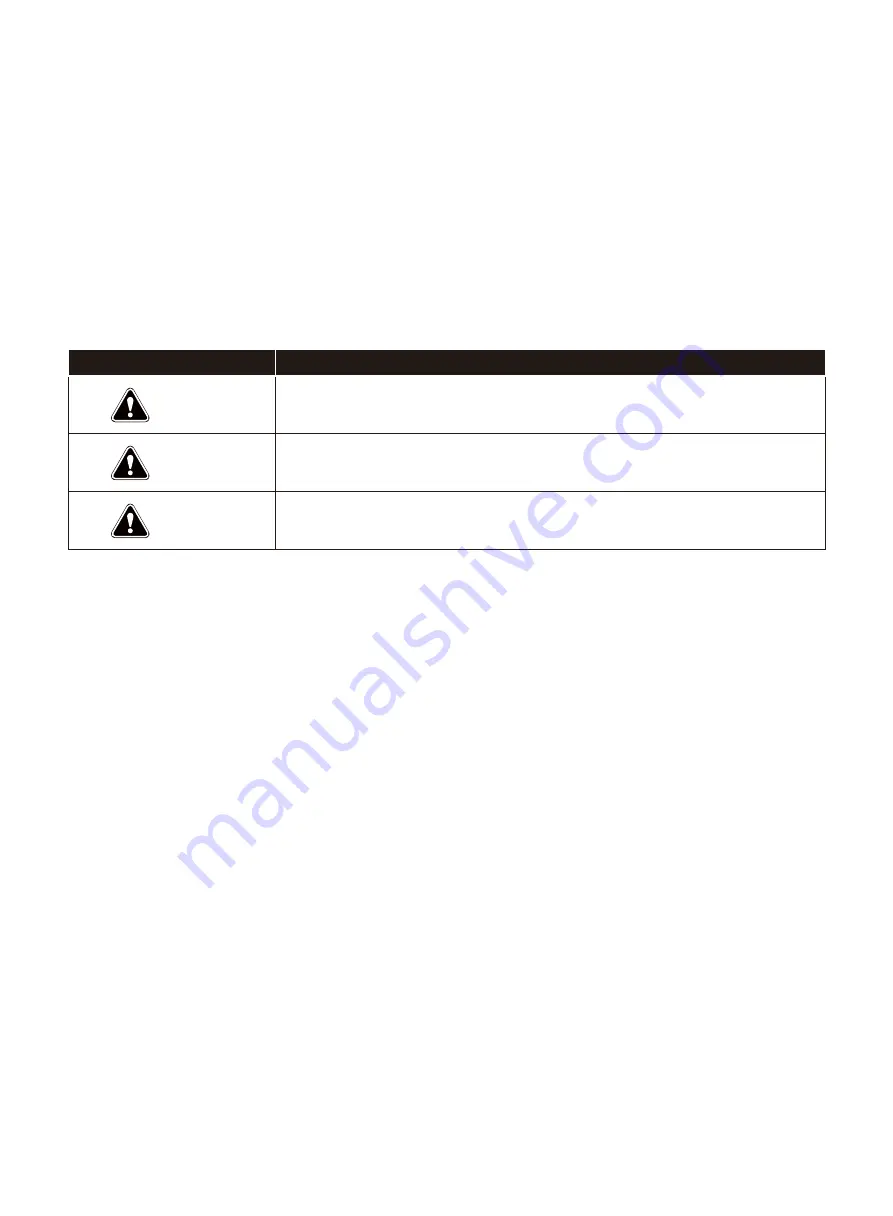
Introduction
Thank you for purchasing the Weldpro MIG155GD welder. This welder is designed and built using the very best quality
components to afford a great welding experience and great performance.
This manual contains the description of the hardware and the operating instructions of the equipment. For your safety and that
of others, please read this manual carefully.
Attention
Pay attention to the words following the signs below.
Sign
Description
The word following this sign means that there is great potential danger, which may
cause a major accident, damage or even death, if the instructions are not followed.
The word following this sign means that there is some potential danger, which may
cause bodily injury or property damage, if the instructions are not followed.
The word following this sign means that there is potential risk, which may cause
malfunctions and/or breakdowns, if the instructions are not followed.
DANGER
WARNING
ATTENTION
Edition
The contents of this manual are updated regularly in order to include all product updates. The manual is to be used solely as a
user’s guide, except where indicated otherwise. No warranties of any kind, whether expressed or implied are made in relation to
the information, descriptions, suggestions or any other content of the manual.
The images of this manual are for reference only. If there is any inconsistency between the image and the actual product, the
actual product will govern.
3