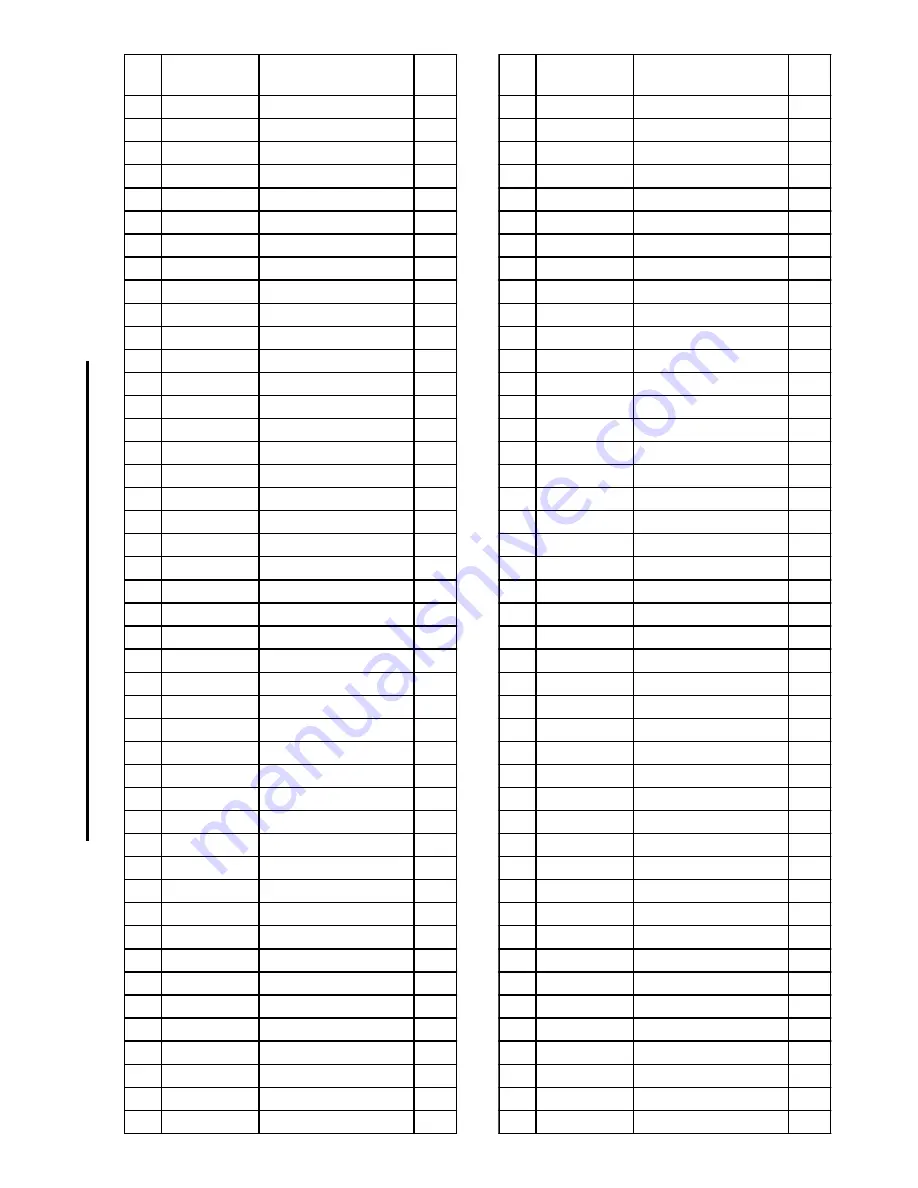
15
EXPLODED VIEW & PARTS LIST
NO.
