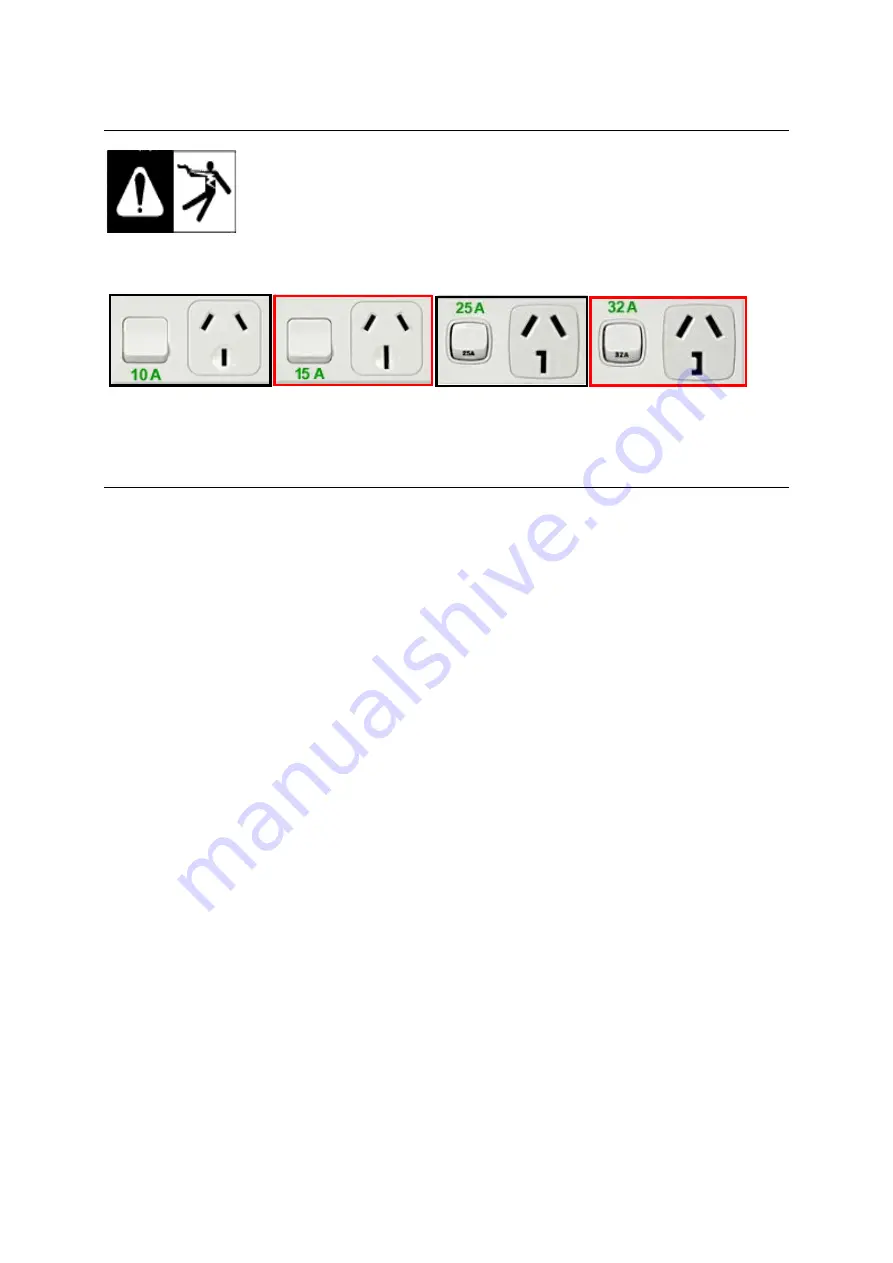
18
Mains supply – 250 MTS Only
The INPUT primary cable is supplied with machine. Connect the machine to mains
according to your state legislation of where machine is being used. Connection can
be effected through plug or direct wiring. Supply system should be protected at all
times by the fuse stated in technical data section. Direct connection to mains can
be done by qualified electrical technician only.
Australian 240V Single Phase Plug variants – AS/NZS 3122
Output connections
Electrode polarity
In general when using the machine for MMAW (Stick) the electrode holder is connected to the
positive (+) terminal and the work return to the negative (-) terminal.
In general when using the machine for GMAW (Mig) the MIG Torch should be connected to the
positive (+) terminal (Euro Connector) and the work return to the negative (-) terminal.
In general when using the machine Gasless Mig the Mig Torch should be connected to the
negative (-) terminal (Euro Connector) and the work return to the positive (+) terminal.
When using the machine for GTAW (TIG) welding the TIG torch should be connected to the
negative terminal (-) and the work return to the positive (+) terminal
Always consult the electrode manufacturer’s data sheet if you have any doubts.
DO NOT USE FITTED FOR COMMISSION
RECOMMEDED TYPE
Summary of Contents for TM250C
Page 2: ...2...