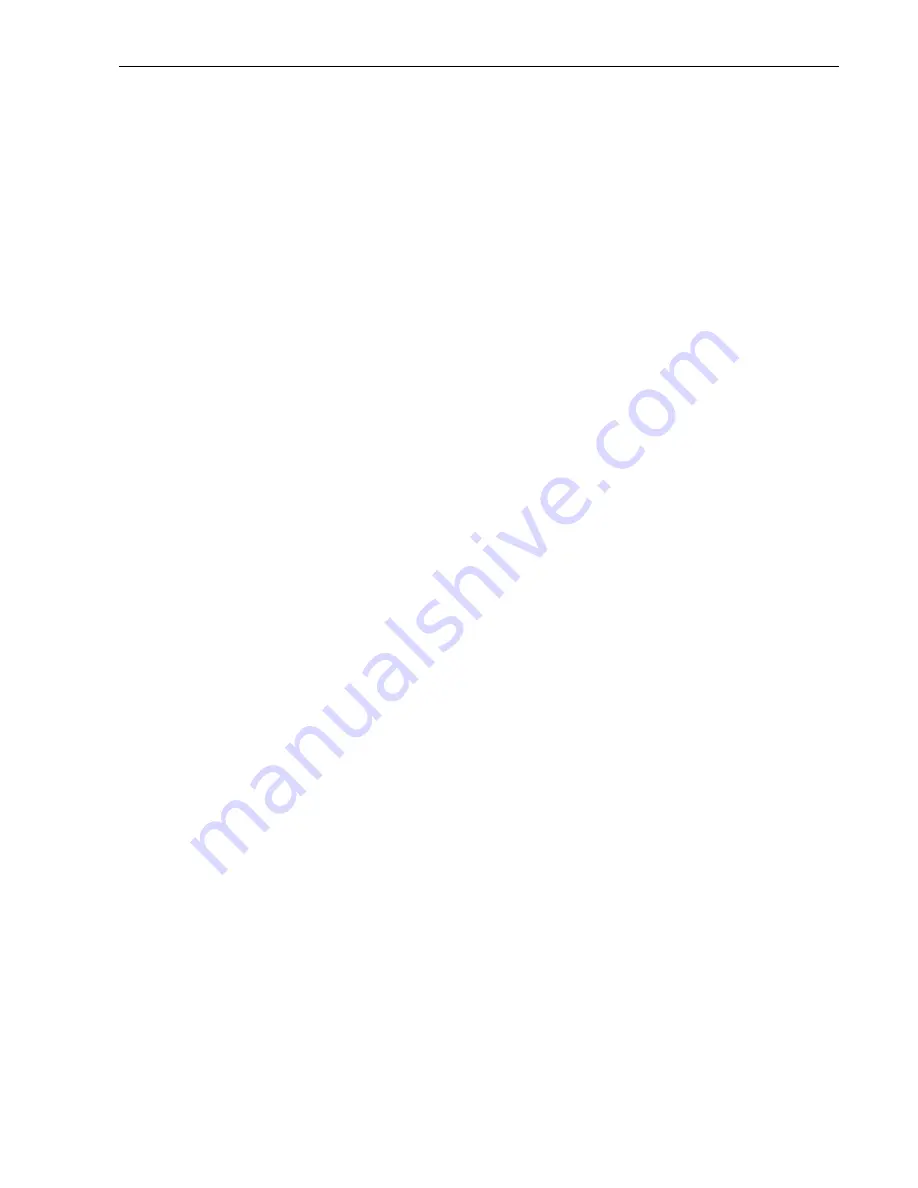
9
WT200MP
Welding Machine
www.weldtech.net.nz
nect the earth clamp to the work piece. Contact
with the work piece must be firm contact with
clean, bare metal, with no corrosion, paint or scale
at the contact point.
5.2 Connect the MIG power connection lead (14) to
the positive welding power output socket (12).
Note if this connection is not made, there will be
no electrical connection to the welding torch!
