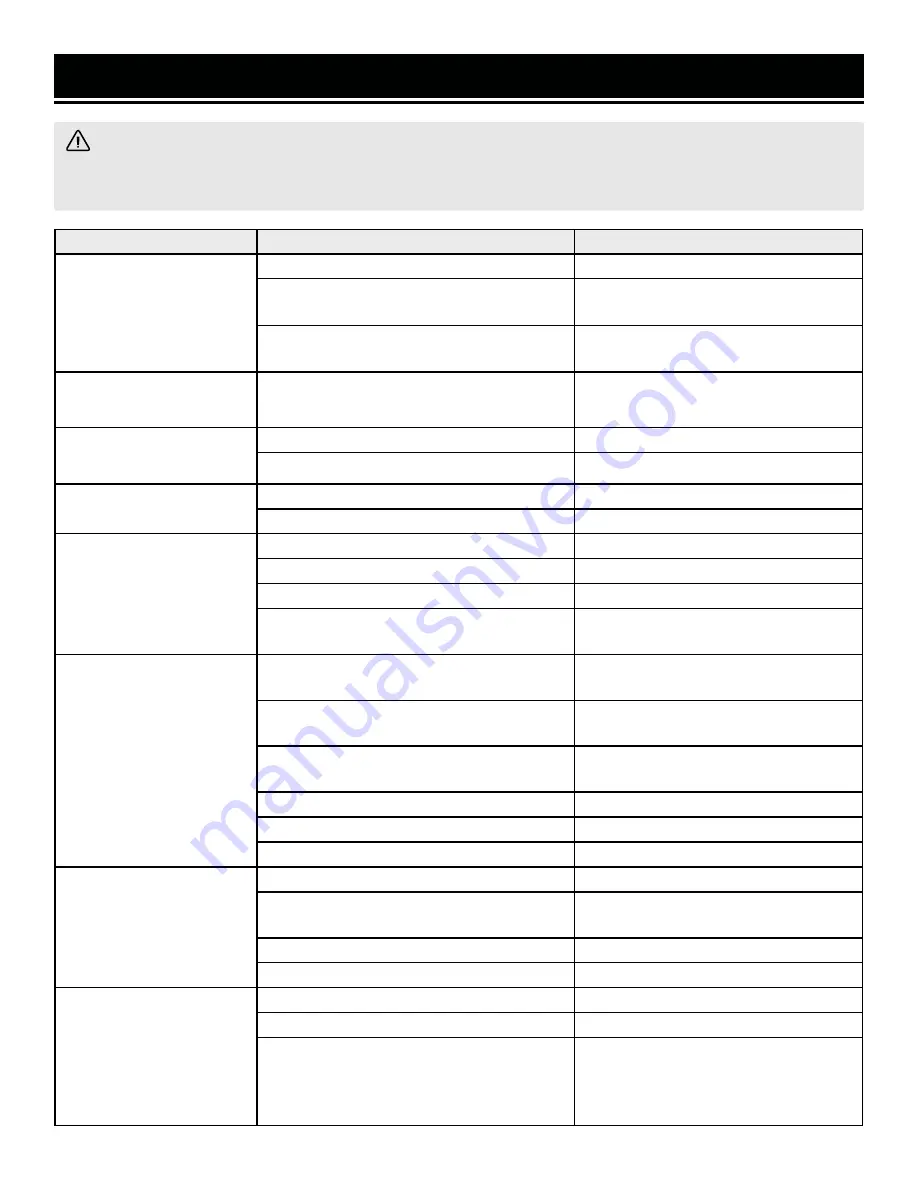
13
PROBLEM
CAUSE
SOLUTION
Air leaking at trigger
area
1. O-ring in trigger valve is damaged.
1. Check and replace O-ring.
2. Trigger valve head is damaged.
2. Check and replace trigger
valve head.
3. Trigger valve stem, seal or O-ring is
damaged.
3. Check and replace trigger
valve stem, seal or O-ring.
Air leaking between
body and drive guide
1. Damaged piston O-ring or bumper.
1. Check and replace O-ring or
bumper.
Air leaking between
body and cylinder cap
1. Screw loose.
1. Tighten screws.
2. Damaged gasket.
2. Check and replace seal.
Blade driving fastener
too deeply
1. Worn bumper.
1. Replace bumper.
2. Air pressure is too high.
2. Adjust the air pressure.
Runs slowly or has
power loss
1. Insufficient oil.
1. Lubricate as instructed.
2. Insufficient air supply.
2. Check air supply.
3. Broken spring in cylinder cap.
3. Replace spring.
4. Exhaust port in cylinder cap is blocked. 4. Replace damaged internal
parts.
Tool skips a fastener
1. Worn bumper or damaged spring (72).
1. Replace bumper or pusher
spring.
2. Dirt in drive guide.
2. Clean drive channel of front
plate.
3. Inadequate airflow to tool.
3. Check hose and compressor
fittings.
4. Worn or dry O-ring on piston.
4. Replace O-ring or lubricate.
5. Damaged O-ring on trigger valve.
5. Replace O-ring.
6. Cylinder cap seal leaking.
6. Replace seal.
Fasteners are jammed
1. Joint guider is worn.
1. Replace joint guider.
2. Fasteners are wrong size or damaged.
2. Use the recommended and
undamaged fasteners.
3. Magazine or front plate screws are loose. 3. Tighten screws.
4. Blade in piston assembly is damaged.
4. Replace piston assembly.
Tool will not drive
down tight
1. Worn blade in piston assembly.
1. Replace piston assembly.
2. Lack of power.
2 . Ad just to adequate air pressure.
3. Slow cycling and loss of power.
3. Check cylinder cap spring for
broken coils or reduced length.
Check if exhaust port of cylinder
cap is restricted.
TROUBLESHOOTING GUIDE
WARNING!
Stop using the tool immediately if any of the following problems occur. Repairs and replace-
ments should only be performed by an authorized technician. For any questions, please contact our customer
service at
1-(800) 232-1195
, M-F 8-5 CST or email us at [email protected].
Summary of Contents for 61722
Page 14: ...EXPLODED VIEW PARTS LIST 14...