PART
DESCRIPTION
QTY
1
3960-001
Blade Tension Knob
1
2
3960-002
Flat Washer
1
3
3960-003
Blade Tension Spring
1
4
3960-004
Carriage Bolt
1
5
3960-005
Pulling Plate
1
6
3960-006
Socket Head Screw
1
7
3960-007
Shaft
1
8
3960-008
Lock Catch
2
9
3960-009
Hex Nut
1
10
3960-010
Lock Washer
1
11
3960-011
Bevel Support Plate
1
12
3960-012
Upper Wheel Shaft
1
13
3960-013
Ball Bearing (6000ZZ)
4
14
3960-014
Upper Wheel
1
15
3960-015
Int. Retaining Ring
4
16
3960-016
Ext. Retaining Ring
2
17
3960-017
Tire
2
18
3960-018
Upper Wheel Cover
1
19
3960-019
Blade
1
20
3960-020
Lower Wheel Cover
1
21
3960-021
Lock Nut
2
22
3960-022
Bushing
2
23
3960-023
Socket Head Screw
2
24
3960-024
Lower Wheel
1
25
3960-025
Thread Forming Screw
3
26
3960-026
Drive Pulley
1
27
3960-027
Lower Wheel Shaft
1
28
3960-028
Hex Nut
4
29
3960-029
Hex Bolt
4
30
3960-030
Lock Nut
1
31
3960-031
Lifting Handle
1
32
3960-032
Pan Head Screw
2
33
3960-033
Frame
1
34
3960-034
Switch Box
1
35
3960-035
Pan Head Screw
2
36
3960-036
Switch Mounting Plate
1
37
3960-037
Thread Forming Screw
1
38
3960-038
Switch
1
39
3960-039
Lock Washer
2
40
3960-040
Serrated Washer
2
41
3960-041
Pan Head Screw
2
42
3960-042
Hex Nut
1
43
3960-043
Flat Washer
2
44
3960-044
Bushing
1
45
3960-045
Brush
1
NO.
PART
DESCRIPTION
QTY
46
3960-046
Carriage Blot
1
47
3960-047
Foot
4
48
3960-048
Belt
1
49
3960-049
Dust Port
1
50
3960-050
Pan Head Screw
3
51
3960-051
Lock Nut
2
52
3960-052
Catching Knob
2
53
3960-053
Socket Head Screw
2
54
3960-054
Socket Head Screw
2
55
3960-055
Ball Bearing (606ZZ)
2
56
3960-056
Flat Washer
2
57
3960-057
Support Rod
1
58
3960-058
Socket Head Screw
4
59
3960-059
Ball Bearing (605ZZ)
4
60
3960-060
Flat Washer
4
61
3960-061
Lower Guide Block
1
62
3960-062
Square Nut
4
63
3960-063
Support Block
1
64
3960-064
Socket Head Screw
2
65
3960-065
Flat Washer
2
66
3960-066
Socket Head Screw
2
67
3960-067
Lower Protecting Cover
1
68
3960-068
Flat Washer
2
69
3960-069
Pan Head Screw
2
70
3960-070
Strain Relief
2
71
3960-071
Guide Plate
1
72
3960-072
Set Screw
1
73
3960-073
Pinion
1
74
3960-074
Adjustment Knob Seat
1
75
3960-075
Flat Washer
1
76
3960-076
Socket Head Screw
2
77
3960-077
Adjustment Knob
1
78
3960-078
Upper Guide Block
1
79
3960-079
Support Rod
1
80
3960-080
Flat Washer
2
81
3960-081
Socket Head Screw
1
82
3960-082
Socket Head Screw
1
83
3960-083
Flat Washer
2
84
3960-084
Socket Head Screw
2
85
3960-085
Upper Cover Assembly
1
86
3960-086
Square Nut
1
87
3960-087
Guide Block
1
88
3960-088
Flat Washer
2
89
3960-089
Socket Head Screw
2
90
3960-090
Flat Washer 8mm
1
Summary of Contents for 3960
Page 14: ...14 EXPLODED VIEW PARTS LIST ...
Page 18: ...18 THANKS FOR REMEMBERING ...