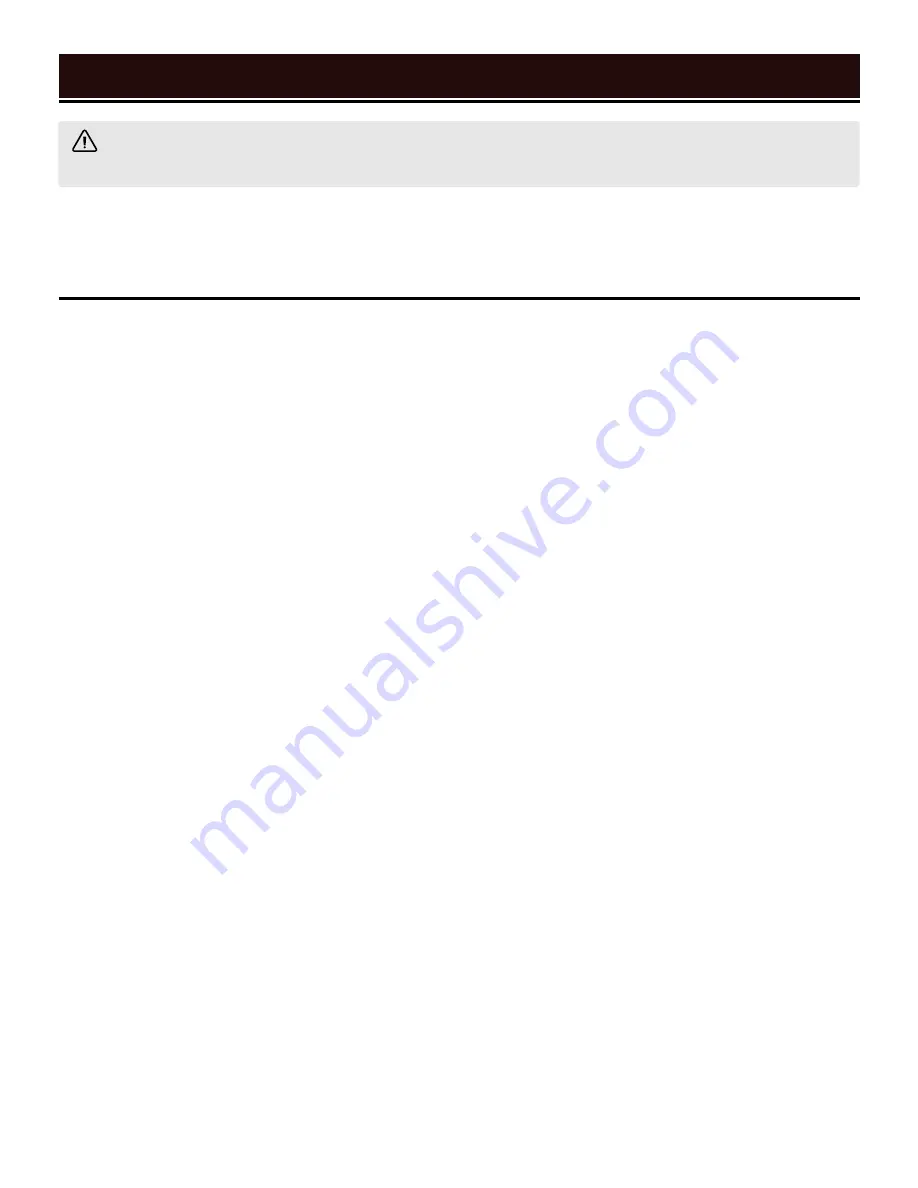
GENERAL SAFETY RULES
4
5
7.
If devices are provided for the connection of dust
extraction and collection facilities, ensure these are
connected and properly used.
Use of dust collection
can reduce dust-related hazards.
POWER TOOL USE AND CARE
1.
Do not force the power tool. Use the correct power
tool for your application.
The correct power tool will
do the job better and safer at the rate for which it was
designed.
2.
Do not use the power tool if the switch does not turn
it on and off.
Any power tool that cannot be controlled
with the switch is dangerous and must be repaired.
3.
Disconnect the plug from the power source and/or
the battery pack from the power tool before making
any adjustments, changing accessories, or storing
power tools.
Such preventive safety measures reduce
the risk of starting the power tool accidentally.
4.
Store idle power tools out of the reach of children
and do not allow persons unfamiliar with the power
tool or these instructions to operate the power tool.
Power tools are dangerous in the hands of untrained
users.
5.
Maintain power tools. Check for misalignment or
binding of moving parts, breakage of parts and any
other condition that may affect the power tool’s opera-
tion. If damaged, have the power tool repaired before
use.
Many accidents are caused by poorly maintained
power tools.
6.
Keep cutting tools sharp and clean.
Properly main-
tained cutting tools with sharp cutting edges are less
likely to bind and are easier to control.
7.
Use the power tool, accessories and tool bits, etc.
in accordance with these instructions, taking into ac-
count the working conditions and the work to be per-
formed.
Use of the power tool for operations different
from those intended could result in a hazardous situa-
tion.
8.
Use clamps to secure your workpiece to a stable
surface.
Holding a workpiece by hand or using your
body to support it may lead to loss of control.
9.
KEEP GUARDS IN PLACE
and in working order.
SERVICE
1.
Have your power tool serviced by a qualified repair
person using only identical replacement parts.
This
will ensure that the safety of the power tool is main-
tained.
CALIFORNIA PROPOSITION 65 WARNING
Some dust created by power sanding, sawing, grinding,
drilling, and other construction activities may contain
chemicals, including lead, known to the State of Califor-
nia to cause cancer, birth defects, or other reproductive
harm. Wash hands after handling. Some examples of
these chemicals are:
• Lead from lead-based paints.
• Crystalline silica from bricks, cement, and other
masonry products.
• Arsenic and chromium from chemically treated
lumber.
Your risk from these exposures varies depending on
how often you do this type of work. To reduce your ex-
posure to these chemicals, work in a well-ventilated area
with approved safety equipment such as dust masks
specially designed to filter out microscopic particles.
Safety is a combination of common sense, staying alert and knowing how your item works. The term “power tool”
in the warnings refers to your mains-operated (corded) power tool or battery-operated (cordless) power tool.
SAVE THESE SAFETY INSTRUCTIONS.
WARNING!
Read all safety warnings and all instructions. Failure to follow the warnings and instructions
may result in electric shock, fire and/or serious injury.