5.3 Connect the spool gun Euro Connector to the MIG
torch Euro connection socket (1) on the front of
the machine. Secure by firmly hand tightening the
threaded collar on the MIG Torch connector clock-
wise. Connect the spool gun interface plug to the
spool gun connection socket (2). Set the spool gun
switch (3) to ‘on’ position.
5.4 Connect the gas regulator to a gas cylinder (not
included with machine) and connect the gas hose
from the regulator to the gas inlet on the rear of
the machine (15). Ensure all hose connections are
tight. Open gas cylinder valve and adjust regulator,
flow should be between 10-25 l/min depending
on application. Re-check regulator flow pressure
with torch triggered as static gas flow setting may
drop once gas is flowing.
5.5 Set the welding voltage adjustment knob (8), wire
speed control knob (9) and inductance control
knob (10) to the desired positions. You are now
ready to weld!
7. Lift TIG Operation
NOTE:
Lift TIG operation requires an optional valve control
TIG torch, and argon gas cylinder.
7.1 Connect the earth cable quick connector to the
positive welding power output socket (12). Con-
nect the earth clamp to the work piece. Contact
with the work piece must be firm contact with
clean, bare metal, with no corrosion, paint or scale
at the contact point.
7.2 Insert TIG torch power connection into the nega-
tive welding power output socket (13). Connect
valve TIG torch gas line to the regulator, ensuring
all connections are tight.
7.3 Open gas cylinder valve and adjust regulator, flow
should be between 5-10 l/min depending on ap-
plication. Re-check regulator flow pressure with
torch valve open as static gas flow setting may
drop once gas is flowing.
7.4 Connect the machine to suitable mains power us-
ing the mains input power lead (16). Switch the
mains power switch (17) to ‘on’ to power up the
machine. Set the welding mode switch (6) to ‘Lift
TIG’.
7.5 Select the required output current using the cur-
rent control knob (9). You are now ready to weld!
NOTE:
The WT200MP is a DC (Direct Current) output
welder only, this means that it is unable to TIG weld reactive
metals such as Aluminium alloys and Brass (which require
AC output). DC TIG output is suitable for steel, stainless steel
and copper. The New Model is the model in the range that
is designed for TIG welding Aluminium and its alloys.
Tips & Tricks
Duty Cycle Rating
Welding duty cycle is the percentage of actual weld-
ing time that can occur in a ten minute cycle. E.g.
20% at 160 amps - this means the welder can weld at
160 amps for 2 minutes and then the unit will need
to be rested for 8 minutes. All duty cycle ratings are
based on an ambient air temperature of 40°C with
50% humidity, which is the international standard for
such a rating. In an environment with temperature
s exceeding 40°C, the duty cycle will be less than
stated. In ambient temperature less than 40°C, duty
cycle performance will be higher.
6. ARC/ MMA Welding Operation
6.1 Connect the earth cable quick connector to the
negative welding power output socket (13) Con-
nect the earth clamp to the work piece. Contact
with the work piece must be firm contact with
clean, bare metal, with no corrosion, paint or scale
at the contact point.
6.2 Insert an electrode into the electrode holder and
connect the electrode holder and work lead to the
positive welding power output socket (12).
NOTE:
This polarity connection configuration is valid for
most GP (General Purpose) MMA electrodes. There are vari-
ances to this. If in doubt, check the electrode specifications
or consult the electrode manufacturer.
6.3 Connect the machine to suitable mains power us-
ing the mains input power lead (16). Switch the
mains power switch (17) to ‘on’ to power up the
machine. Set the welding mode switch (6) to ‘ARC’.
6.4 Select the required output current using the cur-
rent control knob (9). You are now ready to weld!
Summary of Contents for WT200MP
Page 1: ...OPERATING INSTRUCTIONS WT200MP 200A MULTI PROCESS MIG MMA STICK TIG WELDER www weldtech net nz...
Page 10: ...10 Welding Settings...
Page 24: ...24 MMA Stick Troubleshooting...
Page 27: ...27 WT200MP Welding Machine www weldtech net nz TIG Welding Troubleshooting...
Page 34: ...34...
Page 35: ...35 WT200MP Welding Machine www weldtech net nz...